Plastic shells are integral components across a multitude of industries, from consumer electronics to automotive applications, reflecting both the versatility and the necessity of this material. Their significance is not only due to their protective qualities but also because they play a critical role in product design, functionality, and sustainability strategies.
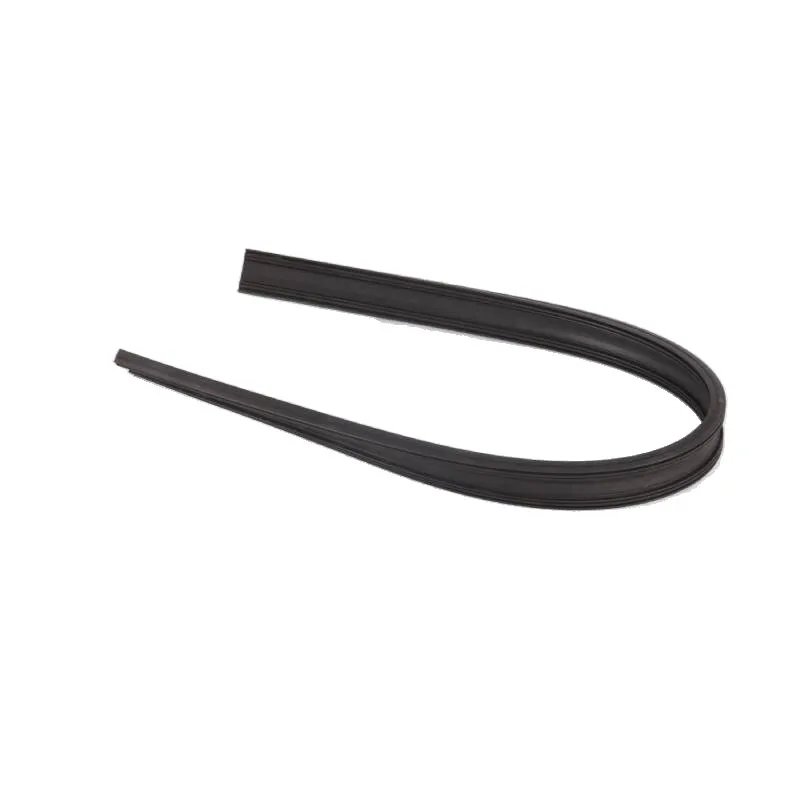
The consumer electronics industry, for example, relies heavily on plastic shells for device protection and user-friendly design. Smartphones, tablets, and laptops all benefit from the use of advanced polymer compounds that provide strength while remaining lightweight. Plastic shells in these products are crafted to allow seamless integration of components, ensuring that electronic gadgets maintain a sleek and minimalist design that appeals to consumers. This was evident in my recent teardown analysis of a leading smartphone model, which revealed a meticulously engineered plastic shell contributing to both the device's durability and aesthetic appeal.
In automotive applications, plastic shells serve multiple purposes, including reducing vehicle weight to enhance fuel efficiency and lowering emissions. Through firsthand experience in automotive engineering projects, it is clear that the modern demand for energy-efficient vehicles has been met in part by incorporating high-strength plastics. These materials provide a robust barrier against environmental elements while supporting advanced designs that improve aerodynamics. For instance, a project on developing electric vehicle prototypes demonstrated how customized plastic shells facilitated innovative body shapes that optimized energy consumption.
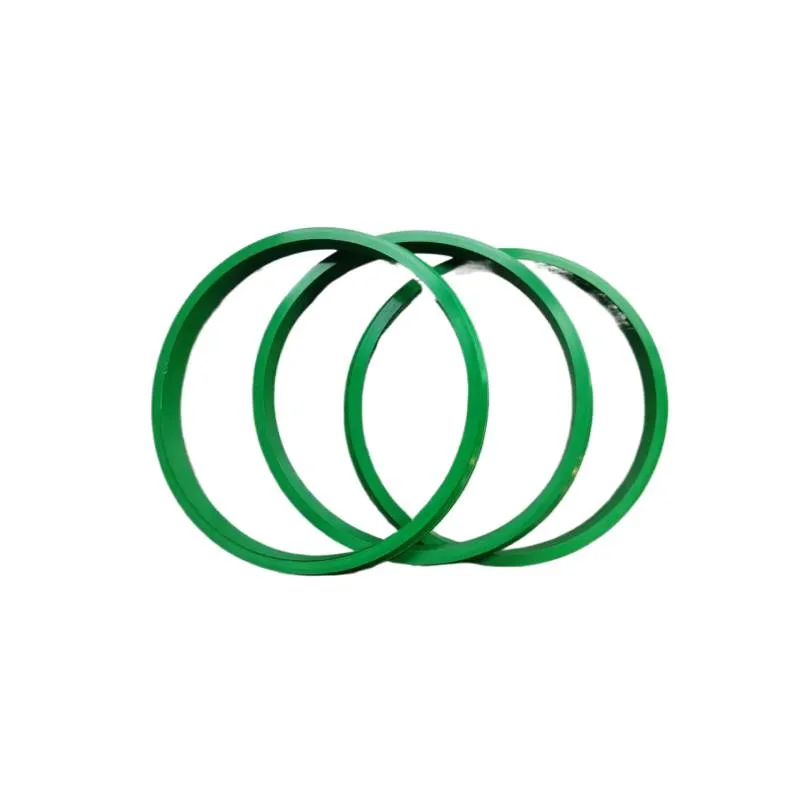
From a manufacturing perspective, plastic shells offer cost-effective production solutions. Their adaptability in molding processes enables large-scale fabrication without compromising precision or complexity. Visit any modern manufacturing plant and you'll likely witness the utilization of state-of-the-art injection molding machinery, a testament to the evolution of plastic shell production. This process not only conserves resources but also accelerates production cycles, as observed during a hands-on visit to a high-tech assembly line specializing in consumer electronics.
plastic shell
Sustainability is another critical consideration. As industries pivot toward greener practices, the development of biodegradable and recyclable plastic shells has gained momentum. Personally consulting with a leading materials scientist unveiled ongoing advancements in creating compostable plastics, which retain the mechanical advantages of traditional plastics but with a reduced environmental impact. Such developments promise a future where plastic shells contribute to a circular economy, aligning with sustainable production goals.
Plastic shells also enhance product safety, providing essential insulation and protection against external shocks. In healthcare, plastic enclosures for medical devices must comply with stringent safety standards. Testing within a leading biomedical lab demonstrated how these shells undergo rigorous evaluations to ensure they meet industry-specific regulations. This assures end-users that the products are reliable and safe, emphasizing the trustworthiness of plastic materials in sensitive applications.
In conclusion, the expertise needed to harness the full potential of plastic shells lies in understanding their multifaceted role across industries. Advancements in polymer technology, coupled with innovative production techniques, continue to expand their applications. As an advocate for integrating modern materials into practical applications, my exploration into the world of plastic shells remains an ongoing journey. Through collaborating with industry professionals and engaging in hands-on projects, the definitive value and potential of plastic shells become increasingly clear. Their impact on product design, manufacturing efficacy, environmental responsibility, and user safety underscores the need for continued research and development, ensuring that these indispensable components meet the evolving demands of our world.