Harnessing the full potential of a plastic buffing wheel can transform not only the appearance of your products but also the performance and durability of your processes. As an experienced professional in the world of surface finishing, I've seen firsthand how a seemingly simple tool can become a cornerstone of effective and efficient polishing work. Here's what makes plastic buffing wheels indispensable and how their characteristics can align with the critical aspects of your business demands.
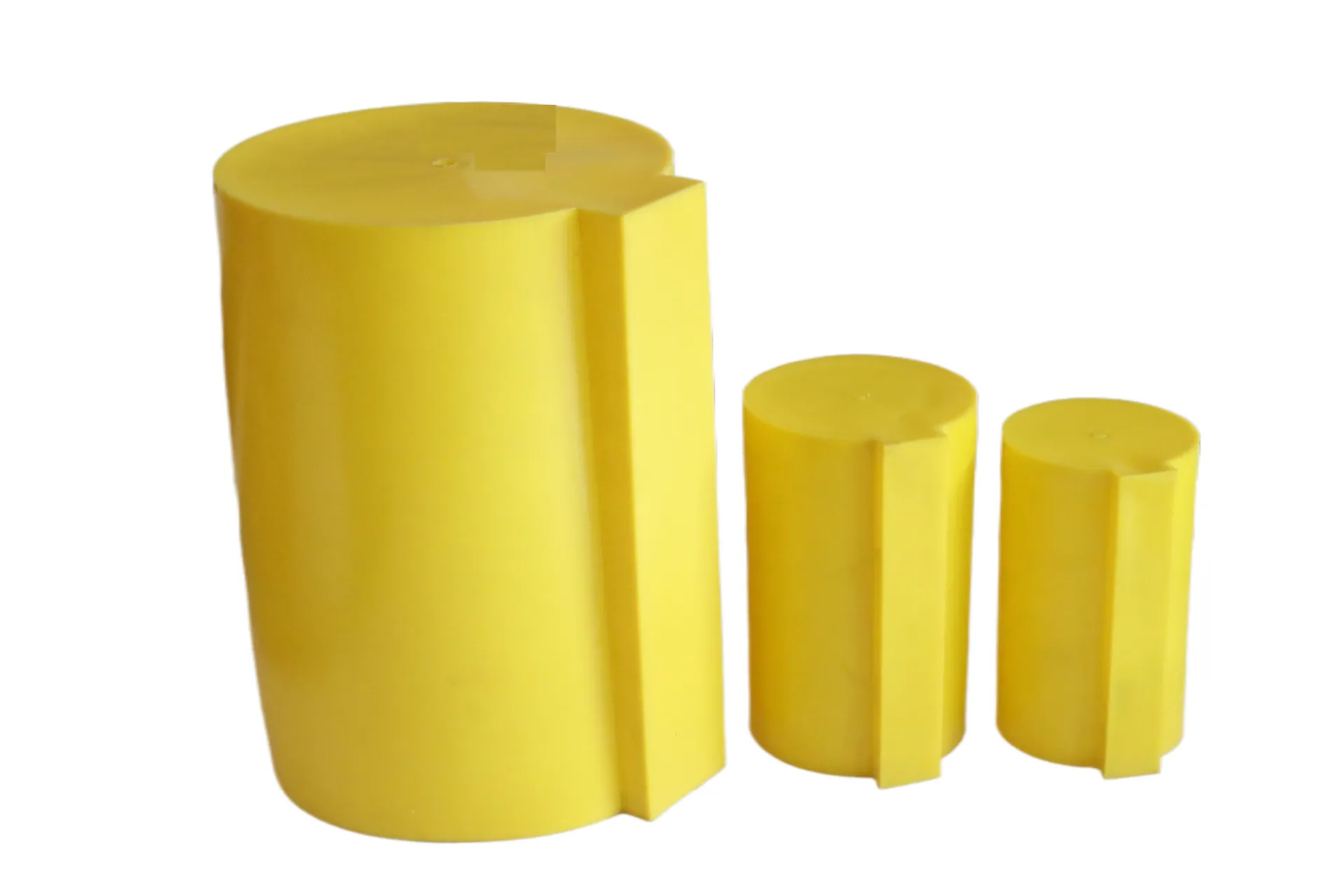
Plastic buffing wheels stand out for their unique ability to balance aggression and gentleness. Made from high-quality synthetic materials, these wheels provide a consistent, controlled cutting action that minimizes heat build-up. For professionals in industries ranging from automotive restoration to delicate jewelry crafting, this attribute is crucial. Heat can distort or damage fragile surfaces, so relying on a tool that minimizes this risk while still performing its task effectively speaks volumes about its design and intent.
For instance, in the automotive industry, detailers often face the challenge of removing scratches and oxidation from various finishes. Plastic buffing wheels, with their adaptable nature, excel in integrating seamlessly with different polishing compounds and waxes. By delivering just the right pressure and friction, detailers can achieve a mirror-like finish without compromising the integrity of the car’s paintwork. Over the years, the advancement in the polymers used has only enhanced their reliability and efficiency.
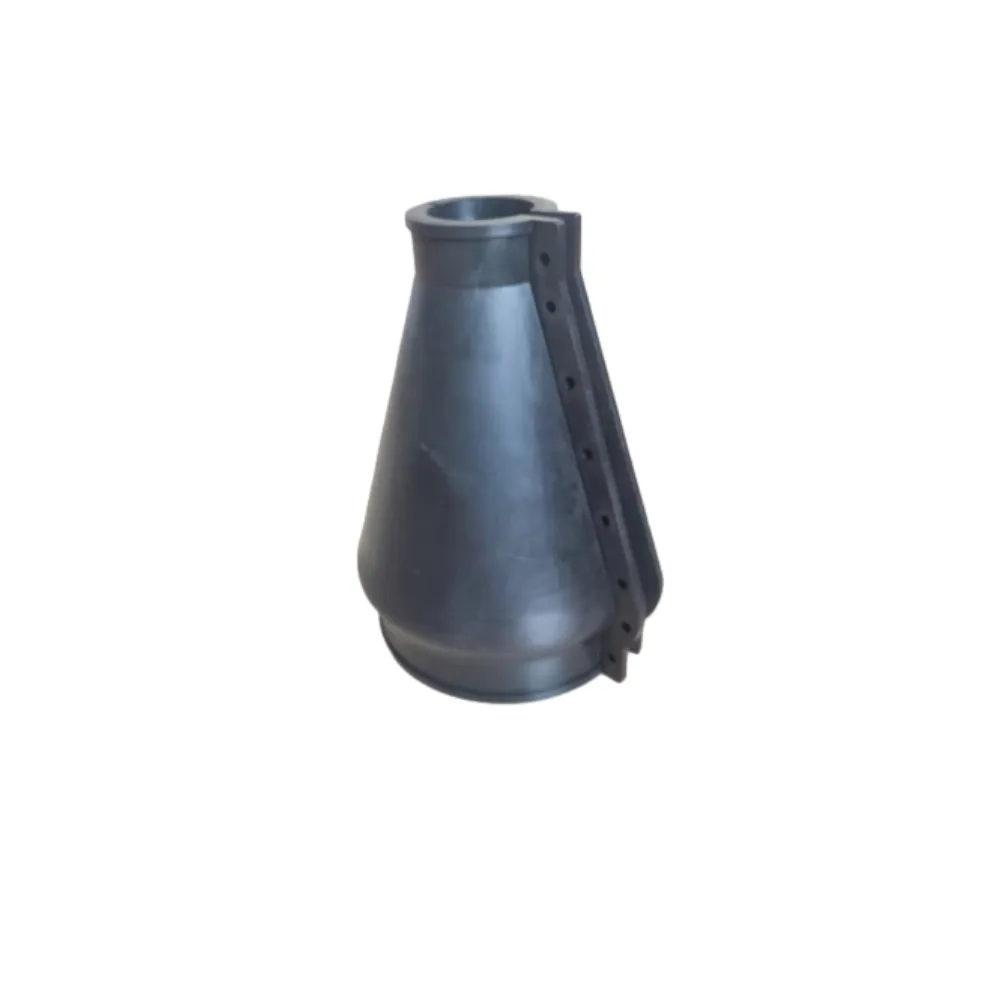
The expertise in utilizing plastic buffing wheels lies in understanding the wheel's construction. Each layer within these wheels serves a distinct purpose, often engineered to cater to specific tasks like cutting, polishing, and finishing. The ability to swap or change these layers means that one wheel can serve various facets of a production line or workshop duties, providing versatility and cost-effectiveness. This multi-functionality not only saves time but ensures a uniform output, showcasing the product’s hidden luster.
plastic buffing wheel
Authority in recommending plastic buffing wheels comes from years of observation and active research into material science. The evolution of plastic composites has allowed manufacturers to introduce products that are lighter, more flexible, and primarily environmentally sustainable. Historically, traditional buffing methods often led to excessive material wastage and required frequent replacements. Conversely, plastic buffing wheels have surged as a preferred alternative due to their longer shelf life and durable performance across more cycles.
Trust earned through these buffing solutions isn't just about the wheel itself; it's about the ecosystem it creates. Workshops and factories that employ these wheels witness a reduction in operative downtime, a common hiccup in hyper-competitive manufacturing processes. As the use of plastic buffing wheels becomes more widespread, the community around them grows richer in shared experiences and advice. Forums and professional networks are abundant with testimonials and user feedback, substantiating their merits beyond promotional declarations.
In the quest for efficiency, reliability, and superior quality, embracing the plastic buffing wheel has proven to be more than a mere choice—it's a strategic advantage. As we continue to innovate and adapt in the face of evolving manufacturing challenges, tools like these wheels remind us of the impact of thoughtful engineering and material science, affirming their place in our toolkits and workflows for years to come.