Rubber fittings and tubing have become essential components in various industries, ranging from automotive to healthcare. Understanding their significance requires delving into the specific properties and applications that make rubber such a versatile material. For businesses and professionals looking to optimize system performance, or for hobbyists involved in DIY projects, the choice and use of rubber components are critical for successful outcomes.
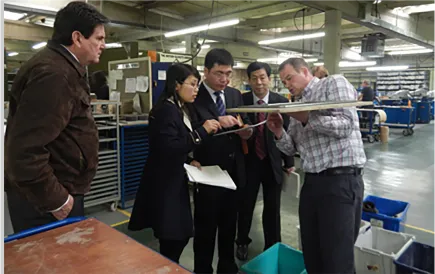
The flexibility of rubber tubing is one of its most celebrated characteristics. Unlike metal pipes or rigid plastic tubes, rubber offers a pliability that makes it ideal for tight spaces and intricate designs. This attribute ensures that systems remain leak-free even when they are subjected to continuous movement or vibration. Rubber's natural ability to absorb and dampen these forces is invaluable in sectors such as automotive, where engines and other components generate significant vibrations.
Moreover,
rubber fittings provide exceptional resistance to environmental factors. In industries where chemical resistance is paramount, such as pharmaceuticals or food processing, the selection of appropriate rubber material can mean the difference between a functioning system and a costly shutdown. Nitrile, silicone, and EPDM rubber, for instance, each provide varying levels of resistance to oil, heat, and chemicals, allowing engineers to select the perfect match for specific industrial needs.
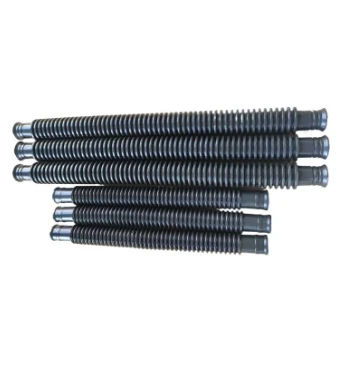
From a reliability perspective, rubber tubing and fittings offer significant benefits. Their ability to endure temperature fluctuations without compromising performance is a defining trait. This makes them ideal for HVAC systems, refrigeration, and other environments where temperature stability is crucial. Rubber components maintain their integrity over wide temperature ranges, ensuring that businesses do not face unexpected failures.
The durability of rubber is another compelling reason it remains a material of choice across industries. Even under constant exposure to different stresses, rubber tubing generally exhibits excellent wear resistance, which prolongs the lifespan of systems and reduces maintenance costs. Businesses can rely on rubber fittings to provide long-term solutions that maximize system uptime and efficiency.
rubber fittings tubing
A critical consideration when choosing rubber tubing and fittings is the regulatory compliance specific to the industry. For instance, medical and food-related applications require rubber that meets stringent health and safety standards, such as FDA approval. Ensuring compliance not only guarantees safety but also enhances the brand’s trustworthiness and authority in the market. Working with manufacturers and suppliers that adhere to these standards is paramount to achieving compliant and reliable systems.
In terms of installation and customization, rubber fittings and tubing offer significant advantages. Custom molding and extrusion allow for components that meet precise specifications, negating the need for excessive adjustments or modifications during installation. For projects requiring specific lengths, diameters, or unique shapes, rubber can be tailored effectively, streamlining the setup process and resulting in products that perfectly fit their intended applications.
The environmentally friendly nature of rubber is increasingly a part of conversation, particularly for businesses committed to sustainability. While natural rubber is biodegradable, synthetic rubbers have been developed with an emphasis on recyclability and reduced environmental impact. Selecting rubber tubing and fittings that support sustainable practices not only aids in regulatory compliance but also positions a company as a forward-thinking industry leader.
In conclusion, rubber fittings and tubing are indispensable in various applications, offering unmatched flexibility, environmental resistance, and durability. Their reliability across different temperature and chemical conditions makes them critical components in both specialized and broad industrial applications. When choosing rubber products, the key is to understand the specific requirements of each system and select materials that not only meet but exceed operational expectations. By doing so, businesses can ensure the efficiency and longevity of their systems while maintaining compliance and supporting sustainability initiatives.