Metal turned parts constitute a critical component of numerous modern industries, revolutionizing the precision and customization capabilities available today. As an integral part of the manufacturing landscape, these components merit significant attention due to their extensive applicability and specialized production techniques.
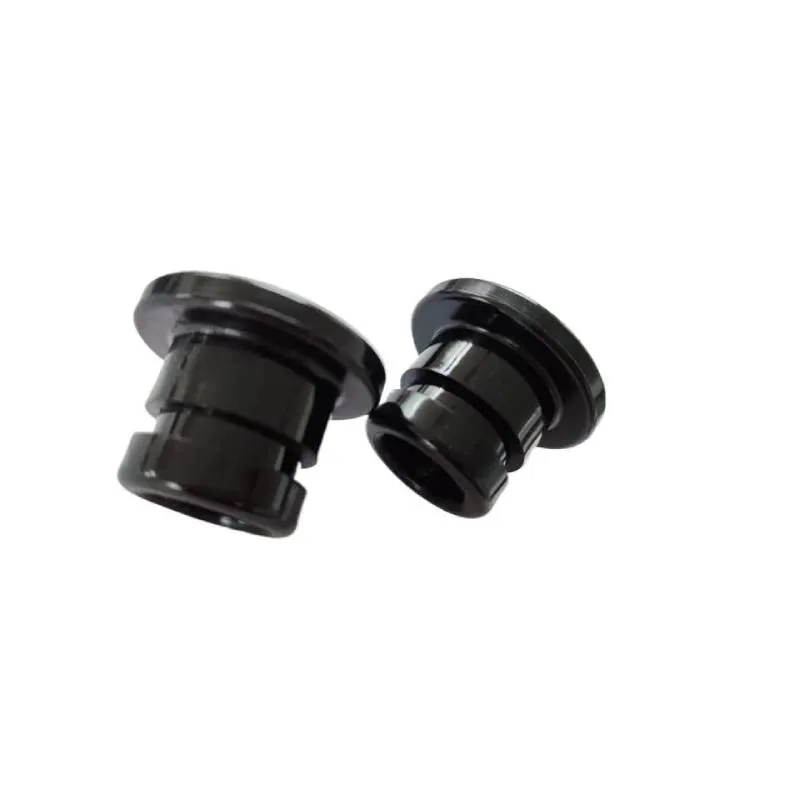
In the world of manufacturing, precision is king. Metal turned parts are produced using a process known as turning, a fundamental method within the machine shop that forms part of the wider machining family. This technique predominantly employs a lathe, allowing manufacturers to create parts with intricate forms and exacting specifications. It is the deft manipulation of raw metal materials using high-speed rotational forces that imbues turned parts with their extraordinary detail and precision.
Expertise in the production of metal turned parts is paramount. Experienced machinists use Computer Numerical Control (CNC) machines to drive unprecedented accuracy in crafting these parts, ensuring each one meets the stringent demands of today's clients. With CNC machining, operators translate complex designs into tangible products through highly detailed programming. This precision technology can produce complex geometries that are difficult to achieve with other machining processes, ultimately offering end-users tailor-made solutions that optimize function and performance in their respective applications.
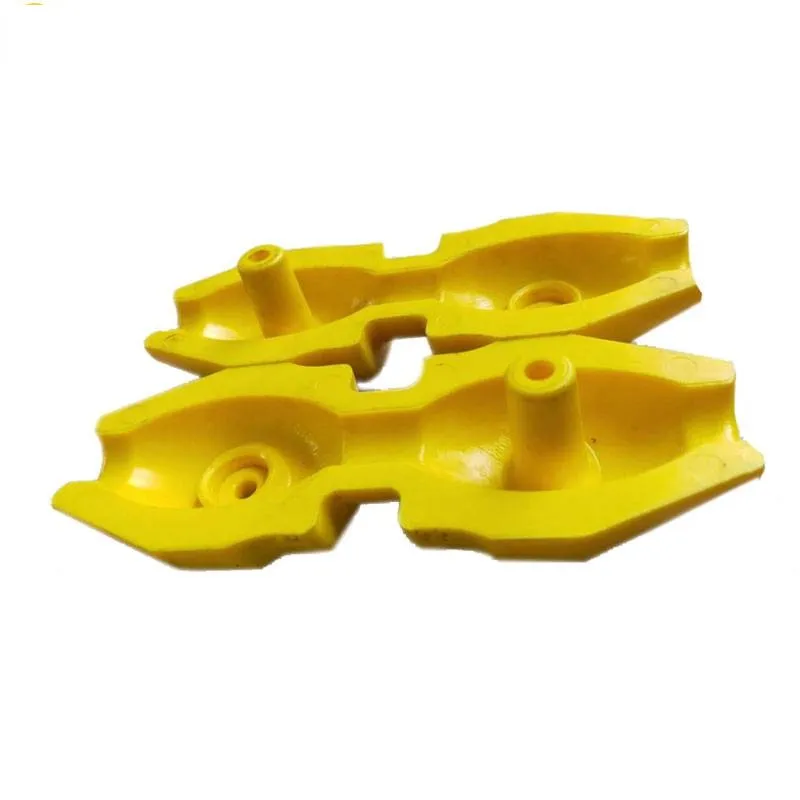
Authoritativeness within this realm comes from a manufacturer's ability to consistently deliver high-quality parts that meet industry standards. Companies striving for the highest levels of authority often seek certifications like ISO 9001, which calls for strict quality management systems. Such accreditations not only enhance a company's credibility but also assure clients of the consistent quality they can expect from the products they procure.
The trustworthiness of metal turned parts is built on reliability and performance. These components must endure rigorous operational conditions, often under high stress or extreme temperatures, depending on their application. Metal turned parts are pivotal in sectors ranging from aerospace to automotive, where the margin for error is nonexistent. Each piece must exhibit both high tensile strength and resistance to wear and tear, ensuring durability and longevity. This reliability translates not only to enhanced safety but also to reduced downtime and maintenance costs over the part's lifespan.
metal turned parts
Furthermore, metal turned parts are celebrated for their versatility. They are used in an extensive array of products and applications, from simple mechanical assemblies to complex aerospace components. This widespread applicability highlights their importance across various technological advancements, further underscoring their indispensable status within the industry.
For companies seeking bespoke solutions, the customization potential inherent in metal turned parts is invaluable. Different metals and alloys, each offering unique characteristics, can be selected based on the specific demands of the application. From stainless steel and brass to titanium and aluminum, the choice of material influences attributes such as corrosion resistance, weight, and strength, allowing for parts to be fine-tuned to precise requirements.
Emphasizing both quality and dependability, metal turned parts are a testament to the prowess of modern manufacturing techniques and the adaptation of raw materials into sophisticated, operationally critical components. As industries evolve, the importance of these components will only escalate, continuously pushing the boundaries of what can be achieved through careful material selection, advanced machining processes, and meticulous quality control.
In summary, metal turned parts are not only about crafting components but also providing solutions that are integral to the enhancement of product efficiency and performance. With significant expertise and authoritative processes, the creation of these parts ensures trusted, high-quality outcomes that meet the demanding requirements of modern industries.