Custom metal seals represent a crucial component in a variety of industrial applications where leakage control and durability are paramount. Their adeptness at providing robust sealing solutions across sectors like aerospace, automotive, oil and gas, and heavy machinery has made them indispensable. Drawing from extensive industry experience, it is clear that the efficiency of custom metal seals hinges on their material composition, design precision, and application-specific customization.
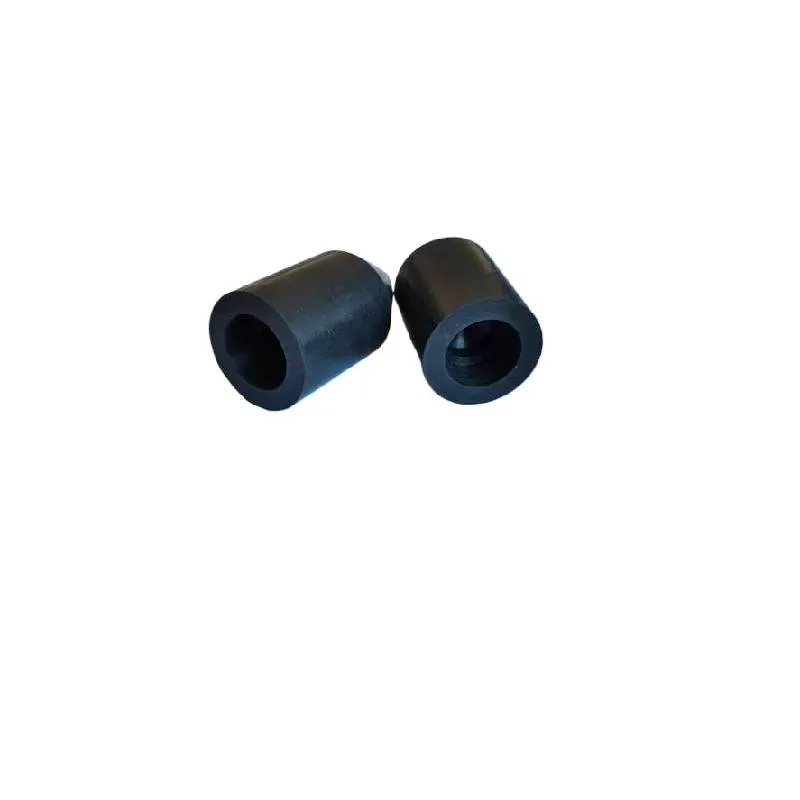
From years of hands-on involvement in the field, the choice of material for custom metal seals is foundational. Metals like stainless steel, Inconel, and copper-nickel alloys are commonly chosen for their superior resistance to high temperatures, pressures, and corrosive environments. For instance, stainless steel seals are highly favored in the food and beverage industry for their corrosion resistance and ability to maintain integrity under steady thermal exposure. Meanwhile, Inconel is preferable in aerospace applications where extreme temperatures and oxidative environments are a concern.
Expertise in seal design further elevates the efficacy of custom metal seals. The most successful custom solutions are those that seamlessly integrate into existing systems, ensuring not only perfect fit and function but also heightened performance efficiency. Precision in custom metal seal design involves finite element analysis (FEA) and computational fluid dynamics (CFD) to predict seal behavior under operational stresses. This analytical approach allows engineers to optimize seal geometry and material characteristics, reducing the risk of failure and extending the lifecycle of the seal. For instance, in the automotive sector, where seal integrity is vital for engine components, employing FEA can predict deformation under thermal cycling, thus tailoring the production process for enhanced durability.
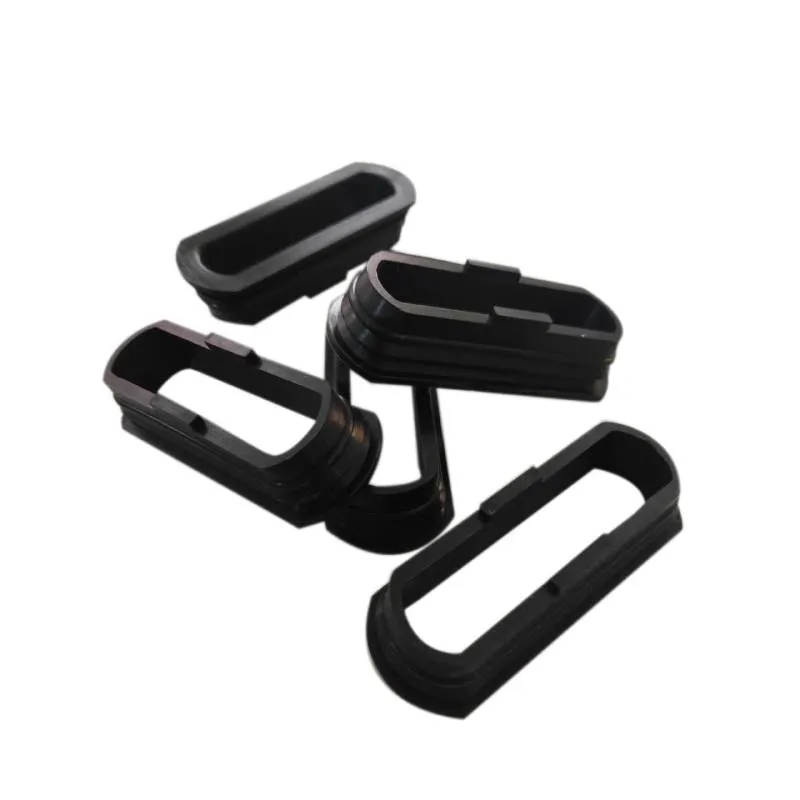
custom metal seals
In the sphere of customization, the ability to tailor seals to precise operational requirements is perhaps the most authoritative aspect that sets custom metal seals apart from their generic counterparts. Companies demand seals that can address specific challenges such as extreme temperature fluctuations, aggressive chemical exposures, or unique spatial constraints. This level of customization often involves novel engineering solutions like bi-directional sealing or the use of composite metal-rubber combinations that afford both rigidity and flexibility. Trustworthiness in the custom seal industry is bolstered by rigorous testing protocols that simulate real-world conditions, ensuring that each seal performs as expected before deployment.
Further reinforcing the reliability and credibility of custom metal seals is the adherence to stringent quality standards such as ISO 9001 and industry-specific certifications like AS9100 for aerospace applications. Compliance with these standards underscores a manufacturer's commitment to quality assurance and continuous improvement, assuring clients of the precision and dependability of their products. A transparent supply chain that traces the origin of materials and the adherence to environmentally responsible manufacturing practices also enhances trust and credibility.
In conclusion, the multidimensional strengths of custom metal seals lie in their meticulously selected materials, innovative design techniques, and tailored customization methods—all underpinned by unwavering adherence to quality standards. Whether addressing the needs of high-stakes aerospace applications or the exacting demands of industrial processing, the expertise and reliability of custom metal seals ensure they remain a cornerstone of modern engineering solutions. Their ability to deliver unparalleled performance while adhering to rigorous quality controls positions them as a trusted choice for engineers and industry leaders across the globe.