Sand casting is a time-honored method of producing metal parts, embraced by industries that prioritize quality and precision. This age-old technique involves creating metal shapes by pouring molten metal into sand molds that capture every desired detail. The process stands out not merely for its historical significance but also for its adaptability, making it indispensable in crafting complex parts for a wide array of industries, including automotive, aerospace, and manufacturing.
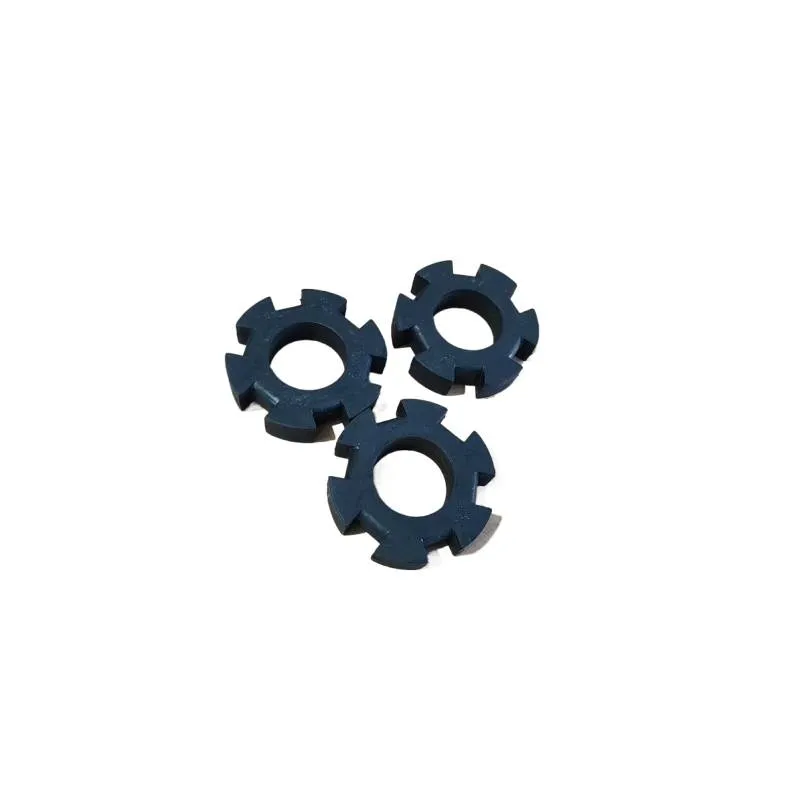
The expertise required in sand casting lies in the meticulous creation of the mold. Initially, a pattern of the part is formed, usually from wood, metal, or plastic, around which the sand is packed. This pattern accounts for everything, including shrinkage of the metal as it cools and solidifies. Professionals in the field know that selecting the right type of sand is crucial. Commonly used are silica-based sands, and the choice depends on the metal to be cast and the precision required. The expertise to choose the correct sand type contributes significantly to the finished product's detail and strength.
Once the mold is prepared, the molten metal is carefully poured into the hollow cavity formed by the pattern. It is during this phase that the role of an experienced technician becomes evident. The pouring temperature, speed, and method can dramatically affect the outcome. Excessive speed may cause defects such as turbulence or air entrapment, while insufficient heat might lead to an incomplete filling of the mold. Such nuances in sand casting require a significant degree of expertise and highlight why seasoned foundry workers are so valuable.
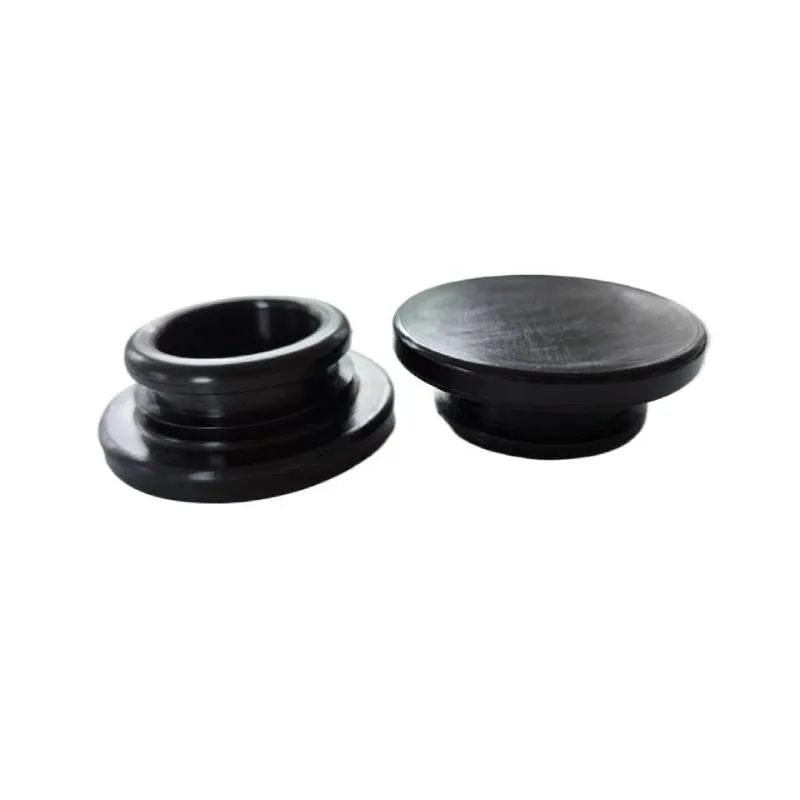
The authoritativeness of sand casting is evident in its widespread adoption and the trust that major industries place in this method. This trust is rooted in the material properties achieved through sand casting, which often surpass alternative manufacturing processes. For instance, the grain structure of sand-cast metals can exhibit enhanced strength properties, offering reliability in high-stress scenarios. This inherent quality assurance makes sand casting the preferred choice for critical components like engine blocks and wind turbine hubs.
sand casting parts
Moreover,
sand casting's versatility enhances its trustworthiness. The technique handles a myriad of metals, including iron, aluminum, brass, and bronze, making it adaptable to various applications without compromising quality. This adaptability, combined with cost-effectiveness—given the reusability of the sand and minimal waste—positions sand casting as a sustainable choice. It aligns with increasing global demands for environmentally conscious manufacturing, further strengthening the trust in its use.
Real-world experience also plays a pivotal role in ensuring the sand casting process evolves with technological advancements. Casting simulation software, quality control tools, and enhanced mold-making techniques have all contributed to refining the process. Industry veterans often draw from decades of insight, using both traditional know-how and modern techniques to guarantee the production of superior parts. This blend of experience and technology underscores why sand casting remains relevant despite being one of the oldest metal fabrication methods.
In summary, the intricate craft of sand casting is sustained by experience, expertise, authority, and trust. Whether it's the production of intricate aerospace components or robust industrial machinery parts, this technique endures as a revered practice. The melding of time-tested methods with cutting-edge innovations continues to amplify sand casting's value and ensures its place in the future of manufacturing.