Precision aluminum parts are at the forefront of innovation across various industries, heralded for their excellent strength-to-weight ratio, corrosion resistance, and versatility. As manufacturing demands increase, businesses are discovering new ways to leverage these durable components to achieve complex engineering feats. Drawing on real-world experience and backed by extensive expertise, this article explores the authoritative factors contributing to the adoption of precision aluminum parts, shedding light on their importance and reliability within the manufacturing domain.
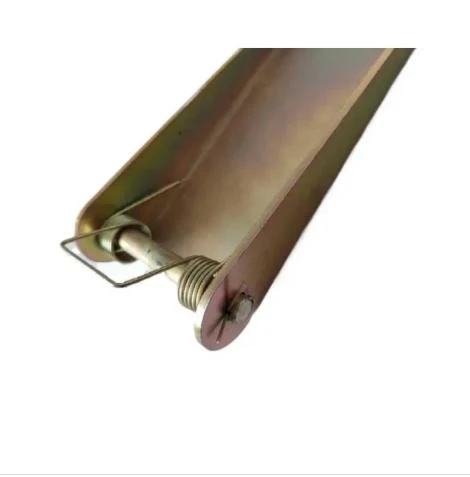
Precision aluminum parts owe their reputation to the remarkable combination of properties offered by aluminum alloys. Among the most notable is their lightweight nature. Engineers often prioritize lightweight materials for applications involving aerodynamics or fuel efficiency, such as in aerospace and automotive industries. Aluminum parts contribute significantly to reducing overall vehicle or aircraft weight without sacrificing durability, thus optimizing performance and reducing fuel consumption. Many manufacturers report improved fuel efficiency and load capacity since incorporating aluminum parts into their designs.
Another advantage of precision aluminum parts is their unparalleled corrosion resistance. Many components in industrial applications must withstand harsh environments, from exposure to chemicals to extreme weather conditions. Aluminum’s natural oxide layer provides an anti-corrosive shield, often eliminating the need for additional coatings or treatments that other metals might require. Manufacturing data illustrate that using aluminum parts can extend the lifespan of machinery and infrastructure enormously, translating to cost savings in both maintenance and replacement.
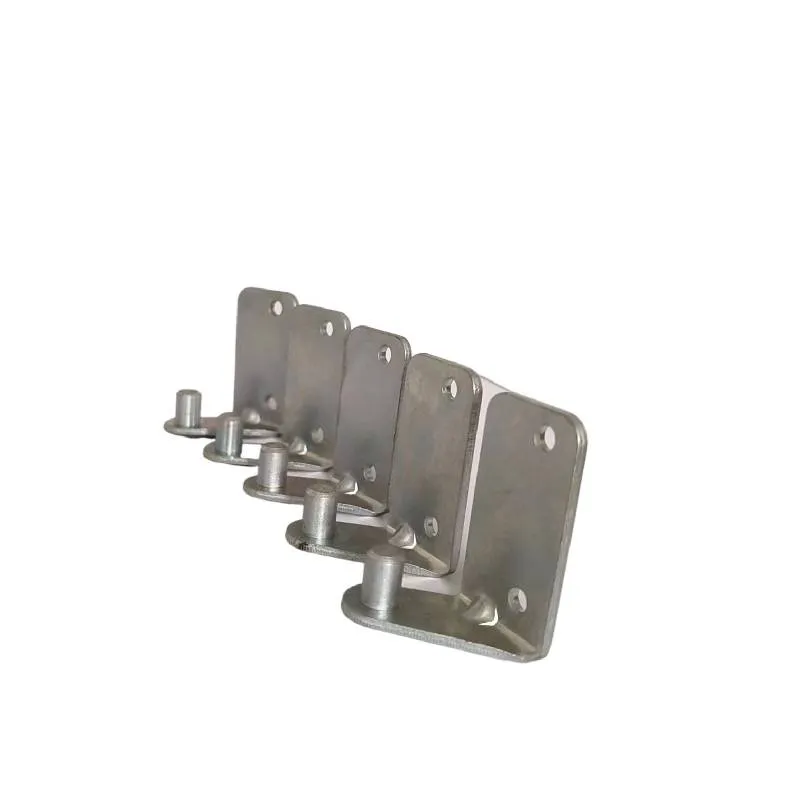
Moreover, aluminum is exceptionally versatile in terms of shaping and forming. Precision machining allows manufacturers to create complex geometries and intricate designs that might be impractical with other materials. For instance, industries such as electronics benefit immensely from the capability to produce finely detailed parts that accommodate contemporary design trends without compromising on functionality. This flexibility also makes aluminum an attractive option for custom solutions, where specific requirements call for bespoke components.
Precision aluminum parts continue to gain traction due to their sustainability. As industries become more eco-conscious, the recyclability of aluminum offers a significant edge. Almost 75% of all aluminum ever produced is still in use today, emphasizing its ability to be reused without degradation in quality. This recyclability reduces waste and decreases the environmental impact of production, aligning with global sustainability goals. Leading manufacturers describe significant reductions in their carbon footprint after pivoting to an aluminum-centric production model.
precision aluminum parts
Quality control is another foundational pillar when discussing the reliability of precision aluminum parts. Advanced technologies like computer numerical control (CNC) machining ensure that parts are produced to exact specifications, time after time. This precision manufacturing minimizes errors and variations, ensuring consistent performance across all produced components. Industry experts highlight how quality assurance procedures in aluminum part production exceed those of traditional materials, providing peace of mind to manufacturers who entrust critical applications to these parts.
The development and use of precision aluminum parts are supported by extensive industry research and specialized expertise. Technical insights provide manufacturers with the knowledge needed to optimize the use of aluminum alloys for specific applications, from composition analysis to mechanical stress tests. A rich body of authoritative literature and case studies available guides engineering decisions, fostering an environment of informed innovation.
Trustworthiness in the use of precision aluminum parts is bolstered by documented success stories and accrediting standards met by leading producers. Certifications from regulatory authorities and adherence to international standards like ISO and ASTM are commonplace among leading aluminum part manufacturers. Testimonials from global industry leaders further endorse their reliability, highlighting specific use cases where aluminum parts have been integral to groundbreaking projects.
In conclusion, precision aluminum parts are a cornerstone of modern manufacturing, applauded for their numerous benefits in strength, flexibility, sustainability, and reliability. Their transformative impact across industries is underpinned by a combination of academic research and hands-on expertise, setting a standard for innovative engineering solutions. As we look toward a future that champions efficiency and sustainability, the role of aluminum in shaping the next generation of technology and infrastructure is indisputable, promising continued advancements and applications.