Effectively sealing stainless steel pipe threads is critical in ensuring leak-proof connections within various industrial and residential applications. While stainless steel is renowned for its durability and resistance to corrosion, improper sealing can compromise even the most robust of systems. Understanding the nuances of working with stainless steel pipe threads can enhance both short-term and long-term system performance.
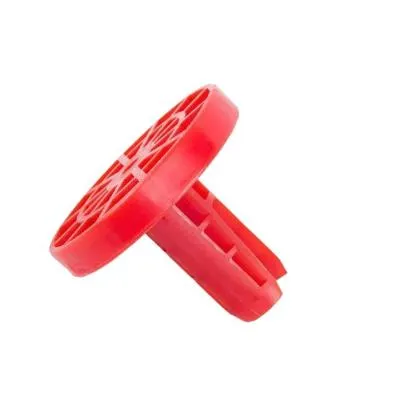
Stainless steel pipe threads are often used in environments where corrosion resistance and pressure handling are paramount. This could include chemical processing plants, oil and gas industries, and even in certain residential plumbing systems. However,
the inherent hardness of stainless steel poses unique challenges when sealing. Threads can gall or seize—a phenomenon where metals stick together under pressure. This occurs due to the similar hardness profiles of stainless steel fittings and pipes.
A seasoned professional with hands-on experience knows that using the right sealing techniques and materials is essential. Thread sealants, often referred to as thread dope, are commonly used. These come in different formulations, including Teflon-based compounds and other synthetic variants. Teflon tape, a widely known solution, is popular due to its ease of use and effectiveness. However, it is crucial to select Teflon tape specifically designed for stainless steel applications, as the standard versions may not suffice, leading to potential leaks.
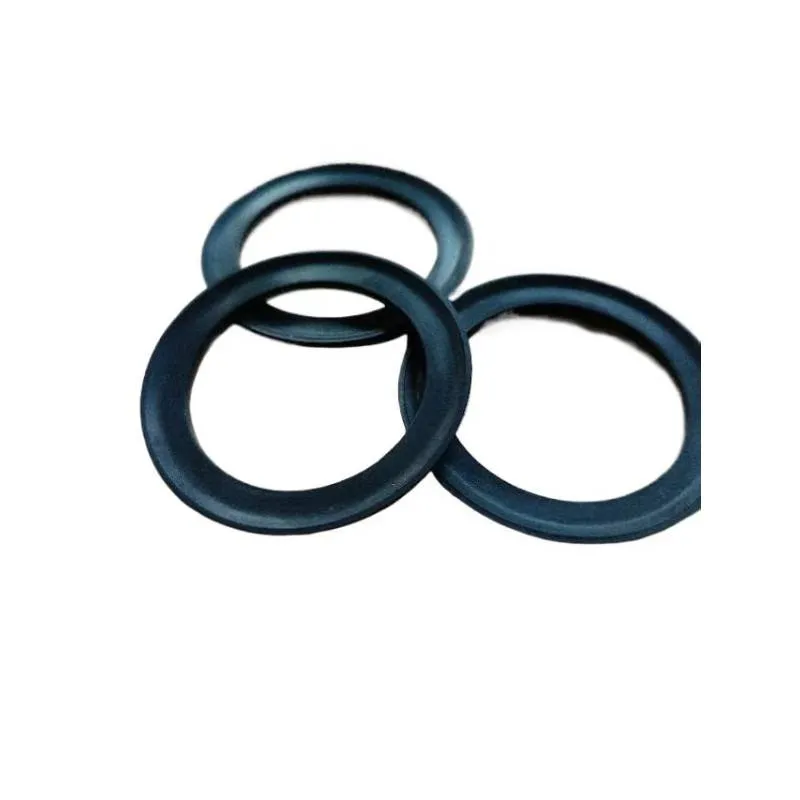
Advanced expertise emphasizes the importance of clean threads. Dirt, debris, and even oil can prevent a good seal. Thus, cleaning the threads with a solvent before applying a sealant is recommended. Moreover, professionals advocate for multiple wraps of Teflon tape in the direction of the thread, followed by a thin layer of thread sealant for added security.
In terms of trustworthiness and authority, industry standards suggest that threads should be cut with precision. Poorly cut threads can lead to diminished sealing performance. Leveraging quality tools and ensuring that threads meet the American National Standard Pipe Thread standards (NPT) are critical steps. Engaging with manufacturers who adhere to these standards adds a layer of reliability and ensures that components interact seamlessly.
sealing stainless steel pipe threads
For those seeking expertise in uncommon scenarios, such as extreme pressure or temperature applications, high-performance liquid thread sealants can be the solution. These offer superior adhesion and, when cured, provide a seal that withstands the arduous demands of heavy-duty industrial use. Consulting manufacturer guidelines when selecting a sealant ensures compatibility with the operating environment.
Trust in a system comes from knowing that all components, including the sealing process, are up to standard. Usage of anti-seize lubricants is often recommended alongside thread sealants to prevent galling effectively. Anti-seize compounds contain metallic or composite powders that dramatically reduce the risk of thread seizing under pressure—especially crucial in high-temperature and high-pressure environments.
Experience dictates that testing is a non-negotiable step in the sealing process. Responsible professionals advocate for hydrostatic testing post-installation to identify and rectify any leaks early in the process.
In addition, being aware of the latest product innovations and technological advancements in thread sealing can significantly enhance performance. Adopting new product lines that focus on sustainability and environmental safety can also align with broader corporate responsibility goals.
Ultimately, the successful sealing of stainless steel pipe threads demands a blend of experience, expertise, authoritative knowledge, and trust. By diligently applying these principles, systems will not only stand up to rigorous demands but also sustain longevity and reliability over time. Always seek out industry guidelines to ensure both safety and efficiency in your applications.