In the demanding world of industrial machinery, the role of precision components like oil seal metals is pivotal. More than just minor parts, they are the silent champions ensuring optimal performance and longevity of heavy-duty equipment. Understanding their intricacies can significantly elevate your machinery's efficiency and lifespan—a realization that sets industry leaders apart from the rest.
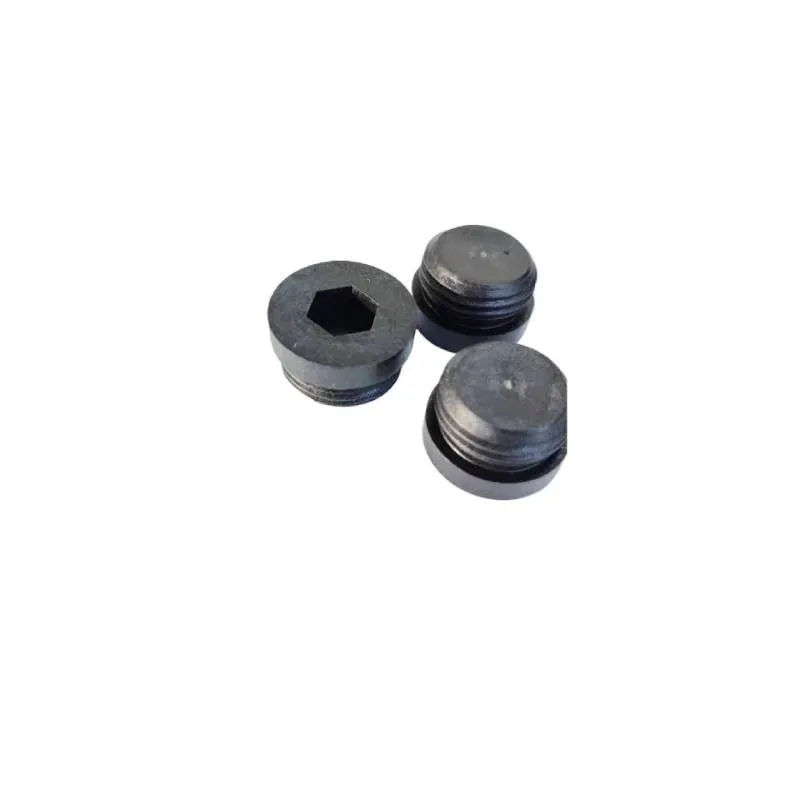
Oil seal metals are crafted from various robust materials designed to withstand harsh environments. Their core function is to contain fluids within a device and prevent any contaminants from entering. Crafted with rigorous standards, these seals act as a barrier against dust, moisture, and other potential contaminants that could degrade the machinery's performance.
In industrial applications, where high-speed and high-pressure operations are routine, the choice of oil seal metal becomes even more critical. Engineers often opt for metals like stainless steel, carbon steel, and other specialized alloys. Each material offers unique properties such as enhanced resistance to corrosion, improved tolerance to extreme temperatures, and exceptional mechanical strength. Stainless steel, for instance, is renowned for its resistance to rust and corrosion, making it ideal for environments exposed to humidity and corrosive substances.
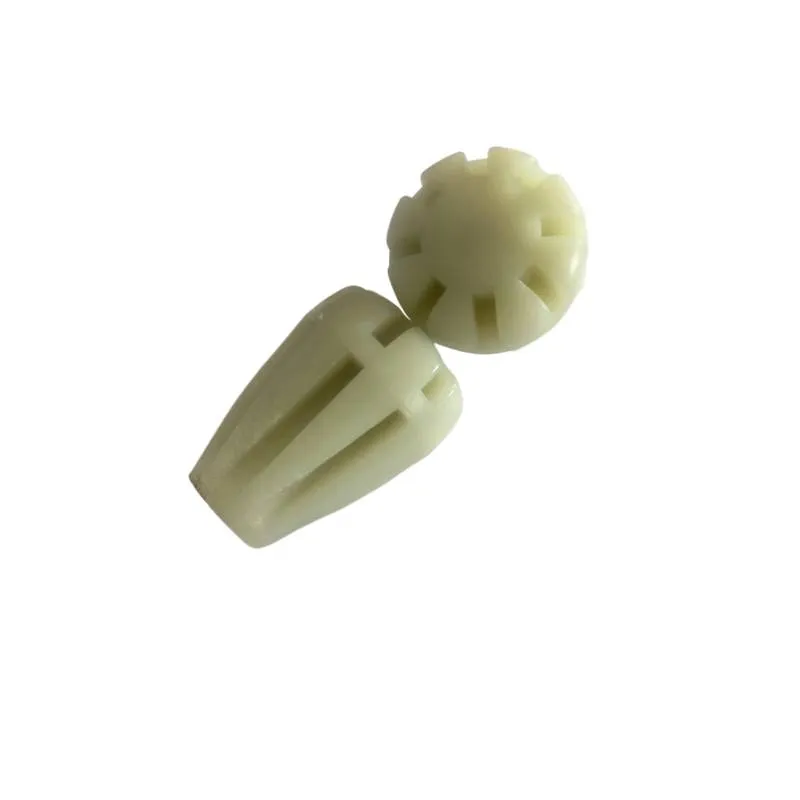
The expertise in selecting the right oil seal metal involves understanding the operational parameters of the machinery. For heavy industries like automotive, aerospace, and manufacturing, seals must withstand enormous stresses. An incorrect choice could lead to leaks, contamination, and ultimately, costly downtime. That is where experience and expertise come into play—understanding the nuances of each application's requirements is crucial.
Furthermore, the design of oil seal metals is vital. Modern engineering expects these seals to exhibit a seamless integration with the machinery, ensuring minimal friction and wear. Advanced manufacturing processes like precision forging and machining are employed to achieve the exact specifications needed for a perfect fit. The ability of these seals to maintain integrity over time without significant wear makes them indispensable in high-stakes industrial settings.
oil seal metal
The authoritativeness of a supplier in the oil seal metal market is often determined by the quality and reliability of their products. Reputable manufacturers invest heavily in research and development to innovate better sealing solutions. They aim to meet and exceed regulatory standards, providing clients with peace of mind regarding the seals' performance and safety. Certificates of compliance, along with rigorous quality checks, are routinely conducted to uphold these standards.
Trustworthiness is earned through consistent delivery of superior products and after-sales support. A trustworthy supplier will not only provide quality products but also offer expert advice, helping clients to identify the most suitable sealing solutions for their specific needs. This collaboration fosters a long-term relationship based on transparency and mutual respect. The provider’s ability to offer custom solutions and troubleshoot issues also significantly contributes to maintaining trust.
As industries evolve with the advent of new technologies and materials, staying updated with the latest advancements in oil seal metal technology is a strategic advantage. Professionals engaged in procurement and equipment maintenance are encouraged to regularly consult with their engineers and suppliers about the latest developments in sealing technology. This open channel of communication ensures that their operations remain efficient and competitive.
In an ever-crowded field, the key to standing out often lies in the commitment to excellence. Suppliers dedicated to refining their products and offering unparalleled customer service ultimately secure their position as industry leaders. Their dedication to quality and performance assurance is reflected in their oil seal metals, resulting in machinery that runs smoothly, enhances productivity, and reduces overheads.
By making informed decisions and choosing quality oil seal metals, companies ensure the continuous and reliable operation of their machinery. The proactive approach not only mitigates risks associated with seal failure but also optimizes operational costs over time. Therefore, integrating top-tier oil seal metals from a reputable and authoritative supplier is a strategic investment towards achieving operational excellence and sustainable success.