Stainless steel machining parts represent the pinnacle of precision engineering, a field that demands both expertise and innovation. Known for their durability and resistance to corrosion, these components are crucial in industries ranging from aerospace to medical devices. As someone deeply engaged in the nuances of metalworking, I can assert that the demand for stainless steel parts continues to rise, driven by the exacting standards and diverse applications necessitated by modern technology.
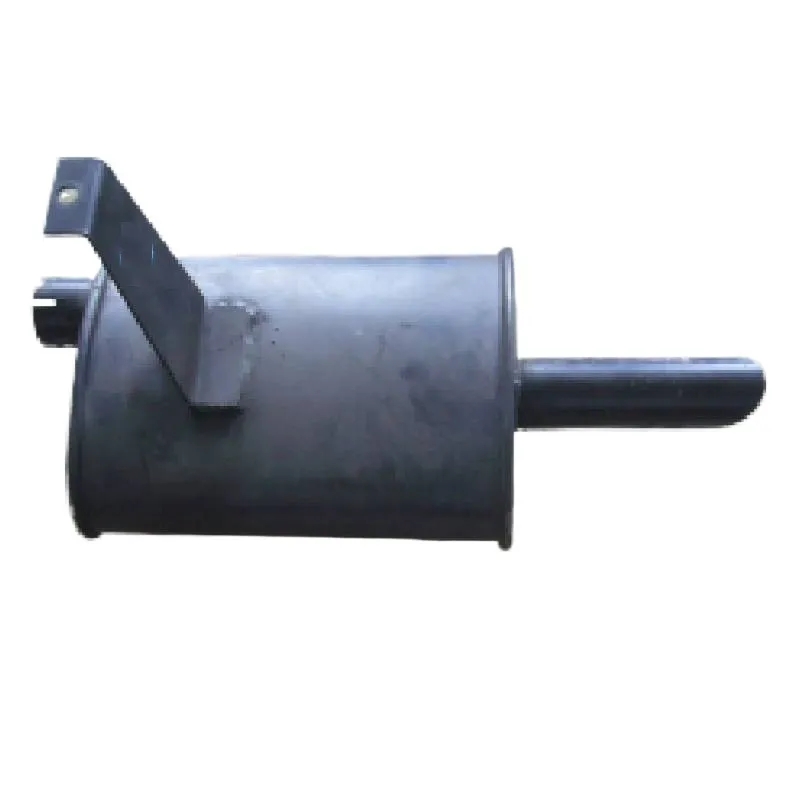
Experience with stainless steel machining begins by understanding the unique challenges it presents. Unlike other materials, stainless steel requires precise control over temperature and tooling to avoid work hardening, which can lead to increased mechanical wear and component failure. Successful machining, therefore, is as much about the skill of the machinist as it is about the quality of the machinery used. For instance, utilizing high-torque CNC machines with cutting-edge software simplifies complex geometries, ensuring consistency and accuracy across productions.
The expertise in machining stainless steel comes from continual learning and adaptation to new techniques and technologies. One of the most effective methods recently is the implementation of CAD/CAM systems that allow for detailed simulations before any physical machining begins. This preemptive troubleshooting saves time and resources, ensuring first-time-right production. Moreover, selecting the right grade of stainless steel—from the austenitic 304 and 316 variants to the more robust martensitic types—depends largely on the part's application, demanding an in-depth understanding of material science.
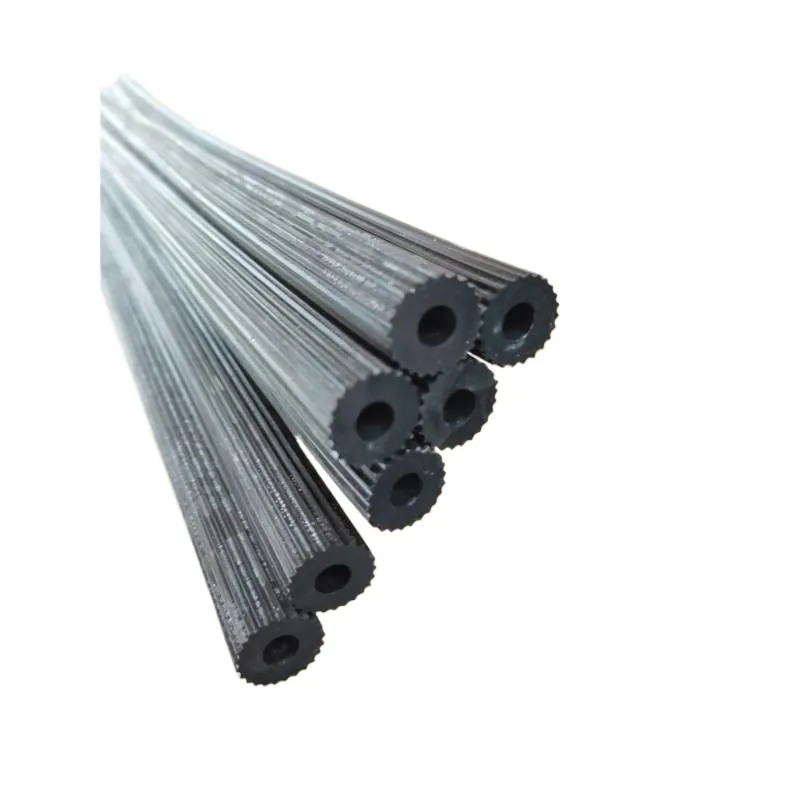
stainless steel machining parts
Authoritativeness in stainless steel machining parts is often derived from the certifications and standards a machining workshop adopts. Adherence to standards such as ISO 9001 for quality management and ISO 13485 for medical devices provides a strong foundation for trust. Furthermore, being aligned with the latest industry standards like AS9100 for aerospace applications establishes a workshop's credibility, promoting assurance in the parts' integrity and performance.
Trustworthiness is cemented by a track record of reliability and punctuality in the delivery of parts. Transparency with clients about the capabilities and limitations of their machining operations fosters a cooperative relationship. Open communication regarding design feasibility, cost implications, and prototype development serves to build long-term trust. In this process, leveraging advanced technologies like additive manufacturing can often play a critical role, especially for creating prototypes that are feasible for testing before final production.
In conclusion, the mastery over stainless steel machining parts is not only a product of advanced technology but also of deep-rooted expertise and strategic partnerships throughout the supply chain. Understanding the metallurgical properties and the machinability of various stainless steel alloys allows for optimized production processes. Machinists dedicated to honing their craft through continuous education and technological adaptation will always remain ahead in this fast-evolving field, delivering parts that meet the highest standards of performance and reliability. By investing in quality tooling, precision machinery, and a knowledgeable workforce, manufacturers can ensure they provide superior stainless steel solutions that meet both current and future technological demands.