High temperature metal seals play a critical role in industries where the utmost reliability and performance are non-negotiable, such as aerospace, automotive, oil and gas, and power generation. These seals must withstand extreme temperatures while maintaining their integrity, thus preventing leaks that could otherwise lead to catastrophic failures. With decades of continuous research and development, the technology behind these essential components has evolved exponentially, guaranteeing both performance and safety.
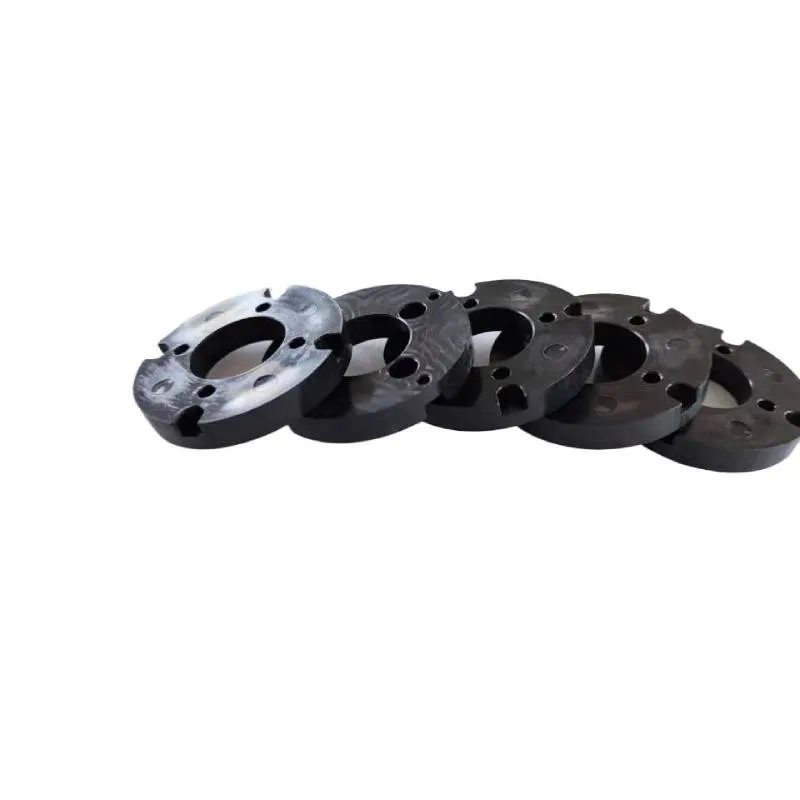
The protective function of high temperature metal seals is unparalleled. Constructed from formidable alloys such as Inconel, stainless steel, and Hastelloy, their resilience against intense heat and corrosive environments makes them the ideal choice for demanding applications.
The design typically employs a combination of metal-to-metal sealing and additional coatings or inserts to enhance performance. This unique construction ensures the seal remains operational under temperatures exceeding 1000 degrees Fahrenheit.
An important factor to consider when choosing high temperature metal seals is their compatibility with different operational environments. Given that these seals often operate in a variety of harsh conditions, they must be tailored to the specific application. This customization involves the careful selection of materials and engineering processes to meet unique operational demands, such as exposure to aggressive chemicals, high pressure, and thermal cycling.
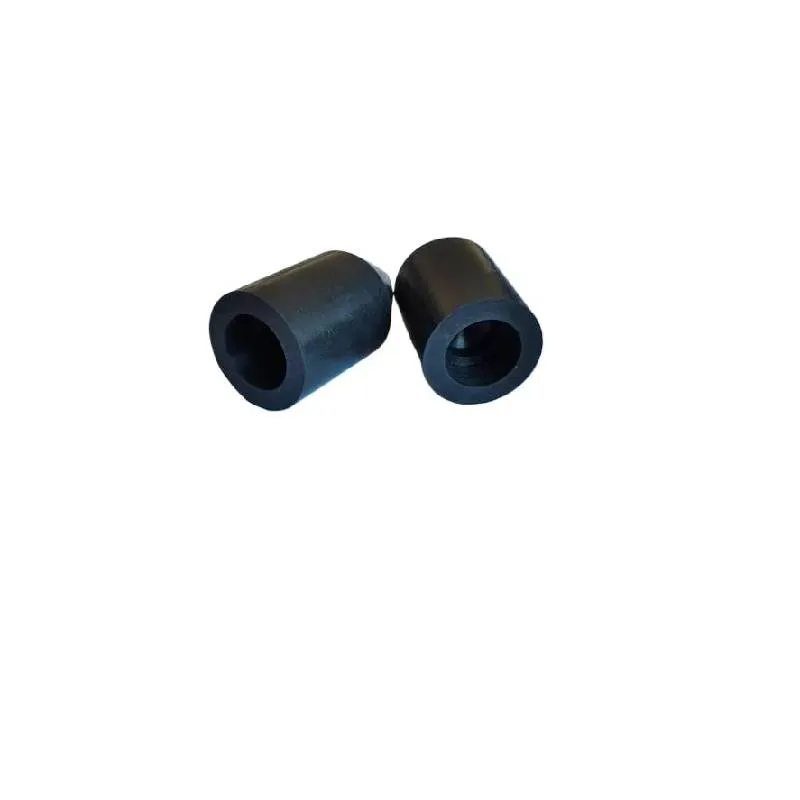
Expert recommendations suggest that regular maintenance and inspection of these seals are key to extending their lifespan. Experience in industries like aerospace has shown that even the most robust seals require periodic checks to identify signs of wear and tear, such as deformation or surface degradation. Advanced diagnostic tools, including non-destructive testing techniques like ultrasonic testing and eddy current inspections, are implemented to ensure the seals are in optimal working condition without disrupting operations.
high temperature metal seals
Trust in high temperature metal seals is affirmed through stringent testing and certification processes. Manufacturers subject these seals to rigorous qualification tests that simulate extreme operational conditions. Certifying bodies, such as the American Society of Mechanical Engineers (ASME) or the International Organization for Standardization (ISO), endorse products that meet predefined standards, providing a guarantee of quality and reliability.
Nevertheless, the industry continues to innovate, seeking ways to further enhance the functionality of high temperature metal seals. Researchers are exploring novel materials and composite solutions that offer improved thermal resistance and adaptability. One promising direction is the development of hybrid seals that integrate advanced ceramic materials, known for their exceptional temperature tolerance and minimal thermal expansion.
Purchasers of high temperature metal seals are advised to work closely with manufacturers to ensure that the selected seals are designed and tested precisely for their application needs. A collaborative approach allows for the seamless integration of these components into existing systems, minimizing downtime and ensuring operational efficiency.
In conclusion, the strategic importance of high temperature metal seals cannot be overstated. Their ability to maintain performance in extreme conditions not only safeguards critical systems but also extends the operational life of costly equipment. As industries continue to push the boundaries of what is possible, the evolution of seal technology remains a testament to human ingenuity and a cornerstone of industrial safety.