For industries that operate under extreme conditions, the integrity and performance of sealing solutions are critical. High temperature metal o-rings have become indispensable components in such scenarios, thanks to their unique ability to maintain their shape and efficacy under severe temperatures and pressures. This comprehensive guide seeks to provide an in-depth understanding of high temperature metal o-rings, shedding light on their applications, material composition, benefits, and selection criteria.
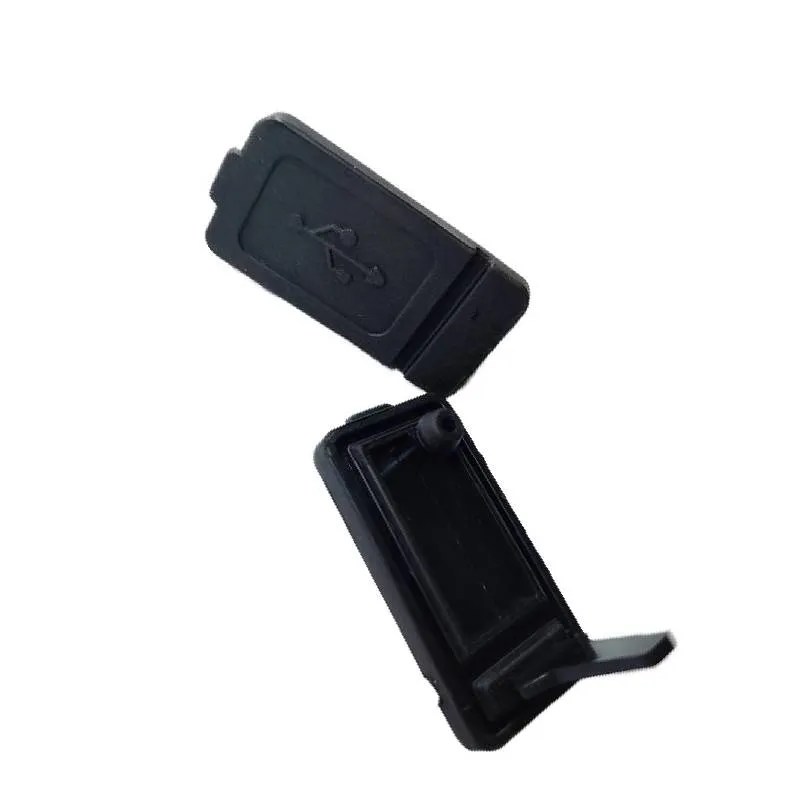
High temperature metal o-rings are engineered to provide reliable sealing in environments where conventional rubber or elastomeric rings would fall short. These metal o-rings are typically crafted from robust alloys such as Inconel, stainless steel, or Hastelloy. Each alloy offers specific advantages; for instance, Inconel is renowned for its exceptional corrosion resistance and ability to withstand severe thermal cycling, making it a popular choice in the aerospace and defense industries.
One of the defining attributes of metal o-rings is their capacity to endure temperature extremes — often surpassing 1000°F (540°C) — without compromising their sealing properties. This remarkable characteristic is invaluable in sectors like oil and gas, chemical processing, and power generation, where the safety and efficiency of operations hinge upon the reliability of every component. In these settings, metal o-rings not only provide a hermetic seal but also contribute to the system's overall structural integrity.
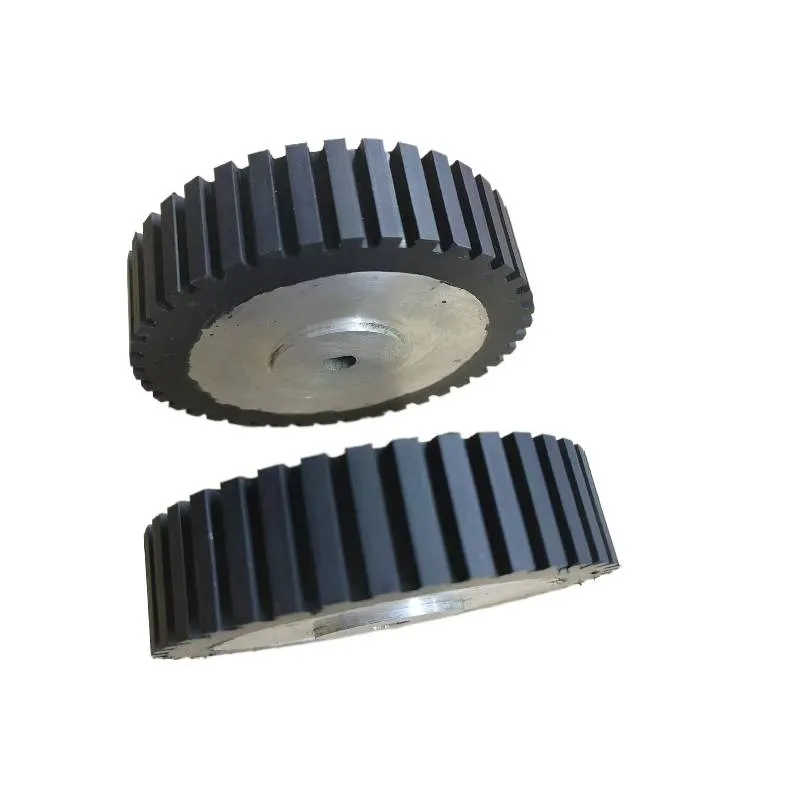
Experience from industries that regularly use high temperature metal o-rings underscores their durability and effectiveness. For instance, in the aerospace sector, where aircraft engines and structural components are regularly exposed to high temperatures and pressures, metal o-rings have proven essential for maintaining operational safety. Engineers in these fields often highlight the rings' superior resistance to thermal expansion and contraction, which minimizes the risk of leakage or failure under fluctuating conditions.
high temperature metal o rings
From a professional perspective, choosing the right metal o-ring requires a keen understanding of the application's specific conditions. Factors such as the nature of the fluids to be sealed, operating pressures, temperature ranges, and potential exposure to corrosive substances must all be carefully considered. Moreover, customization of the o-ring's cross-sectional profile could be required to meet exceptional operational demands or to fit unique industrial designs.
Authoritative sources on high temperature sealing solutions emphasize the necessity of rigorous testing and quality assurance in the manufacturing of metal o-rings. Certified production processes that adhere to international standards such as AS9100 for aerospace or ISO 9001 for general industrial applications provide assurance of the product's reliability and performance. Testing for tensile strength, elasticity under extreme conditions, and corrosion resistance are crucial steps in ensuring the o-rings' durability and efficacy in high-stakes environments.
Trust in high temperature metal o-rings also stems from their proven track record across various high-demand sectors. Companies that have invested in high-quality metal o-rings often report decreased maintenance needs and enhanced longevity of their machinery. This reduction in downtime not only cuts costs but also significantly boosts operational efficiency. Testimonials from seasoned industry professionals often reiterate the o-rings' ability to withstand harsh process conditions while maintaining reliable performance.
In conclusion, high temperature metal o-rings are foundational components in applications demanding extraordinary resilience and precision. Their development is rooted in a deep understanding of material science and engineering principles, underscoring the expertise required to produce these crucial elements. By selecting appropriately tailored metal o-rings and ensuring compliance with rigorous manufacturing standards, industries can achieve optimal performance and safety in even the most challenging environments. As such, these o-rings are not just simple components but are pivotal to the success and reliability of modern high-temperature operations.