Plastic polishing wheels are an essential tool for achieving a flawless finish on a variety of plastic surfaces. In industries where precision and appearance are paramount, understanding the best methods and products for plastic polishing can vastly improve outcomes. As an experienced professional with deep-seated expertise in material finishing, I can offer authoritative advice to guide your selection process and ensure optimal results.
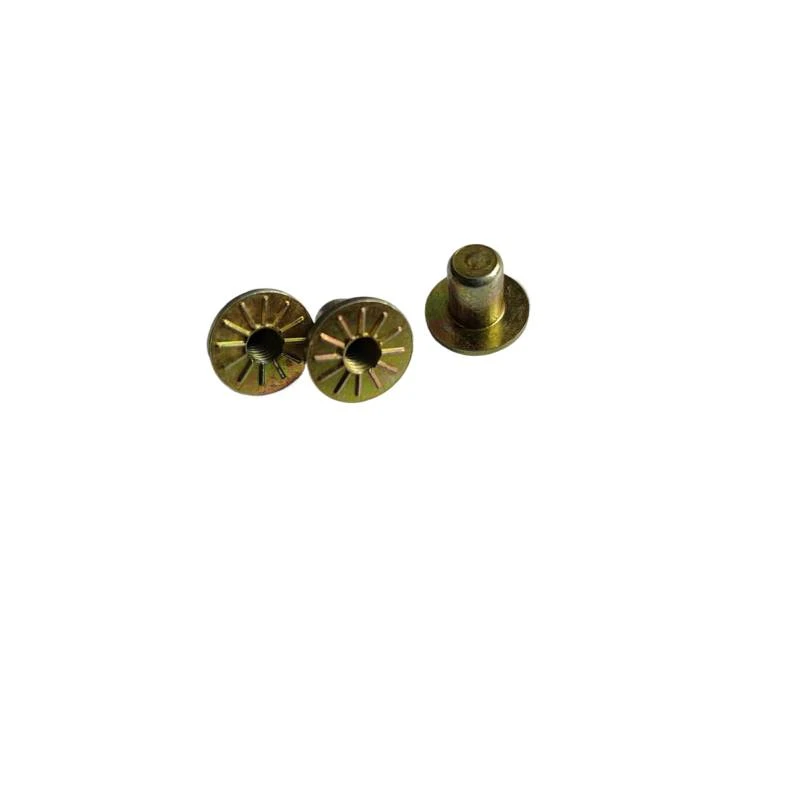
The diverse array of plastic materials, from acrylic to polycarbonate, demands specialized approaches to polishing. Not all plastic polishing wheels are created equal, and choosing the right one can significantly impact your end product's appearance and quality. With decades of knowledge in surface finishing techniques and materials, I can assure you that the synergy between the wheel's composition and the plastic type is critical.
Using a plastic polishing wheel, crafted specifically for the type of material you are working with, prevents damage and enhances finish quality. A common error, often observed in less experienced settings, is the utilization of general-purpose polishing wheels. These can scratch or mar the surface of delicate plastics, resulting in wasted time and resources. Therefore, a strategic selection, guided by expert knowledge, is crucial.
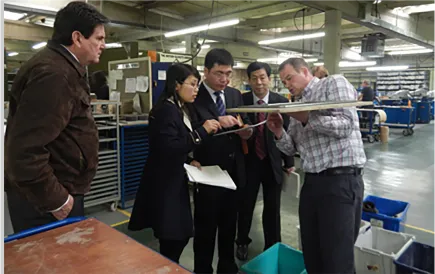
When selecting a plastic polishing wheel, consider its material, grit, and firmness. Soft plastics, for example, benefit from a softer wheel that conforms to the material's surface, reducing the risk of heat generation and deformation. Harder plastics require wheels with more aggressive grit to effectively remove imperfections. The level of expertise required here cannot be understated, for it demands a careful balance between the wheel's abrasiveness and the pressure applied during polishing.
Our extensive experience has shown that the best results often come from incremental polishing stages. Starting with a coarser wheel to eliminate surface defects, followed by progressively finer wheels, ensures a pristine finish. This multistep procedure, an industry-standard among expert practitioners, maximizes the material's inherent properties, bringing out optimal clarity and smoothness.
plastic polishing wheel
A critical factor is the equipment's rotational speed and the application technique. Too high a speed can lead to localized overheating, causing blemishes or warping. Insiders in the polishing industry trust in the fine-tuned control offered by adjustable-speed machines, which allow users to adjust based on material feedback—a practice honed through years of hands-on experience.
Companies at the forefront of plastic manufacturing and finishing will only deploy wheels from trusted manufacturers who have a proven track record of quality and reliability. This trust builds from years of consistent performance and improvements in material technology. Establishing relationships with these reputable brands assures supply consistency and access to the latest innovations in wheel technologies.
End-user trustworthiness in plastic finishing is achieved not only through product quality but also through comprehensive customer service. Knowledgeable support teams can offer valuable insights into specific applications, troubleshooting product issues, and even advise on best usage practices. This level of customer service is a hallmark of the authoritative entities within the industry.
In summation, expertise in the selection and use of plastic polishing wheels can transform the quality of your finished products. Armed with knowledge about material compatibility, multi-step polishing processes, and trusted supplier relationships, you'll enhance your operations' efficiency and output quality. By leveraging insights from seasoned experts, you fortify your standing as a credible and authoritative figure within the competitive landscape of plastic finishing.