Galvanized washers, though seemingly small components, play a pivotal role in numerous industries, underpinning the structural integrity and longevity of countless projects. Their galvanization process sets them apart from regular washers, offering serious advantages in terms of durability and protection, especially in harsh environments.
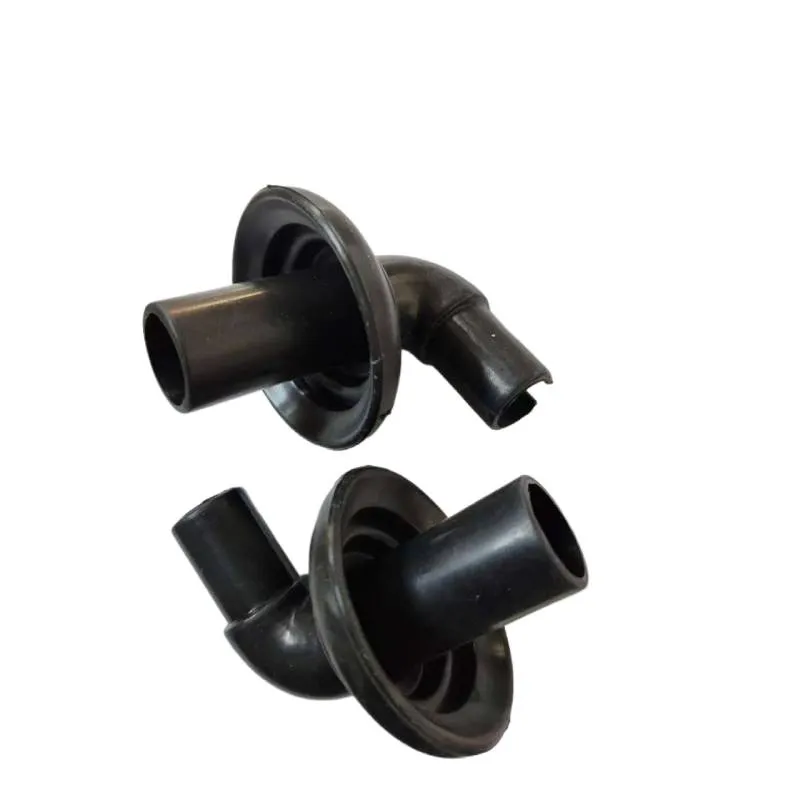
Experience in using galvanized washers reveals their crucial benefits in real-world applications. For instance, during a recent construction project involving a coastal building, these washers ensured that the structure remained corrosion-free despite the salty, humid air. The added layer of zinc provided by galvanization serves as a powerful deterrent against rust, thereby extending the life of the structures that incorporate these washers. From bridges to pipelines and even everyday appliances, the reliability of galvanized washers cannot be overstated, especially in settings where exposure to the elements is unavoidable.
Diving into expertise, it's essential to understand the galvanization process to appreciate its significance fully. Galvanization involves coating the washer, often made of steel, with a thin layer of zinc. This zinc coating acts as a sacrificial anode, meaning it will corrode first, thus protecting the steel underneath. This makes galvanized washers an ideal choice in environments prone to moisture and chemicals, where other washers might fail. Their resilience is unmatched, particularly when considering cost-to-benefit ratios in large-scale operations, such as industrial machinery or construction projects.
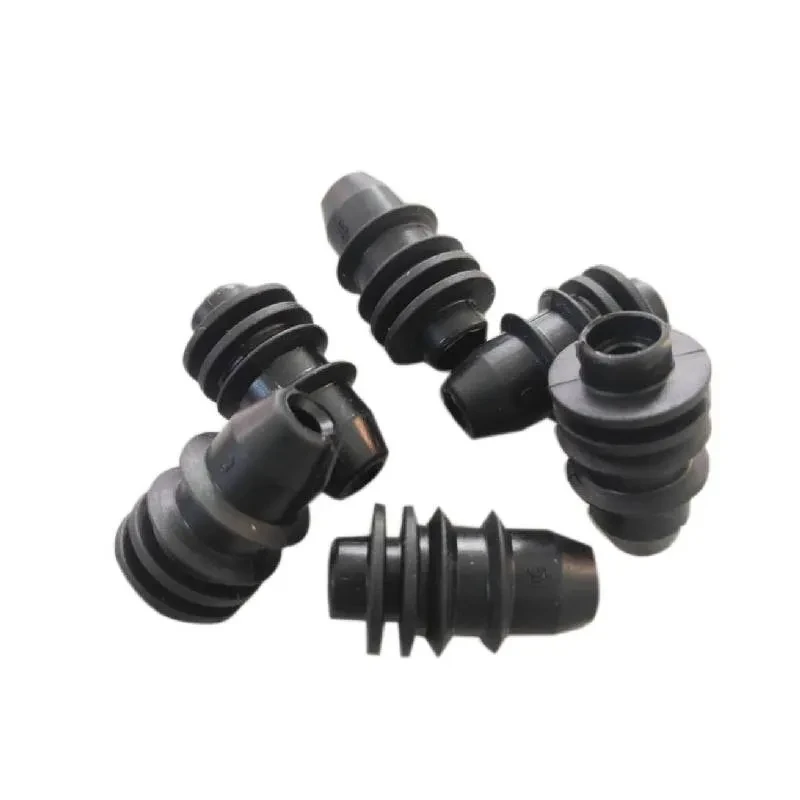
washer galvanized
In terms of authoritativeness,
industry standards further affirm the selection of galvanized washers. Both ASTM and ISO have stringent guidelines on the use and manufacture of these components. Companies adhering to these standards demonstrate their commitment to quality and safety. Galvanized washers are manufactured according to precise specifications that ensure they can withstand immense pressure and adverse conditions without losing effectiveness. This standardization underlines their reliability and positions them as essential components in projects requiring high levels of safety and durability compliance.
Trustworthiness in using galvanized washers is bolstered by testimonies from engineers and industry professionals who constantly advocate for their use. The confidence in galvanized washers stems from their proven track record in the field. Engineers often cite significant maintenance cost reductions when galvanized components are used, as they are less likely to require replacement due to corrosion-related failures. This dependability is essential in critical applications such as transportation infrastructure and military equipment, where failure can result in dire consequences.
In conclusion, the extensive benefits provided by galvanized washers, from their extensive protective features and compliance with international quality standards to their proven trustworthiness in the field, make them an essential component in industries where durability and reliability are non-negotiable. Their capacity to safeguard steel components against corrosion, coupled with their cost-effectiveness and robust performance, ensures they remain a staple in engineering solutions worldwide. Whether it's bridging the gap between two structural elements or ensuring machinery functions without the risk of component degradation, galvanized washers stand out as a superior choice, embodying a perfect blend of engineering precision and material science.