In the realm of material handling and manufacturing, the small yet invaluable plastic ball caster has proven itself to be a pivotal component in optimizing operational efficiencies. Integrating such elements into equipment may sound minor but introduces an impactful shift in maneuverability and product lifecycle. For industries ranging from furniture manufacturing to intricate machinery design, plastic ball casters offer a lightweight yet durable solution that addresses several of the complexities associated with movement and positioning.
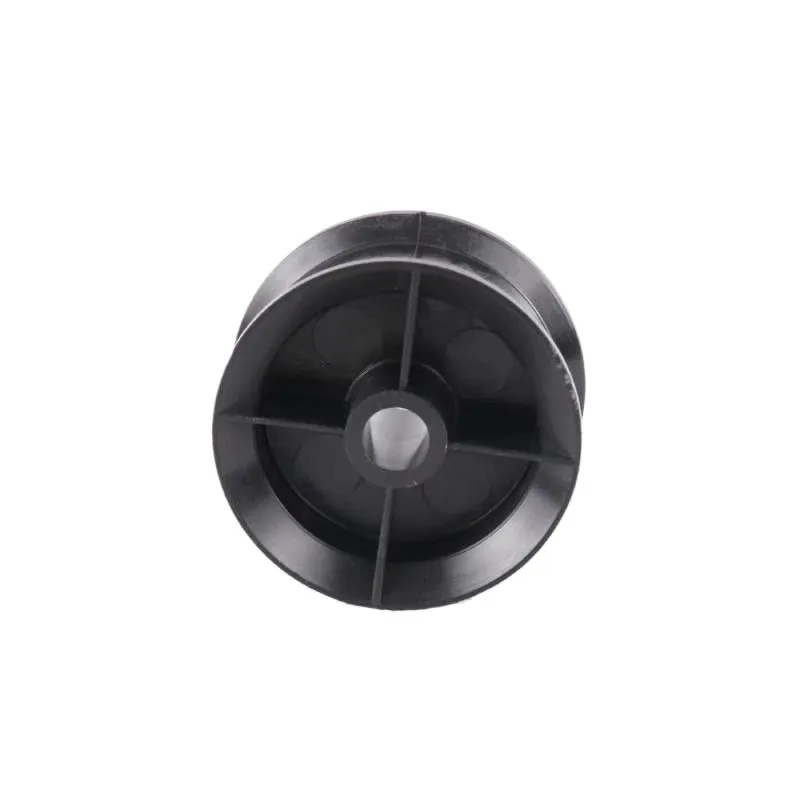
Foremost,
let's delve into their unparalleled experience in diverse industrial applications. Unlike metal casters, plastic ball casters present a lightweight advantage without compromising the load capacity significantly. This feature is particularly advantageous in sensitive environments like the electronics industry, where the combination of weight and movement finesse is critical to maintaining product integrity. Additionally, the composition of plastic inherently contributes to noise reduction, an asset in environments where noise pollution is a concern, such as in hospitals or office settings.
Expertise in selecting appropriate materials compatible with various environmental conditions is key when discussing plastic ball casters. The engineering behind these components often involves polymers like nylon or polyurethane. Each offers a unique set of attributes for particular needs; for instance, nylon excels in rigorous mechanical conditions with its robust resistance to wear and tear, while polyurethane provides superior shock absorption and a smooth glide. Knowledge of material science allows industries to tailor plastic ball casters perfectly to their specific operational requirements, maximizing efficacy and longevity.
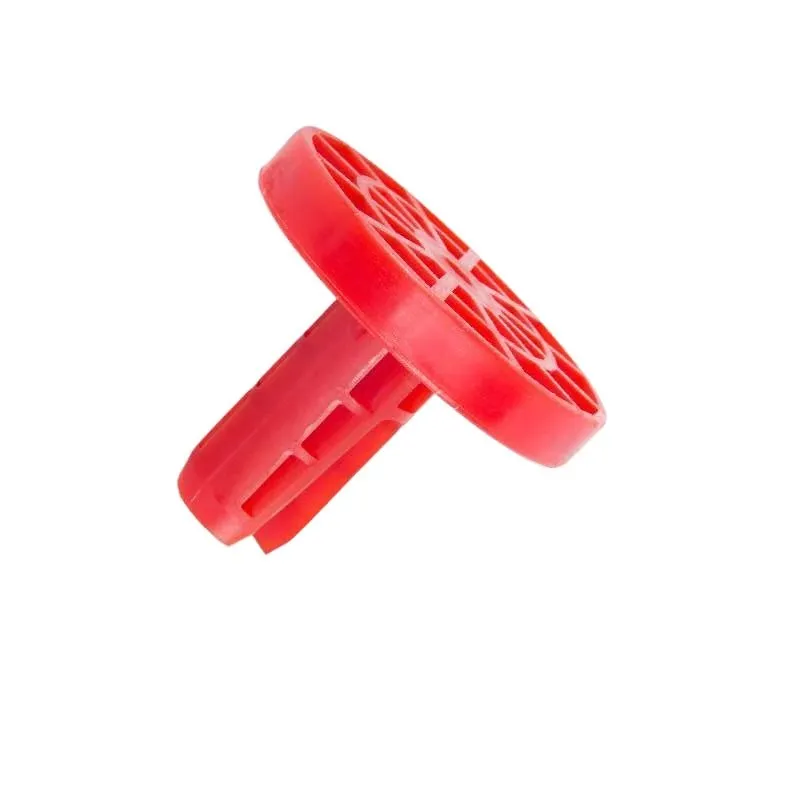
plastic ball caster
From an authority perspective, numerous authoritative entities have sanctioned the use of plastic ball casters, particularly highlighting their environmental benefit. As the global shift leans towards more sustainable manufacturing practices, plastic ball casters emerge as a frontrunner in reducing carbon footprints. Their production and lifecycle management result in significantly reduced energy consumption compared to traditional materials like steel. Various standards bodies and regulatory agencies now recognize and often incentivize adopting such smarter, greener solutions in design and manufacturing.
Trustworthiness remains a critical pillar upon which the use of plastic ball casters is founded. Over decades of evolution, these components have demonstrated an exceptionally high dependability rate in multiple sectors. Modern advancements in plastics technology ensure these casters are not only reliable under normal conditions but also maintain integrity under extreme pressures and temperatures. This resilience reassures manufacturers of reduced maintenance costs and lower replacement frequencies, further securing their reputation as a cost-effective and durable solution.
In summary, the strategic incorporation of plastic ball casters within industrial frameworks speaks volumes about their capacity to influence logistics positively and efficiently. By offering experienced insight into maneuverability options, having expert knowledge of material compatibility, upholding authoritative endorsements for sustainability, and proving trustworthy reliability, plastic ball casters indeed carve a niche as essential components across industries. In the pursuit of optimized operational excellence, they remain unsurpassed allies in maneuverability, fundamentally transforming how modern industries approach the complexities of movement within manufacturing and design.