Metal washers with teeth, often referred to as toothed or serrated washers, play a crucial role in ensuring secure and stable fastening in various mechanical and industrial applications. With a uniquely designed structure that incorporates small projections or teeth, these washers provide enhanced grip and resistance to rotation. Here, we delve into their functionalities, applications, and the nuances of optimizing their use for maximum efficiency and reliability, presenting insights drawn from extensive industry experience and expertise.
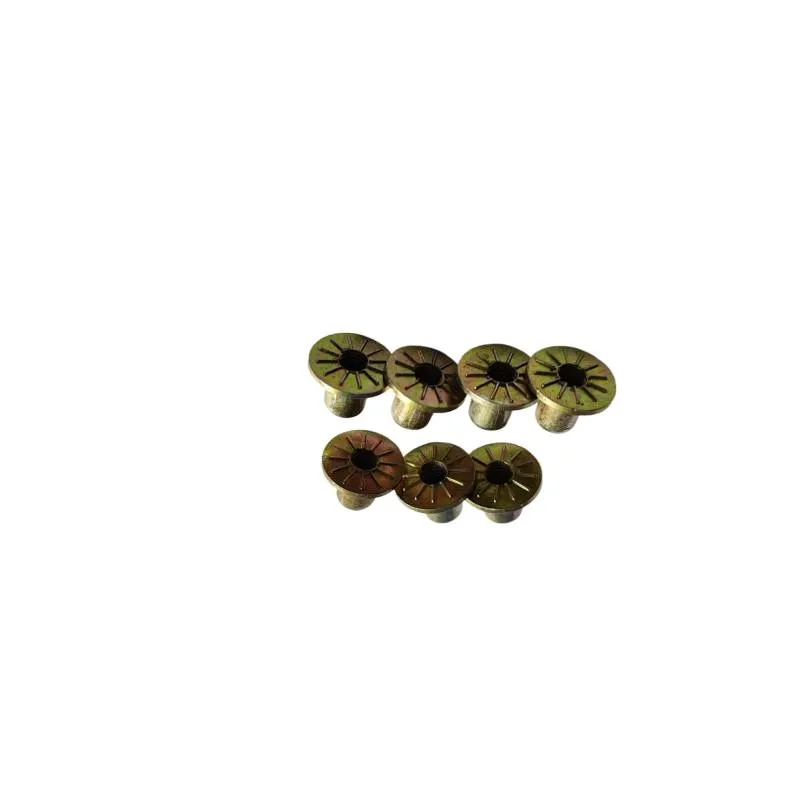
The primary function of a metal washer with teeth is to prevent the loosening of a fastening assembly. This function is particularly critical in high-vibration environments where traditional flat washers might fail. The teeth of these washers dig into the surface material, creating a locking mechanism that secures components against rotation and movement, thereby maintaining the integrity of the assembly. This characteristic makes toothed washers indispensable in industries such as automotive manufacturing, aerospace engineering, and heavy machinery, where the precision and durability of connections are paramount.
In selecting the right toothed metal washer, several factors should be considered to optimize performance. Material selection is a primary concern. Stainless steel offers excellent corrosion resistance and strength, making it ideal for most applications. However, in environments with extreme temperatures or chemical exposure, alternative alloys such as titanium or specialized coated steels may provide enhanced performance. Understanding the environmental conditions and mechanical stresses that the washer will encounter allows for informed material choices, thereby improving both longevity and reliability.
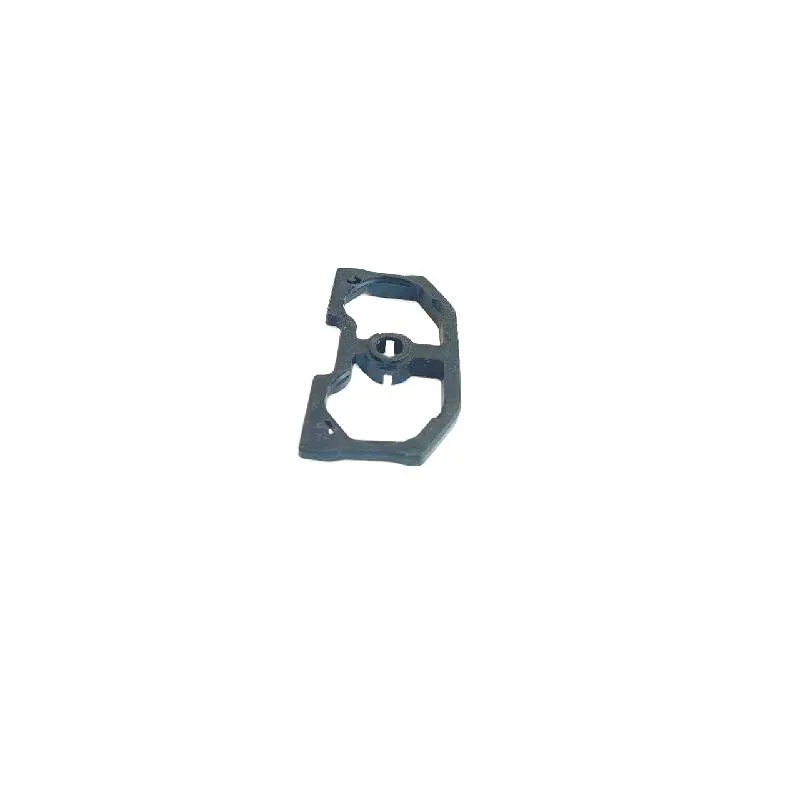
The size and configuration of the teeth are also critical. Different profiles, whether external or internal, cater to varied applications. External-tooth washers, for instance, deliver exceptional grip on softer surfaces, while internal-tooth washers provide superior hold within confined spaces. Additionally, the thickness and diameter of the washer must match the specifications of the bolt or screw used, ensuring an even distribution of load and minimizing potential damage to the surfaces in contact. Precision in these attributes assists in achieving uniform contact pressure, enhancing the strength of the mechanical joint.
metal washer with teeth
When installing a toothed washer, attention to detail safeguards against potential malfunctions.
It's essential to align the teeth properly with the intended surfaces to maximize their locking potential. Applying consistent torque during fastening ensures that the teeth engage fully without damaging the materials involved. In scenarios where maintenance is frequent, understanding the residual effects on the washer's effectiveness is essential, as repeated use may lead to wear or deformation of the teeth, compromising their locking ability.
Real-world applications often present complex challenges requiring customized solutions. In the automotive industry, for example, toothed washers contribute significantly to the stability of engine components, exhaust systems, and suspension assemblies. Specialists in this field employ advanced simulation and testing techniques to optimize washer configurations, ensuring that vehicles withstand extensive operational stresses and environmental conditions. These methodologies underscore the washer's role in enhancing safety and performance, showcasing the expertise required to deploy these components effectively.
Recent advancements in manufacturing technology have led to the development of washers with enhanced performance characteristics. Innovations such as laser-cutting and precision stamping have improved the dimensional accuracy and consistency of toothed washers, enhancing their effectiveness and reducing installation errors. Coating advancements also provide additional benefits, such as increased wear resistance and improved frictional properties, broadening the application scope of these washers in evolving industrial contexts.
In conclusion, metal washers with teeth offer unparalleled securing capabilities across diverse applications where vibration and movement could otherwise compromise connection integrity. Their value derives from a combination of material excellence, design precision, and application expertise. Professionals in the field recognize that optimal performance is not solely dependent on the component itself, but on its integration within a broader mechanical system. Emphasizing the E-E-A-T principles in both their manufacture and use upholds the reliability and safety standards industry stakeholders demand, ensuring these small yet mighty components consistently meet and exceed expectations.