Plastic flanged wheels are critical components in various industries, offering a combination of durability, adaptability, and cost-efficiency. As someone who has dealt extensively with these components, I've come to understand their profound impact on product design and functionality. Here’s a detailed insight into their application and benefits, aimed at helping you make informed decisions.
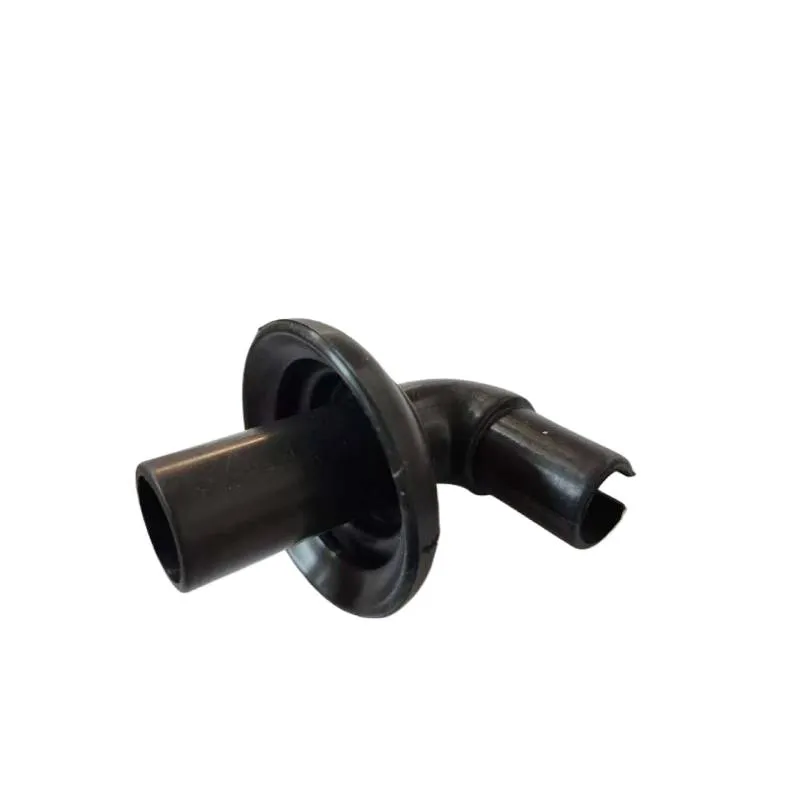
In modern manufacturing and industrial applications, plastic flanged wheels have emerged as a versatile alternative to metal wheels. Their rise in popularity can be attributed to their lightweight nature and corrosion resistance, which are crucial in environments that demand resilience and longevity. From automotive assemblies to intricate conveyor systems, plastic flanged wheels have found a niche by providing a solution that traditional materials like metal cannot.
When designing systems that involve movement and load-bearing elements, choosing the right wheel type is paramount. Plastic flanged wheels offer an edge due to their high resistance to many chemicals, which extends their usability in chemical plants and factories where exposure to corrosive substances is high. For instance, in the pharmaceutical industry, equipment often encounters stringent hygiene and chemical resistance standards, making plastic flanged wheels an ideal choice.
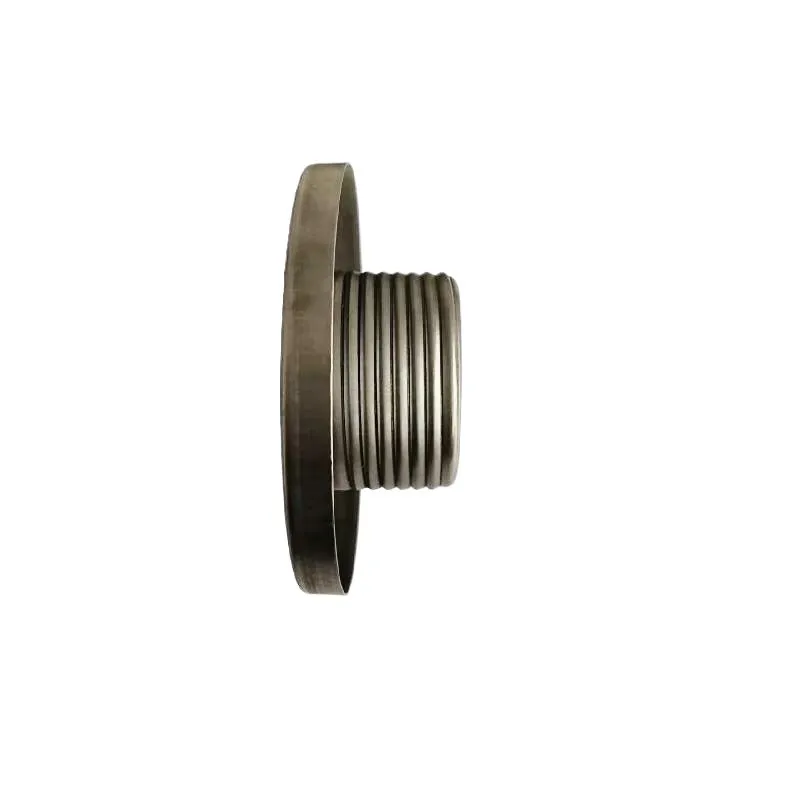
Plastic flanged wheels also excel in reducing noise pollution, an often overlooked but essential factor in environments like hospitals and schools where quiet operation is critical. Unlike metal wheels, which can produce significant noise, plastic wheels provide smooth, noiseless operation, enhancing the overall working conditions.
However, expertise in selecting the appropriate plastic material is vital. Different plastics offer varying benefits; for instance, Nylon provides robustness and low friction, whereas Polypropylene is noted for its impact resistance and cost-effectiveness. Expertise in polymer science enables a nuanced selection that aligns with specific application needs, maximizing performance and longevity.
plastic flanged wheels
Authoritative manufacturers often undertake rigorous testing to ensure their plastic flanged wheels meet industry standards. These tests might include load capacity evaluations, wear resistance assessments, and chemical exposure tests. By choosing wheels from reputable suppliers, you benefit from components that have proven reliability, backed by scientific research and thorough quality checks.
The trustworthiness of plastic flanged wheel suppliers is crucial. Always seek companies that provide transparent information about their manufacturing processes and the materials used. Certifications such as ISO 9001 can be indicators of a manufacturer’s commitment to quality and consistency. Reviews and testimonials from previous clients can also be invaluable, offering real-world insights into the performance and reliability of the wheels in different settings.
In terms of installation and maintenance, plastic flanged wheels are notably advantageous. They are often designed for easy installation, reducing setup time and costs. Maintenance is minimal due to their self-lubricating properties, which help in prolonging the service life without frequent intervention. This ease of use translates into lower long-term costs and less downtime, critical advantages for operations where efficiency is paramount.
In conclusion, the decision to integrate plastic flanged wheels into your system design should be informed by an understanding of their material properties, testing standards, and the reputation of the supplier. With the right expertise and insights, these wheels can significantly enhance the functionality and durability of your products, providing a competitive edge in demanding industrial environments.