Rubber hose ends are pivotal components in various industrial and domestic applications, contributing to the proper functioning and longevity of hose systems. These seemingly small parts play a significant role in ensuring smooth operation without leaks or pressure drops, factors critical for industries ranging from automotive to agriculture and beyond.
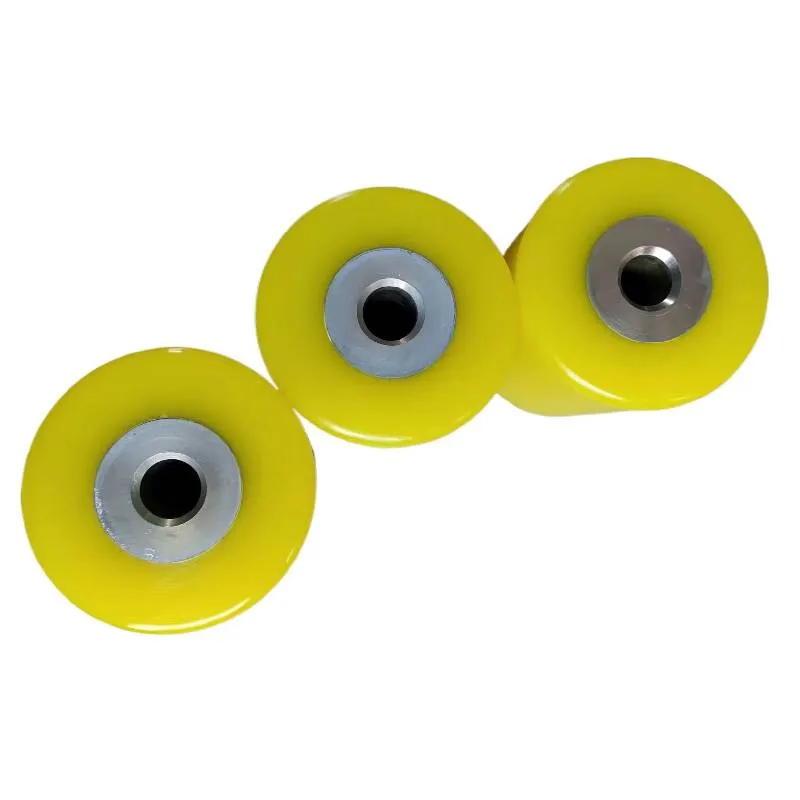
Understanding rubber hose ends begins with recognizing their function. These components serve as the final piece in a hose assembly, providing a secure and tight seal that prevents fluids or gases from escaping. Various designs and materials allow for tailored applications, with rubber being a popular choice due to its flexibility, durability, and resistance to environmental factors.
From a professional standpoint, choosing the right rubber hose end involves an assessment of several critical variables. First, understanding the fluid or gas type that will pass through the hose is essential. Rubber hose ends are versatile, accommodating a wide range of substances, but specific applications might necessitate speciality rubbers to resist corrosive materials or high temperatures.
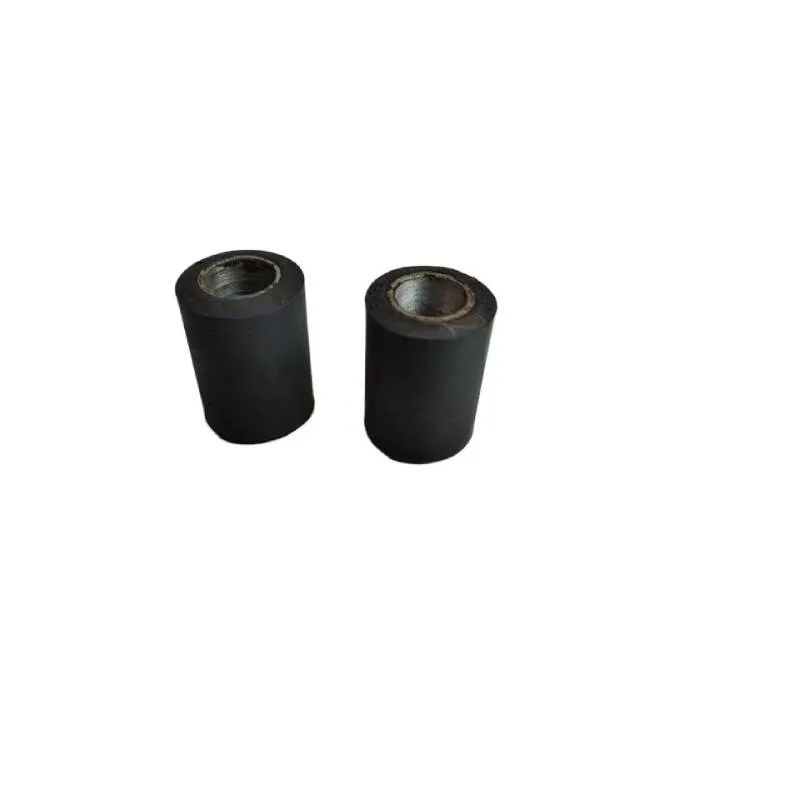
Equally important is the pressure rating. Hose systems operate under diverse pressure levels, and the rubber hose end must withstand these without failing. A mismatch here can lead to catastrophic failures, causing environmental spills or system downtimes, translating into significant financial losses. Therefore, it's advisable to consult the manufacturer's specifications and, if necessary, engage with an expert for tailored advice.
A significant aspect of rubber hose ends is their compatibility with the hoses they join. The industry offers ends in various sizes and threading styles, and selecting the correct type ensures a secure fit. This compatibility extends to both the internal diameter of the hose and the external fixtures, minimising wear and tear and extending the system's life.
rubber hose end
Real-world experience underscores the necessity for regular maintenance checks. Even with the correct end installed, environmental factors like UV exposure and extreme temperatures might degrade the hose end's integrity over time. Regular inspections for signs of wear such as cracks, brittleness, or elasticity loss can prevent unexpected failures.
In terms of authoritativeness and trustworthiness, the reputation of manufacturers and suppliers is paramount. Selecting hose ends from reputable companies can ensure they meet international safety and quality standards. Having certifications like ISO 9001 or equivalent is a testament to their commitment to quality, providing peace of mind to users that these components are tried and tested for reliability.
For product experts and industry professionals, understanding emerging technologies impacting rubber hose ends is essential. Advancements in material science may lead to superior alternatives, incorporating composites or reinforced fabrics that enhance the performance of traditional rubber hose ends.
Lastly, education plays a crucial role; those involved in specifying or installing these components should undergo periodic training. Understanding the latest industry standards, installation practices, and failure analysis techniques can maximize the efficiency and longevity of hose systems.
In summary, rubber hose ends, though small, have an outsized impact on the systems they are part of. Thoroughly understanding their design, application, and maintenance requirements form the crux of leveraging their full potential. By prioritizing these factors alongside continuous professional development and utilizing trusted sources, stakeholders can ensure optimal performance, affirming their standing as experts within their respective fields.