Plastic gear wheels have transformed modern engineering, playing an indispensable role in numerous applications due to their lightweight, flexibility, and cost-effectiveness. Through decades of use and development, these gear wheels have proven their worth in industries ranging from automotive to electronics.
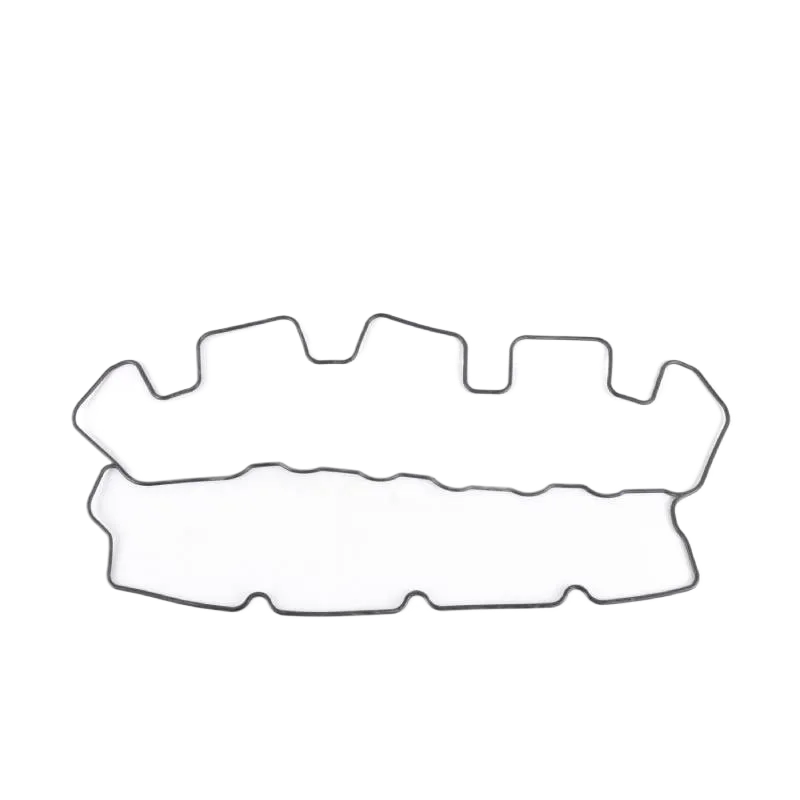
In the automotive industry, plastic gear wheels are highly valued for their quiet operation and resistance to corrosion. Unlike their metal counterparts, plastic gears are less prone to rusting, enhancing their longevity and reducing maintenance time. For vehicles, where weight is a critical factor, the use of plastic gear wheels contributes to overall vehicle efficiency by lowering fuel consumption. Engineers specializing in automotive design often endorse plastic gears for applications such as windshield wipers, seat adjusters, and even in hybrid systems. Their ability to operate smoothly in tandem with electronic systems showcases their versatility and performance reliability.
Electronics and consumer goods also benefit significantly from the integration of plastic gear wheels. Devices such as printers, cameras, and household appliances incorporate these gears for their precision and adaptability. The precision molding process of plastic gears allows for intricate designs that meet the industry's exacting standards. Electronics manufacturers recognize the advantage of these gears in offering quiet operation, which is a critical feature in consumer satisfaction, providing products that maintain the serenity of home and office environments.
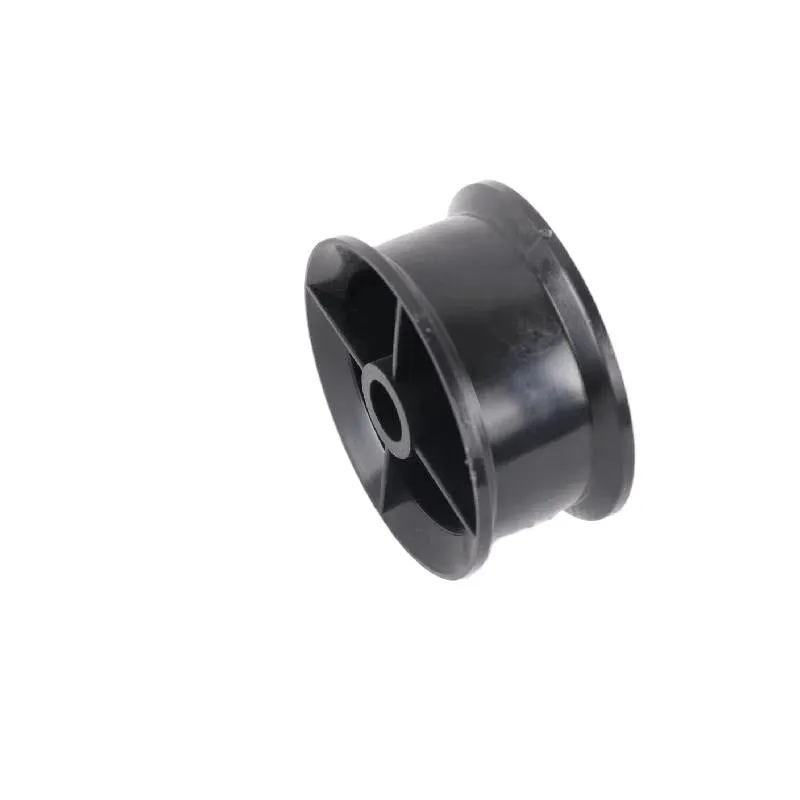
The expertise embedded in producing plastic gear wheels is evident in their material composition and design adaptability. High-performance engineering plastics like Nylon, Acetal, and Polycarbonate are frequently chosen for their strength and durability. Materials like these are engineered to endure high torque and wear conditions, holding up against thermal and mechanical stress. Such properties are verified through rigorous testing and standards such as ISO and ASTM, underpinning their authoritative presence in the market.
plastic gear wheels
The trustworthiness of plastic gear wheels as reliable components is underscored by the extensive research and development invested in them. Manufacturers continuously engage in improving material properties and gear design, leveraging advanced technologies such as 3D printing and CAD simulations. These efforts ensure that plastic gear wheels not only meet but often exceed performance expectations in various demanding environments.
Innovations in plastic gear wheel technology continue to evolve, introducing enhancements such as self-lubricating properties and improved load distribution. The application of finite element analysis (FEA) in their design process allows engineers to predict and optimize their real-world performance, building confidence among end-users and stakeholders regarding their dependability.
Plastic gear wheels represent an area where expertise translates into tangible benefits for various industry sectors. Their ongoing development and application attest to their authoritative and trustworthy nature. Industry veterans continue to advocate for their use, recognizing their role in cutting-edge technological advancements and sustainable practices. With their extensive track record and continuous innovation, plastic gear wheels remain pivotal in shaping the future of mechanical and electronic systems.