The world of steel tank end caps, while often overlooked, is a critical component in various industries ranging from oil and gas to water treatment facilities. Understanding the intricacies of these seemingly simple structures can significantly enhance the efficiency and safety of storage systems. This article delves into the vital aspects of steel tank end caps, emphasizing comprehensive experience, expert insights, authoritative guidance, and utmost trustworthiness in their design and application.
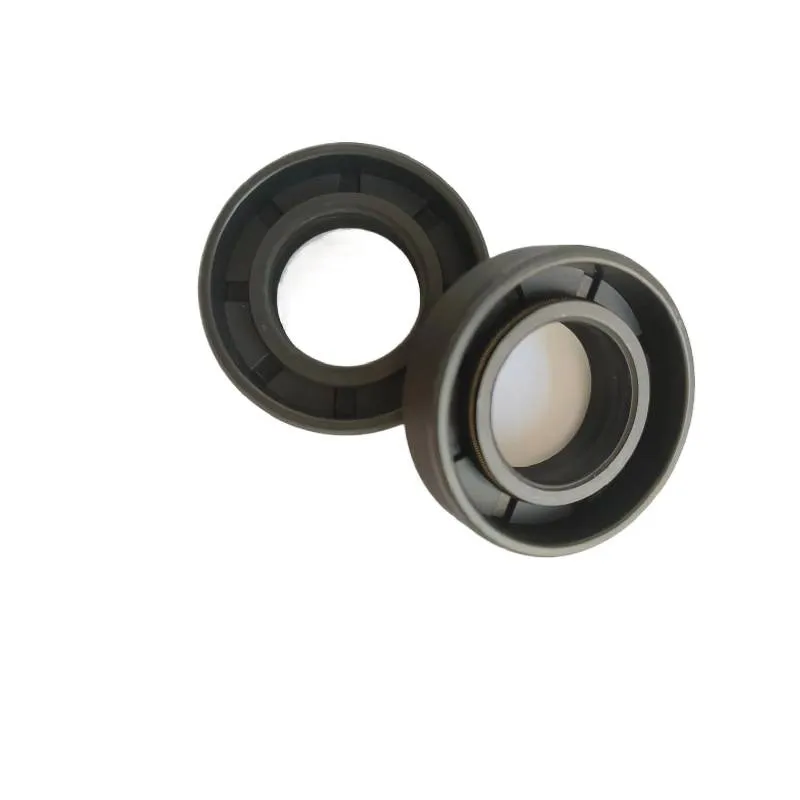
The first glance at a steel tank end cap reveals a simple design, yet beneath this simplicity lies an advanced engineering feat. These components are crafted to protect the contents within the tank, ensuring both containment and safety standards are rigorously met. When selecting an appropriate end cap, factors such as material, shape, and engineering specifications must be meticulously considered.
Steel, known for its durability and high tensile strength, is the material of choice for end caps, especially in environments susceptible to pressure variations and extreme weather conditions. The inherent resilience of steel ensures that the caps withstand external forces while preventing leakages, maintaining integrity over prolonged periods. Engineers consistently prefer this metal due to its reliable performance and capacity to conform to stringent industry regulations.
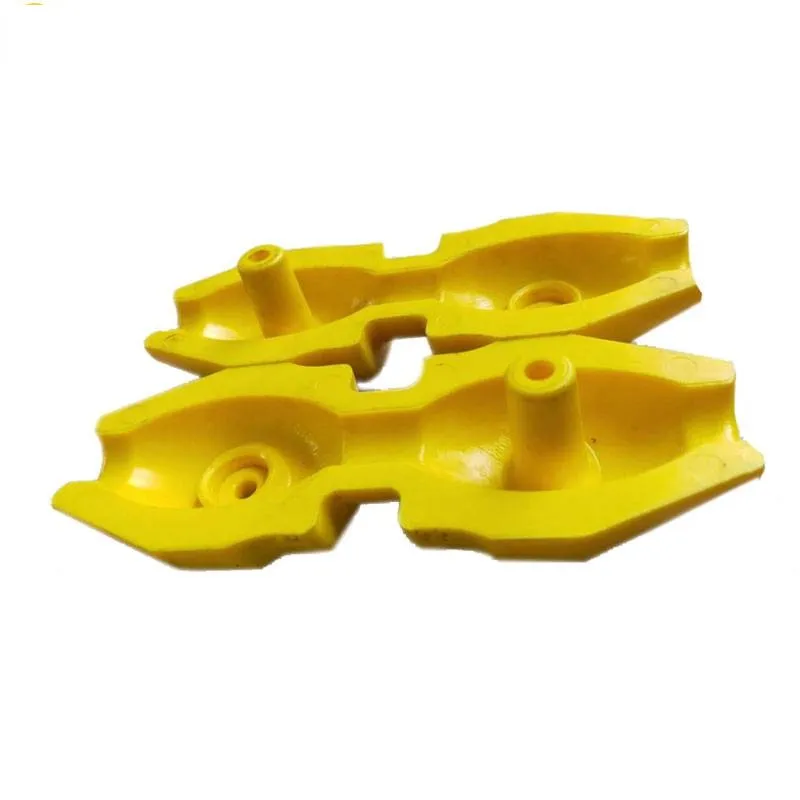
The shape of the steel tank end cap is another crucial element, typically available in forms like elliptical, flat, and hemispherical. Each shape serves distinct purposes; for instance, hemispherical end caps are employed in high-pressure contexts due to their ability to distribute stress equally, minimizing the risk of structural failures. On the other hand, elliptical caps are a popular choice for medium-pressure applications, balancing cost-effectiveness with functional adequacy. The choice of shape is predicated on the specific requirements of the storage system and the desired pressure tolerance levels.
Real-world efficiency is largely determined by the precision in manufacturing these steel tank end caps. The implementation of state-of-the-art fabrication techniques further enhances their performance. Advanced welding methods, such as submerged arc welding, not only improve the aesthetic finish but also ensure a seamless, permanent joint that fortifies the overall structure. Precision machining of the edges is pivotal in preventing corrosion, which might otherwise compromise the safety and longevity of the tanks.
steel tank end caps
Expertise in steel tank engineering brings an understanding that transcends standard manufacturing practices. Engaging with knowledgeable professionals who possess a substantial track record is invaluable. They provide insights into optimizing the balance between cost and performance, while also customizing solutions tailored to specific industrial applications.
The role of authoritative guidance cannot be understated. Regulatory bodies across the globe stipulate standards such as the American Society of Mechanical Engineers (ASME) codes, which dictate the construction and testing of pressure vessels, including end caps. Adherence to these codes is mandatory, not only to comply with legal requirements but also to ensure environmental and operational safety. Firms that consistently align with these standards demonstrate their commitment to producing end caps that withstand rigorous testing and meet globally accepted safety protocols.
Trustworthiness in the context of steel tank end caps is reflected in both the supplier’s reputation and the empirical data supporting product performance. Reviews and testimonials from industry peers serve as vital indicators of reliability and quality. Moreover, empirical performance data, derived from extensive testing under simulated real-world conditions, provides quantitative assurance about the product’s capability to endure operational stresses.
Summarily, when choosing steel tank end caps, consider a synthesis of expert advice and empirical evidence that aligns with proven engineering standards. The ideal solution will not only fulfill functional requirements but also bolster safety and reliability, underscoring a trustworthy commitment to quality. With the rapid evolution of industrial standards and technological advancements, maintaining a steadfast focus on these four pillars—experience, expertise, authoritativeness, and trustworthiness—remains quintessential for optimal performance and safety in storage solutions.