Miniature press brakes have become pivotal in manufacturing, catering to industries eyeing precision, efficiency, and adaptiveness. Beyond their mechanical prowess, understanding their niche applications and the nuances of their operation highlights their indispensability.
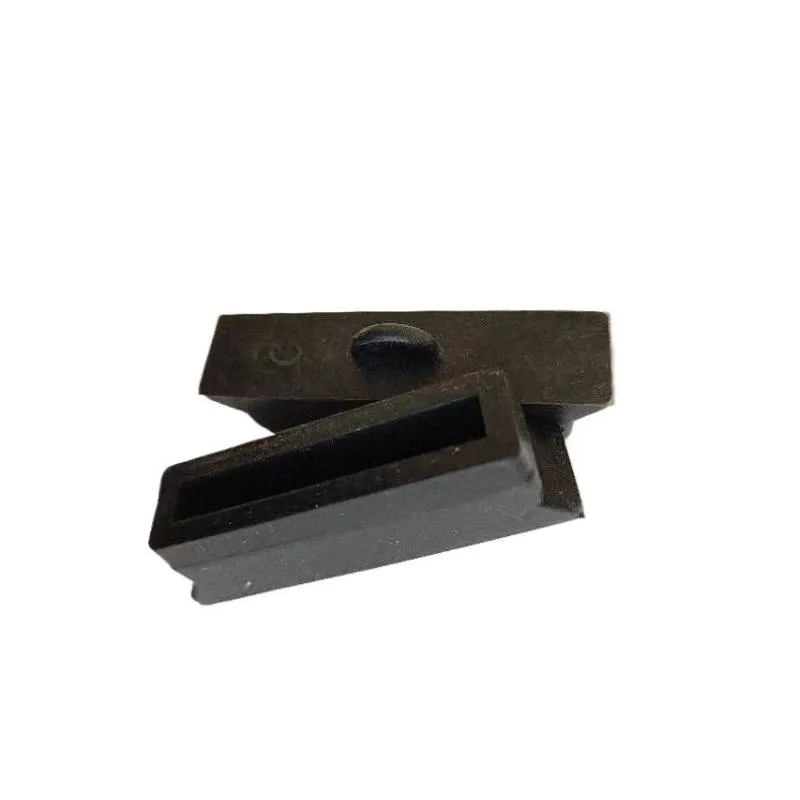
1.
Precision and Adaptability
Miniature press brakes, often referred to as micro press brakes, champion precision. They are designed to accommodate small, complex parts that demand meticulous attention to detail and precision bending, ideal for sectors like electronics, aerospace, and medical devices. Their adaptability lies in their capability to handle a broad range of materials — from delicate metals to modern composites — without compromising on the precision of the bend. These machines excel in environments where space optimization and nimbly meeting custom demands are essential.
2. Advanced Technological Integration
What sets modern miniature press brakes apart is their integration with state-of-the-art technologies. Many are equipped with CNC (Computer Numerical Control) systems, which allow for automated, consistent, and precise bending operations. These intelligent systems store and execute specific operations without human error, drastically reducing waste and enhancing throughput. Furthermore, some advanced models incorporate IoT capabilities, allowing for remote monitoring and predictive maintenance, thereby minimizing downtime and maximizing efficiency.

3. Expertise in Operation
Operating a miniature press brake demands a blend of technical expertise and an understanding of the intricate nature of small part production. Trained operators, familiar with the idiosyncrasies of the material they are working with, can fine-tune the machine settings to achieve precision that is within micrometers. The expertise lies in understanding not just the machine, but also the behavior of varied materials under pressure, the flexibility of the tool, and the potential for springback, which influences the final geometry of the product.
4. Versatile Applications
The industrial versatility of miniature press brakes extends to a plethora of applications. In the electronics industry, they are critical for manufacturing enclosures and components where precision is non-negotiable. In aerospace, where weight-to-strength ratios are crucial, these machines facilitate the crafting of complex control panels and structural components. Within the medical device sector, where sterilization and precision are paramount, miniature press brakes assist in creating components used in surgical instruments and implants.
miniature press brake
5. Authoritativeness through Engineering Excellence
Manufacturers of miniature press brakes command authority by consistently advancing the engineering landscape. Through investment in research and development, they push the boundaries of what these machines can achieve, often setting industry benchmarks for efficiency, precision, and safety. Companies that hold patents on innovative technologies become industry trailblazers, leading the pack and setting standards that others follow.
6. Trustworthiness via Quality Assurance
In an industry where trust is built on reliability and performance, miniature press brakes are subjected to rigorous quality assurance processes. This includes stress tests, durability tests, and precision tests that ensure each unit meets stringent industry criteria before it ever reaches the production floor. Trust is further solidified by comprehensive customer support and service agreements, ensuring that clients have access to technical assistance whenever required.
7. Sustainable Manufacturing Practices
In addition to precision and efficiency, the operation of miniature press brakes is increasingly aligning with sustainable manufacturing practices. By minimizing energy usage, reducing material waste through precision, and adopting environmentally-friendly operational protocols, these machines contribute to a more sustainable production environment.
8. Real-World Experiences and Use Cases
Consider the example of a leading electronics component manufacturer who transitioned to miniature press brakes, resulting in a 30% reduction in production time and a 20% decrease in material waste. This real-world application showcases not only the financial benefits but also the enhanced precision and quality of the final product, affirming the strategic advantage afforded by these machines.
By encompassing these strategic aspects, companies leveraging miniature press brakes can maintain a competitive edge. Integrating cutting-edge technology, ensuring a workforce skilled in precise operations, and adhering unabatedly to quality and sustainability not only enhance operational efficiency but also establish a benchmark of trust and authority in the marketplace.