Milling thin wall aluminum is a precision engineering task that requires not only advanced machinery but also experienced hands that comprehend the intricate details of the material and process involved. This particular operation is essential in various industries, such as aerospace, automotive, and electronics, where lightweight yet sturdy components are crucial. The complexity of milling thin walls in aluminum stems from the metal's propensity to deform under high machining forces and the challenge of maintaining tight tolerances.
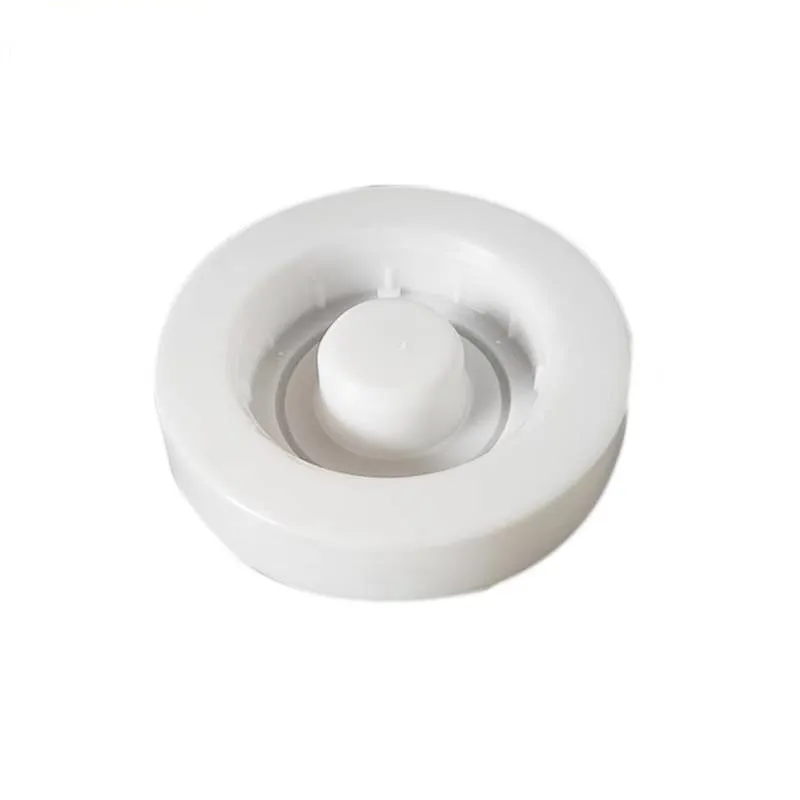
Understanding the behavior of aluminum during milling is pivotal. Aluminum is known for its ductility and high thermal conductivity, attributes which can be both advantageous and problematic. During milling, the heat generated is quickly dissipated, but at the cost of potential thermal expansion and material deformation. Therefore, operators must strike a balance between cutting speed, feed rate, and the sharpness of the milling tools. Using high-helix end mills, for example, can minimize the radial force, reducing the chance of wall deflection and chatter, which is a common issue in thin wall milling.
Moreover, machinists must account for tool deflection, a critical factor when dealing with thin wall structures. Tool deflection can lead to inaccuracies and poor surface finish, negatively impacting the performance of the final product. Employing tools with a smaller diameter can alleviate this, allowing for a finer cut and less deflection. Additionally, optimizing the tool path through advanced CAM software can enhance efficiency and accuracy. This software can simulate the milling process, identifying potential areas of concern and allowing adjustments before actual machining, effectively reducing trial and error time.
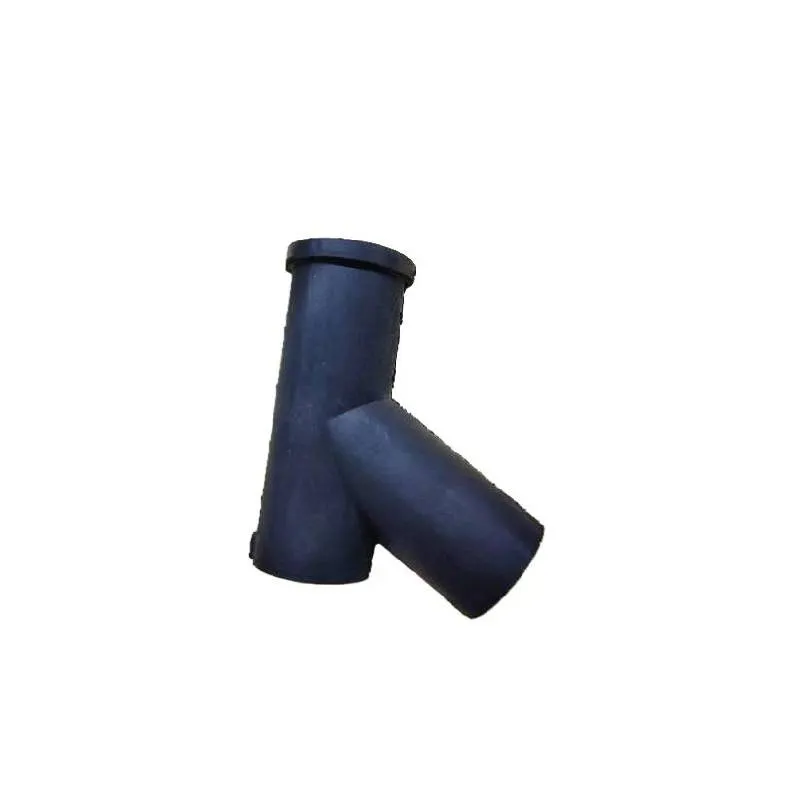
Experts in the field emphasize the importance of stable fixturing to prevent vibration and ensure precision during the milling of thin wall aluminum. Vacuum fixtures or custom jigs are often recommended to secure the workpiece without applying excessive pressure, which can warp the thin walls. It is essential to verify that the fixtures themselves are not introducing additional variables that could complicate the process.
Coolant application is another crucial aspect of the milling process to consider. It not only helps in heat dissipation but also serves to remove chips from the cutting area, preventing them from causing scratches on the machined surface. High-pressure coolant systems can be used to effectively wash away chips during high-speed milling. However, it is vital to ensure that the coolant is compatible with the aluminum alloy used to avoid chemical reactions that could compromise the integrity of the material.
milling thin wall aluminum
The choice of aluminum alloy also plays a significant role in the milling process. Alloys such as 6061 and 7075 are popular choices due to their excellent machinability and mechanical properties, making them suitable for components that will face varied mechanical stresses. Understanding the specific attributes of these alloys can inform decisions on tool selection and milling parameters, allowing for optimized operations.
In terms of quality assurance, non-contact measurement tools like laser scanners or vision systems provide a way to verify the dimensions and surface quality of thin wall components without risking damage that contact methods might introduce. This enhances the reliability of the final product, ensuring it meets the stringent standards required, particularly in industries where precision is non-negotiable.
Ensuring the quality of the milling process necessitates a thorough understanding of machine dynamics and continuous monitoring. Implementing real-time monitoring systems can help identify any deviations in the milling process, providing immediate feedback, and allowing for corrections on the fly. This capability is particularly advantageous in high-volume production runs where consistent quality is crucial.
Finally, continuous education and adaptation to the latest technology are vital for maintaining expertise in the field of thin wall milling in aluminum. Whether it's through attending industry conferences, subscribing to relevant publications, or participating in professional networks, staying informed about the latest advancements ensures the use of best practices and cutting-edge solutions.
In summary, the milling of thin wall aluminum demands a multifaceted approach that combines expert knowledge of material properties, precise machining strategies, and advanced technological tools. Mastery of these elements results in the production of high-quality components that meet the exacting standards of modern engineering industries.