Navigating the complex landscape of the oil and gas industry requires detailed knowledge of various components essential to pipeline integrity and reliability. Among these components, pipe fittings play a crucial role. These fittings are not mere accessories but integral parts that ensure seamless transportation of oil and gas, safeguard against leaks, and maintain system efficiency under high-pressure conditions. Understanding the different types of pipe fittings used in this sector enhances operational efficiency and safety, two critical pillars in the industry.
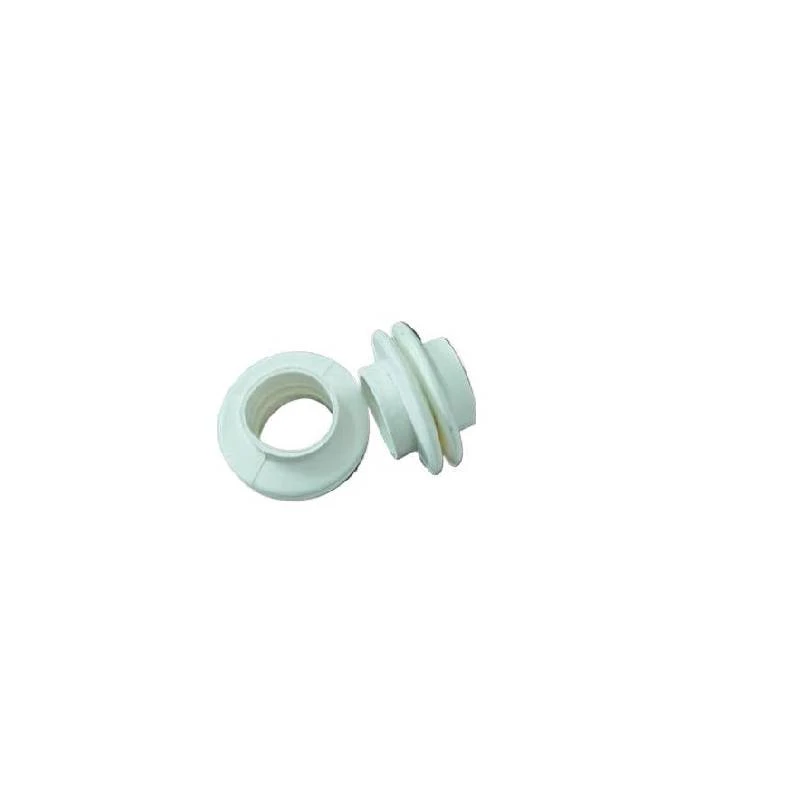
Pipe fittings in the oil and gas industry are meticulously designed to handle extreme conditions. The industry relies on a diverse range of fittings, each serving specific purposes and suited for unique applications. These fittings not only unify the pipeline system but also facilitate directional changes, branch connections, and size adjustments, ensuring the smooth operation of both upstream and downstream processes.
One of the most commonly used fittings is the elbow. Elbows are critical in altering the pipeline's direction, typically by 45 or 90 degrees. They allow for smooth transitions in direction without compromising the flow integrity, which is vital for maintaining consistent pressure levels throughout the system. Selecting the right elbow, manufactured from high-grade materials, is imperative for minimizing wear and tear and extending the pipeline's lifespan.
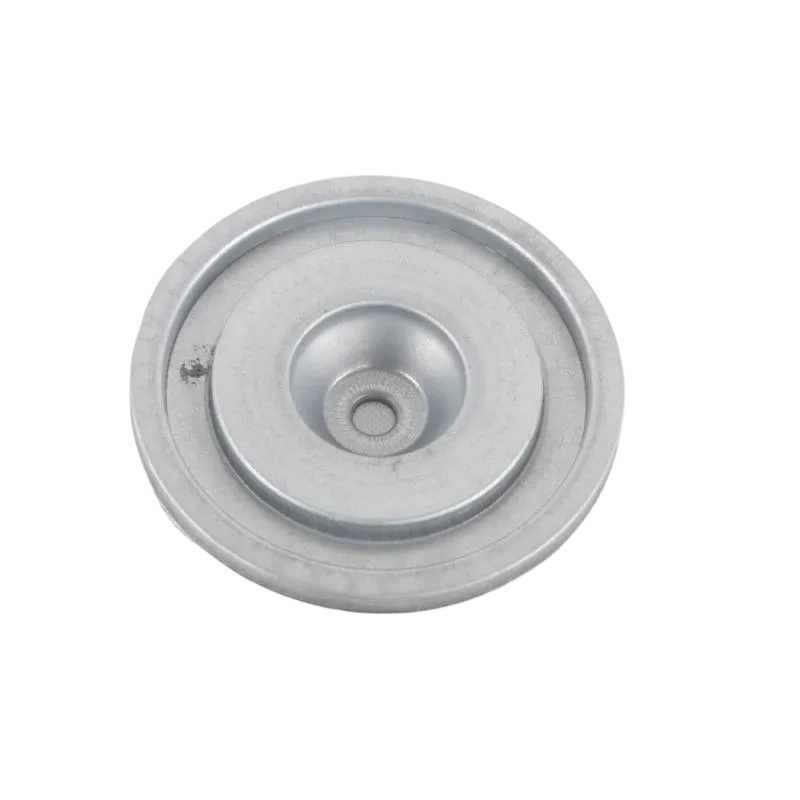
Tees, another essential type, come into play when creating branch lines. Particularly in massive distribution networks, tees enable the bifurcation of flow without causing pressure drops that might compromise system efficiency. Properly designed tees, constructed from corrosion-resistant materials, allow operators to maintain a balance between multiple branches, ensuring the steady delivery of oil and gas.
Couplings are fundamental for connecting straight sections of the pipeline or terminating pipe runs. They offer flexibility in pipeline design, allowing sections to be joined with precision. Especially in the maintenance and repair of pipelines, couplings present a convenient solution for replacing damaged segments without extensive system overhauls. High-pressure couplings in particular are indispensable in ensuring that connections hold firm under extensive pressure and temperature variations.
types of pipe fittings in oil and gas industry
Reducers play a vital role in modifying the pipe diameter, enabling seamless transitions between pipes of differing diameters. This fitting is essential when adapting systems to meet changing demands or integrating upgraded technology. In oil and gas operations, reducers help manage flow rates and accommodate equipment specifications, ensuring that the pipeline system operates at optimal efficiency.
The choice of material is another critical consideration in selecting fittings. Typically, materials like carbon steel, stainless steel, and alloy steel are preferred for their durability and resistance to extreme environmental factors. Each material has properties that make it suitable for specific applications, ranging from high-corrosion environments to high-pressure settings. The longevity and performance of pipe fittings hinge on selecting the appropriate material tailored to the operating conditions.
Safety valves represent another pivotal category of pipe fittings. They are designed to automatically relieve pressure from the system when it exceeds predetermined limits. An industry where pressure fluctuations can lead to catastrophic failures highlights the importance of safety valves in protecting both infrastructure and personnel. Regular inspection and maintenance of these valves are paramount to ensure they function correctly.
In summary, the types and materials of pipe fittings in the oil and gas industry significantly influence the effectiveness and safety of pipeline operations. An understanding and appreciation of these components yield insights that contribute to more informed decision-making, improved operational performance, and enhanced safety protocols. Appreciating the nuances of each type of pipe fitting helps design more resilient and efficient pipeline systems, crucial in an industry that demands precision and reliability.