Plastic pulley wheels have revolutionized a myriad of industries by offering an unparalleled balance of durability, efficiency,
and cost-effectiveness. These components are integral in various mechanical systems, proving their worth through the seamless transmission of force in everyday machinery. The grip of plastic pulley wheels on the market showcases not just a trend, but an evolution in engineering and material science.
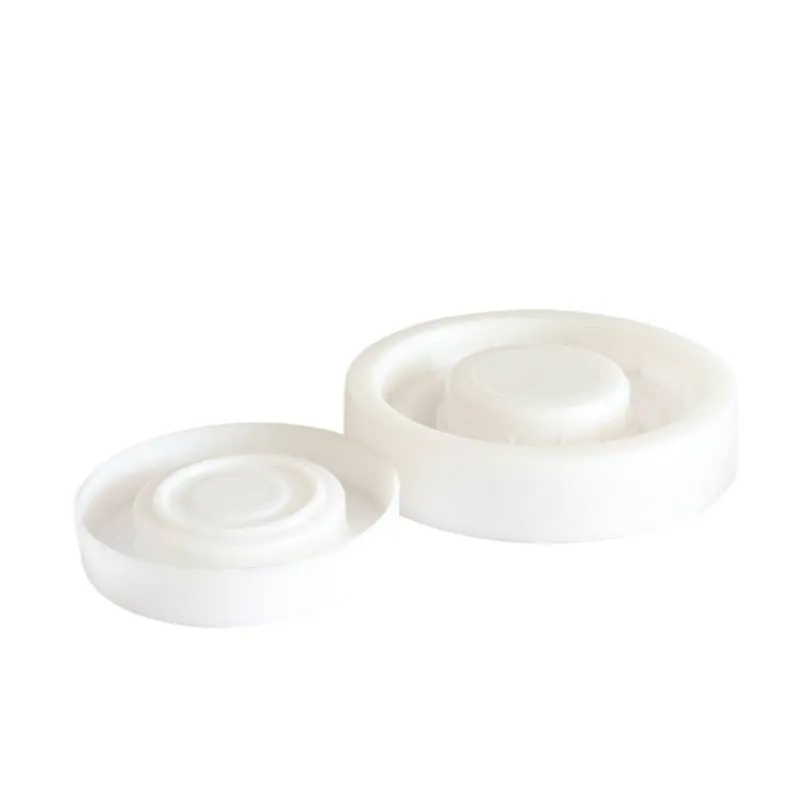
For industries looking to optimize performance while minimizing weight and cost, plastic pulley wheels present a compelling solution. Their non-corrosive nature means they outperform traditional metal pulleys in environments where moisture or chemical exposure is a concern. This resilience contributes to longer life spans, reducing the need for frequent replacements and maintenance, which are critical concerns for industrial operations seeking to optimize uptime and reliability.
Moreover, their role in industries as diverse as automotive, manufacturing, and consumer electronics speaks volumes about their versatility. In automotive engineering, for instance, the light weight of plastic pulleys contributes to better fuel efficiency and reduced emissions, goals at the forefront of modern engineering challenges. Meanwhile, in consumer electronics, these pulleys help in the precise movement of components within confined spaces, enabling the sleek designs and reliable functionality consumers expect.
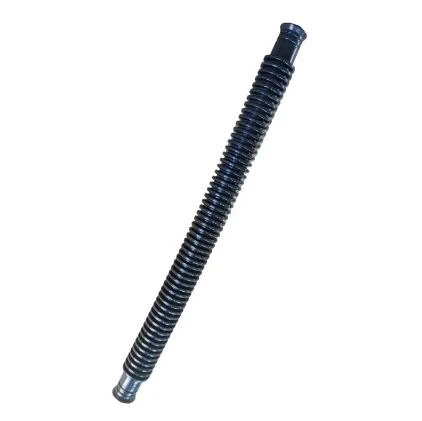
Expertise in material science has driven innovations in the design and functionality of plastic pulley wheels. Advances in polymer technology have led to plastics that are not only stronger but also more resistant to wear and temperature extremes. Nylon, polycarbonate, and acetal are commonly used polymers, each offering distinct advantages. Nylon provides an excellent balance of strength and flexibility, while polycarbonate offers high impact resistance and dimensional stability. Acetal, on the other hand, is prized for its low friction and excellent machinability.
plastic pulley wheels
Authoritativeness in the field of pulley design is further exemplified by the work of leading manufacturers who have dedicated extensive R&D to perfecting the balance between material properties and mechanical performance. These manufacturers test their products rigorously, addressing crucial factors such as load capacity, rotational speed, and thermal environment to ensure peak performance.
The trustworthiness of plastic pulley wheels is not just anecdotal. Industries globally deploy these components in essential applications, with testimonials from engineers who praise their consistency and reliability. Additionally, compliance with international standards and certifications is further evidence of their reliability, making them a safe bet for businesses that prioritize both quality and compliance.
In conclusion, the strategic selection of plastic pulley wheels over traditional materials manifests not just in improved performance metrics but also in economic benefits. By reducing maintenance costs and extending the lifecycle of mechanical systems, these wheels contribute toward more sustainable and efficient industrial practices. The innovations in plastic pulley technology not only reflect advancements in material science but also epitomize a commitment to pushing boundaries in industrial efficiency and design. For any industry professional or business looking to harness these benefits, plastic pulley wheels present an informed and strategic choice backed by tangible expertise, authoritative insight, and trusted reliability.