Sealing metal to metal is a critical process in various industries, from automotive to aerospace, and even in home appliances. Achieving a reliable seal is paramount to ensure the longevity and functionality of components. This process, although seemingly straightforward, demands meticulous attention to detail and technical expertise.
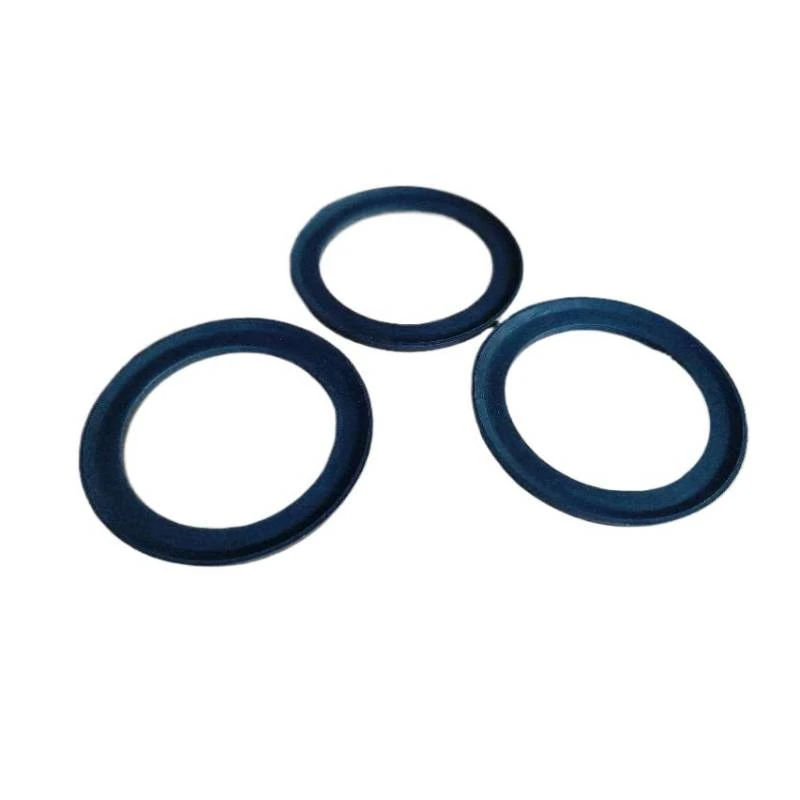
The journey to master metal-to-metal sealing begins with understanding the properties of the metals involved. Different metals exhibit varying levels of thermal expansion, corrosion resistance, and mechanical strength. For instance, sealing aluminum to steel involves compensating for aluminum's higher thermal expansion without compromising the structural integrity of the steel. This necessitates the selection of appropriate sealing materials and techniques that complement the characteristics of both metals.
In many instances, gaskets serve as the intermediary in metal-to-metal seals, preventing leaks while accommodating slight surface irregularities. However, not all gaskets are created equal. Metallic gaskets, such as spiral wound gaskets, offer robustness and can withstand high temperatures and pressures, making them ideal for industrial applications. Non-metallic gaskets, while versatile and easier to handle, may not provide the same durability or resistance needed for extreme conditions.
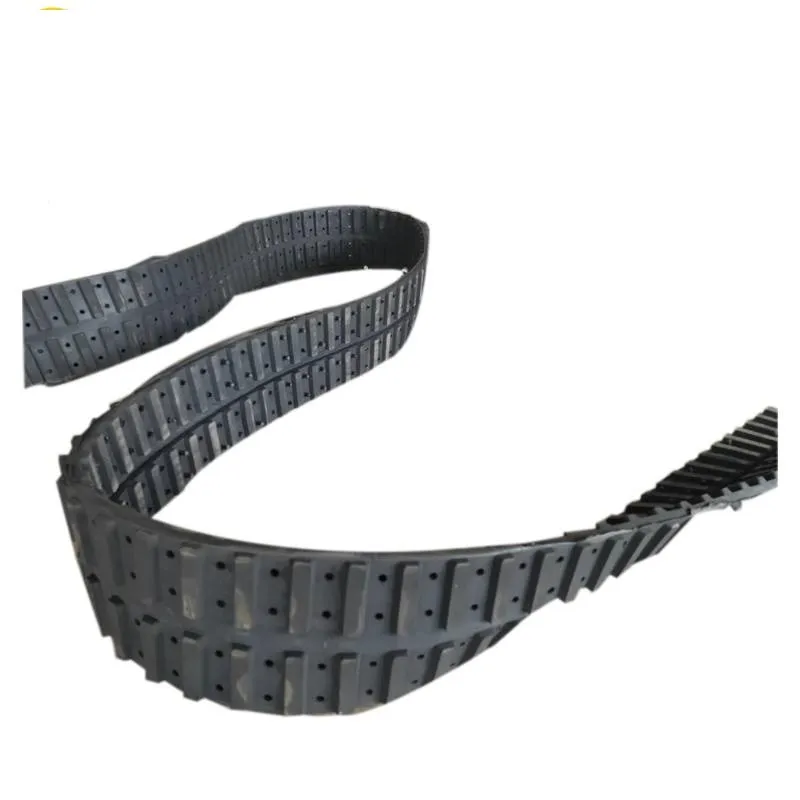
Beyond gaskets, the method of joining is crucial. Traditional techniques like welding or soldering are commonly employed, yet they require precision and skill. Improper welding can introduce weaknesses due to thermal stresses or lead to corrosion at the joints. Recent advancements have seen the emergence of adhesive sealing, where high-strength industrial adhesives are used to bond metal surfaces. These adhesives provide a cleaner and often more efficient alternative to mechanical joining methods.
The expertise in metal-to-metal sealing is evident when factors like surface preparation are considered. Surface roughness can significantly influence seal effectiveness. A smoother surface enhances adhesive bonding, while certain textures may better accommodate gasket sealing. The cleaning of surfaces to remove contaminants like oils, dirt, and oxidization is a non-negotiable step, as these can impair adhesion or gasket performance.
sealing metal to metal
Another dimension of expertise is the environmental considerations of the sealing process. Metals exposed to harsh environments — such as those in offshore or chemical processing industries — necessitate seals that resist corrosive elements and extreme temperatures. The choice of sealing materials must therefore be guided by a comprehensive understanding of the service environment and long-term durability requirements.
Trustworthiness in metal-to-metal sealing is reinforced through quality assurance measures. Rigorous testing protocols should be implemented to simulate operational conditions and stressors. These tests can include pressure, temperature cycling, and fatigue testing to validate the reliability and lifespan of the seal. Manufacturers often certify their products to comply with international standards, providing an added layer of assurance to clients.
Documentation and traceability are also integral. Detailed records of material specifications, testing results, and process parameters should be maintained. This transparency not only builds trust with customers but also enables troubleshooting and continuous improvement in sealing processes.
Moreover, the authority of a manufacturer or service provider in this field is often demonstrated through innovation and adherence to best practices. Industry leaders invest in research and development to pioneer new sealing technologies and materials. They frequently contribute to industry standards and guidelines, shaping the future landscape of metal-to-metal sealing.
In conclusion, sealing metal to metal is a sophisticated task requiring a blend of technical knowledge, practical experience, and strict adherence to quality standards. As industries evolve, so do the demands on seals, pushing for more advanced and reliable solutions. Companies dedicated to mastering this art are not only ensuring their competitiveness but also profoundly impacting the safety and efficiency of countless applications worldwide.