Deburring metal parts is a critical aspect of manufacturing that often determines the final quality, functionality, and safety of the product. In industries ranging from aerospace to consumer electronics, the presence of burrs can lead to serious quality control issues, affecting the performance and lifespan of metallic products.
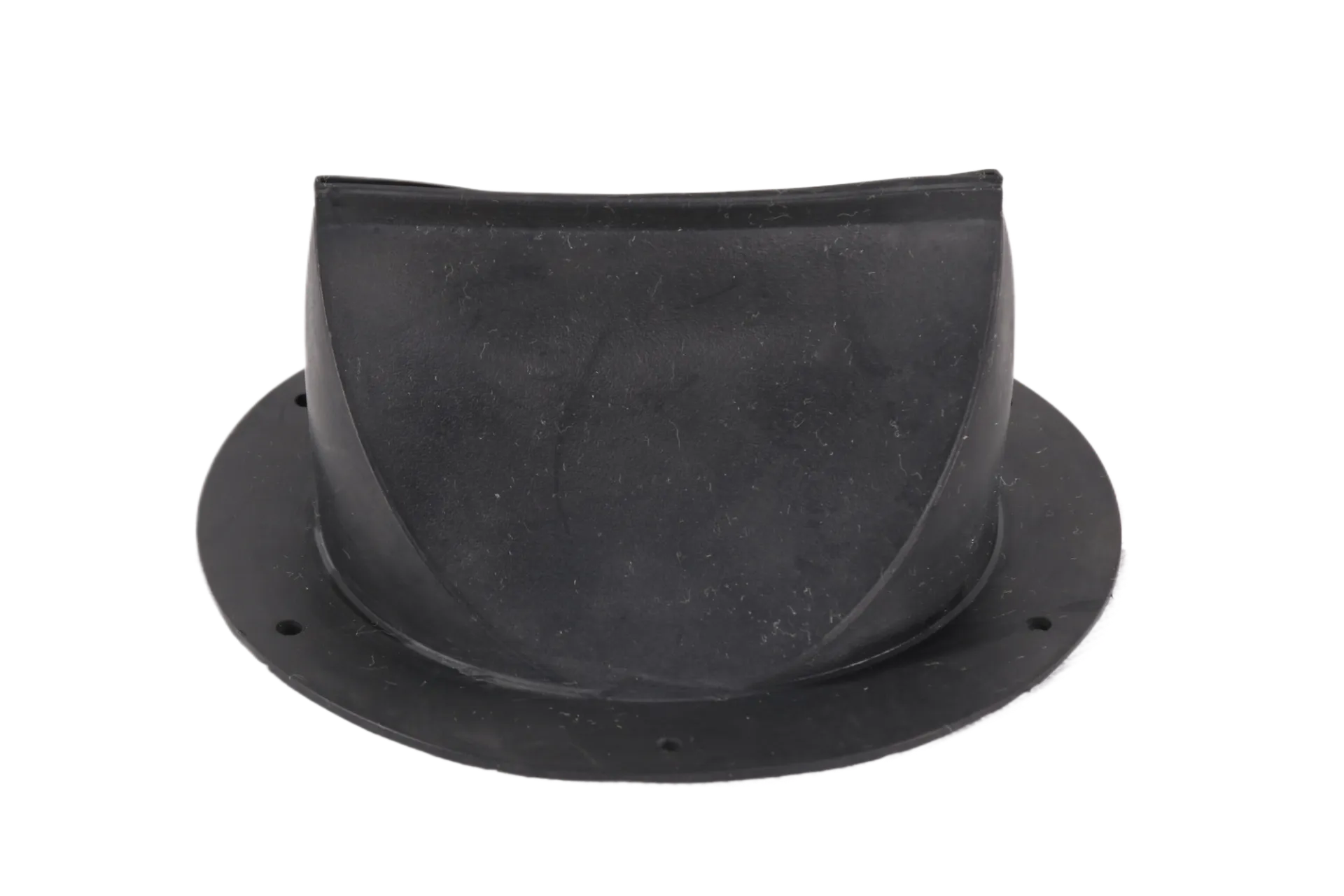
The process of deburring involves the removal of small imperfections or rough edges, known as burrs, which typically form during machining or cutting operations. Burrs can compromise component fit, exacerbate wear and friction, and in the worst-case scenario, cause mechanical failure.
This makes deburring not just an optional step, but a mandatory process for achieving precision craftsmanship.
There are various techniques available for deburring metal parts, each with its distinct advantages, challenges, and best-use scenarios. Manual deburring is one of the oldest techniques, offering detailed attention and finesse by skilled technicians. Utilizing tools such as files, abrasive stones, or scrapers, manual deburring is ideal for small-scale operations or components requiring high precision. However, given its intensive labor demands, it's less suited for large production runs.
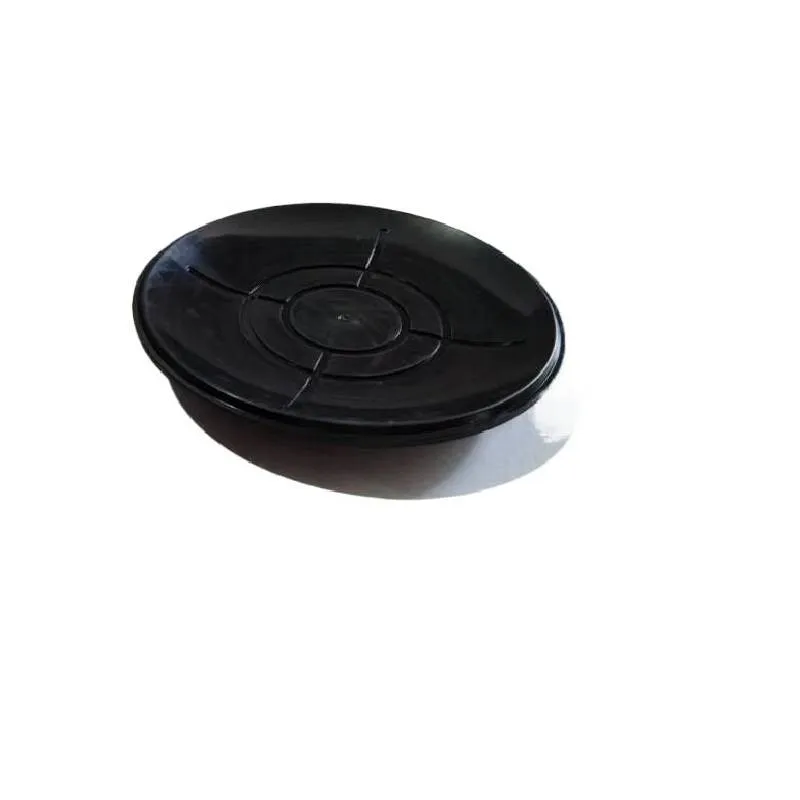
Mechanical deburring, on the other hand, employs machinery that automates the deburring process using tumblers or vibratory finishers. This method provides uniform results quickly and efficiently, making it suitable for bulk production. Yet, care must be taken to optimize cycle times and media types, as over-processing can damage parts or remove more material than desired.
Electrochemical deburring is another innovative process that involves removing burrs using electrolysis. It is highly precise, especially for hard-to-reach areas or complex geometries. The process minimizes material removal elsewhere on the part, maintaining the integrity of the component’s precise dimensions. Nevertheless, it requires stringent control over the electrical parameters and an understanding of material behavior under such conditions.
deburring metal parts
Moreover, thermal energy deburring—using controlled explosions to vaporize burrs—is especially effective for intricate and inaccessible areas. Its high initial setup cost is justified in scenarios involving complex part geometries or materials that are difficult to machine.
Choosing the right deburring process often depends on several factors material properties, part geometry, production volume, and the specific requirements of the finished product. For manufacturers dealing with high-precision industries like aerospace or medical devices, precise and reliable deburring is integral to meet industry standards.
Implementing effective deburring processes also feeds into the broader quality assurance framework, impacting not only the aesthetic and functional aspects of components but also their market reputation and compliance with safety regulations. Investing in the right equipment, technologies, and skilled workforce for deburring operations can significantly enhance a company's competitive edge.
Beyond the process itself, the sustainability and environmental considerations of deburring should not be overlooked. Manufacturers are increasingly looking into cleaner technologies and recyclable media to minimize environmental impact, aligning their operations with ever-stringent environmental regulations.
In summary, the deburring of metal parts is a nuanced field of manufacturing where precision, efficiency, and foresight play a pivotal role. Whether through manual finesse or high-tech automation, mastering deburring techniques is key to ensuring the quality and reliability of metallic components. As industry knowledge and technology progress, manufacturers must adapt and innovate their deburring strategies to meet expanding demands and regulations, truly underscoring the importance of expertise and trustworthiness in the field.