Designing plastic parts requires a nuanced understanding of key factors that influence both functionality and manufacturability. It's not merely about creating shapes; it's about engineering components that fulfill exact specifications while ensuring cost-effectiveness and sustainability. Whether for automotive, consumer electronics, or medical devices, the principles of plastic part design remain consistent and are crucial for successful product development.

One of the primary considerations in plastic part design is material selection. Different applications necessitate distinct plastic resins, each offering unique properties. For instance, polycarbonate is often favored for its strength and impact resistance, whereas polyethylene might be chosen for its flexibility and chemical resistance. A deep understanding of these materials and their behaviors under different conditions—temperature fluctuations, mechanical stress, and environmental exposure—is critical. Professionals in this field must be adept at evaluating these materials based on their mechanical properties, sustainability, and cost-effectiveness.
Furthermore, maintaining manufacturability without compromising design integrity is a pivotal aspect. This is where experience in DFM (Design for Manufacturability) becomes invaluable. Applying DFM principles ensures that the design can be efficiently transitioned into mass production. It involves considerations like wall thickness uniformity, appropriate use of drafts, radius incorporation, and maintaining tolerance levels. These elements not only facilitate the injection molding process but also minimize defects, thereby reducing waste—a testament to environmental consciousness.
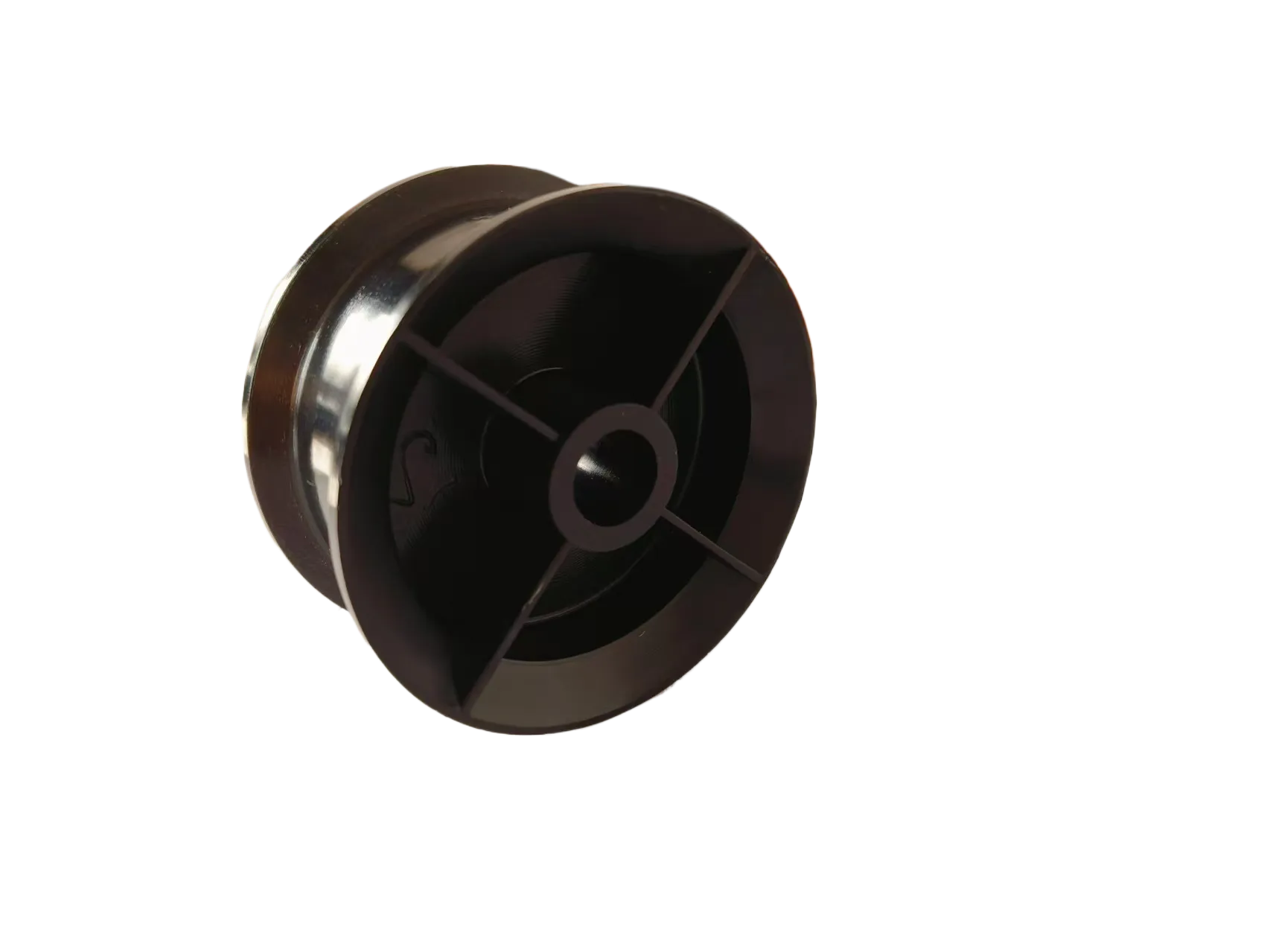
Complex geometries are often at the heart of innovative designs. However, they can pose significant challenges during manufacturing. Techniques such as finite element analysis (FEA) allow designers to simulate performance under various conditions, identifying potential failure points before actual production. This proactive approach enhances the overall reliability and functionality of the final product. Insightful application of FEA requires expertise and experience, solidifying the professional’s authoritative role in the design process.
plastic part design
The intersection of technology and design cannot be overstated. Advanced CAD (Computer-Aided Design) software has revolutionized how designers approach plastic part design. These tools offer precise control over complex geometries and integrate seamlessly with 3D printing technologies, allowing for rapid prototyping. Rapid prototyping is particularly advantageous as it offers real-world iterations of design concepts, enabling designers to test and refine parts efficiently. This iterative process not only enhances the aesthetic and functional aspects of the design but also builds trust with stakeholders, who appreciate the transparency and dynamism in development.
Sustainability is increasingly influencing design decisions across industries. Eco-friendly materials and circular design approaches, where parts are designed for disassembly and recycling, are gaining traction. Engineers proficient in sustainability principles are not only likely to enhance product lifecycle and reduce environmental impact but also to appeal to increasingly eco-conscious consumers. This awareness and ability to integrate sustainability into designs bolster credibility and trustworthiness, aligning with global priorities.
In terms of expertise, staying abreast of industry trends and innovations is essential. Trade shows, webinars, and professional courses provide ongoing education and insight into the latest technologies and methodologies emerging in plastic part design. Partnerships with material scientists and engineers further amplify a designer’s ability to innovate and solve complex design challenges, leveraging their combined knowledge to create superior, market-leading products.
Conclusively, expertise in plastic part design is demonstrated through a comprehensive understanding of materials, manufacturing processes, and technological tools, all while maintaining a keen eye on sustainability. This field demands a careful balance of creativity and engineering rigor, ensuring that designs are not only feasible but also pioneering in their utility and environmental consideration. The scrutiny and skill involved fortify the designer’s authoritative voice, positioning them as trustful leaders in the evolving landscape of product development.