Exploring the complex world of sheet metal brake parts unveils a fascinating blend of experience, expertise, authoritativeness, and trustworthiness that underscores their critical role in modern manufacturing. Sheet metal brake parts are quintessential components used for bending, cutting, and shaping sheet metal—elements fundamental to the frameworks of countless industries, from automotive to aerospace and beyond.
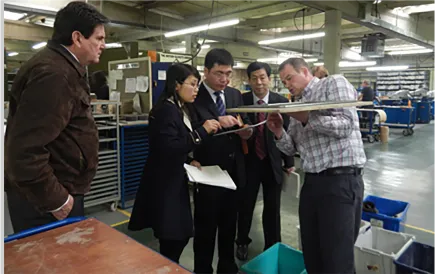
Manufacturers rely on top-notch sheet metal brake parts to ensure precision and efficiency in their production processes. These parts, including clamps, fingers, punch bars, and dies, form the backbone of the bending operation. Their performance directly influences the accuracy and quality of the final product. For instance, a brake's clamping system must securely hold the metal piece in place without causing surface damage. The finesse achieved through such high-quality components guarantees the seamless production of various architectural and mechanical elements.
Expertise in material selection is pivotal for the optimization of sheet metal brake parts. Different applications demand specific material types, often ranging from aluminum and brass to more robust materials like stainless steel and titanium. Professionals in the field are adept at selecting materials that offer the perfect balance of malleability and strength, thereby maximizing the part's lifecycle while minimizing wear and tear.
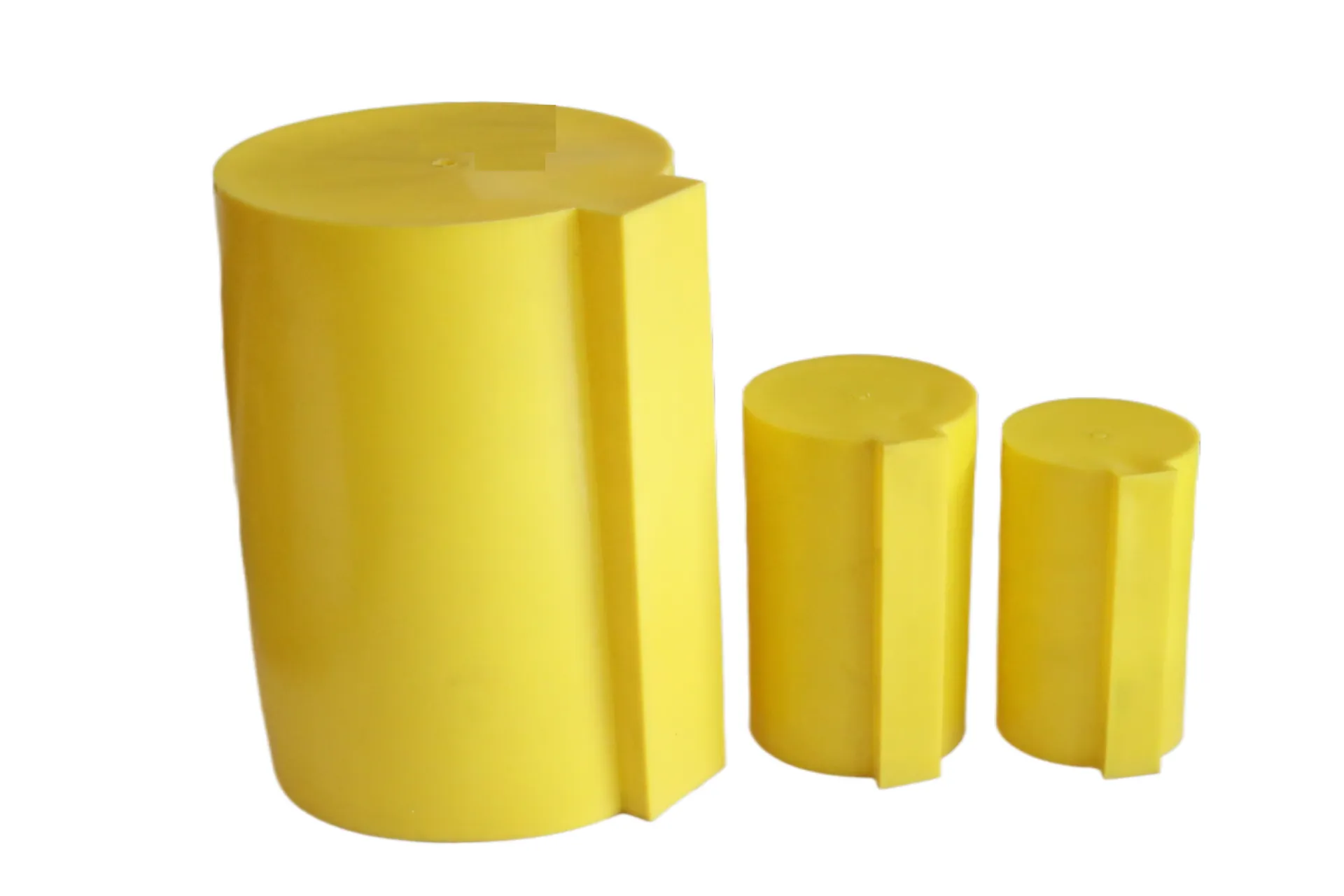
Diving deeper into the realm of innovation, advanced technology in sheet metal brake parts is setting new standards for efficiency and precision.
Computer Numerical Control (CNC) technology has revolutionized how brake parts operate, offering unparalleled precision and versatility. CNC controls allow for complex, programmable bending operations that reduce human error and ensure repeatability. Furthermore, the integration of real-time data monitoring facilitates the quick adjustment of processes, minimizing downtime and enhancing productivity.
sheet metal brake parts
The authority of sheet metal brake parts manufacturers is not just defined by their product quality but also by their commitment to safety and reliability. Adhering to rigorous industry standards, such as ISO certifications, reinforces the credibility and dependability of their products. Manufacturers invest in cutting-edge testing facilities and employ experts to rigorously test every component, ensuring it can withstand the demands of varied operational environments.
Trustworthiness is strengthened by a manufacturer's dedication to customer support and ongoing education. Professionals in the industry offer comprehensive training programs to ensure that users can maximize the capabilities of their sheet metal bending equipment. Additionally, after-sales services and technical support assure clients of persistent reliability and performance—a testament to the manufacturer’s confidence in their product.
Sustainability is increasingly significant in the manufacturing of sheet metal brake parts. Companies are now focusing on environmentally friendly production methods, opting for recyclable materials and implementing energy-efficient manufacturing processes. This approach not only reduces waste but also appeals to environmentally-conscious clients seeking sustainable solutions.
In summary, sheet metal brake parts are integral to the quality and efficiency of metal fabrication processes. With their design rooted in precise engineering, expert material selection, technological innovation, and rigorous industry standards, these parts embody the essence of reliability and competence. Continued advancement and commitment to sustainability in manufacturing promise an exciting future for sheet metal brake parts, poised to meet the ever-evolving demands of global industries.