Plastic worm wheels, though often overshadowed by their metal counterparts, have increasingly carved a niche for themselves in various industries. This shift is driven by a combination of cost-efficiency, performance, and a better understanding of engineering requirements which highlight their suitability for specific applications.

One notable advantage of plastic worm wheels is their incredible versatility. They come in a variety of shapes and sizes, adapting easily to a wide range of use cases. Industries from pharmaceuticals to miniature robotics have embraced plastic worm wheels for their lightweight, high strength-to-weight ratio, and resistance to wear and tear. Unlike metal worm wheels, which often require lubrication and regular maintenance, plastic variants can operate in highly demanding environments with minimal upkeep.
This represents a significant cost-saving aspect over the lifecycle of a product.
Experts in the field of material science often highlight the distinctive properties of high-performance polymers, such as polyacetal, polyamide (nylon), and polyphenylene sulfide, which are commonly used in the manufacturing of plastic worm wheels. These materials are chosen for their incredible mechanical properties, including high tensile strength, impact resistance, and dimensional stability, even in fluctuating temperatures. Moreover, these plastics exhibit excellent chemical resistance, making them ideal for adverse environments where metal worm wheels might corrode or degrade.
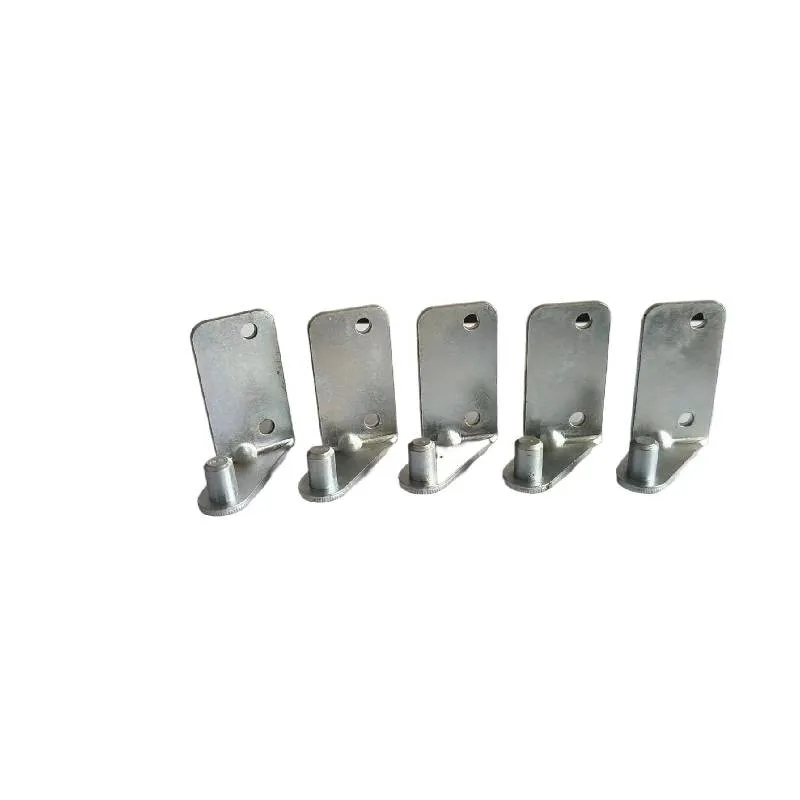
In sectors like food processing, where contamination can pose a significant risk, plastic worm wheels stand as champions due to their non-toxic and FDA-compliant nature. This non-metallic feature reduces the risk of foreign body contamination significantly, bolstering trust in products that reach the consumer. Food-grade plastics ensure that machinery stays operational without fear of imparting harmful substances onto consumables.
From an engineering perspective, the self-lubricating capability of some plastic worm wheel types cannot be overstated. This characteristic reduces the need for external lubricants, which further cuts down on maintenance costs and potential downtimes. The optimization of gear assembly to leverage these materials enhances operational productivity while maintaining a steady performance curve over time.
Despite their myriad of advantages, plastic worm wheels are not universal solutions. Situations requiring extreme load-bearing or high-temperature operations may still necessitate the use of their metallic counterparts. However, for applications where weight, cost, and minimal maintenance are critical factors, plastic worm wheels provide unmatched benefits. Engineers and designers attuned to these nuances make deliberate material choices that align best with their project specifications.
plastic worm wheel
The credibility of plastic worm wheels shines especially in the realm of prototyping and product development. Through the use of precision molding techniques, manufacturers can produce gears with tight tolerances, fostering trust in their reliability and performance. This capability allows for rapid iterations and testing, helping engineers refine their designs with greater agility and less cost.
Furthermore, as environmental concerns loom large, the eco-friendly nature of many high-performance plastics has become a polarizing topic. Recyclability and lower energy consumption in manufacturing processes give plastic worm wheels an edge over traditional metal gears amidst eco-conscious initiatives. For organizations aiming to lessen their carbon footprint, transitioning to such components aligns well with sustainability goals.
To cement authoritativeness, numerous case studies underline the efficacy of plastic worm wheels. In robotics, for example, projects highlight how these components afford agile movements, enhancing robotic functionality without the added burden of excess weight. Similarly, in automotive settings, their utility in non-load-bearing applications like window mechanisms reflects a growing preference for plastic solutions where applicable.
The choice between plastic and metal is far from straightforward and requires a comprehensive understanding of the application demands, operating environment, and longevity expectations. However, it is an expert understanding of these descriptors that can maximize cost savings, performance, and efficiency across a product's lifecycle.
In conclusion, the emergence of plastic worm wheels represents a paradigm shift towards more innovative, cost-effective, and sustainable engineering practices. Their standing in both expert discourse and practical applications underscores a growing trend where traditional materials find themselves challenged by new-age solutions—offering a glimpse into the future of industrial design and manufacturing optimization.