Mini press brakes have revolutionized the world of metal fabrication, offering unparalleled precision and efficiency to professionals and hobbyists alike. These compact machines bring the power of industrial-grade bending equipment into smaller workshops, enabling users to execute high-quality metal forming processes without the need for a full-scale press brake. Harnessing the benefits of advanced technology, mini press brakes are tailored to meet the needs of versatile and modern fabricators who demand performance and durability in their tools.

Modern fabrication shops prioritize space efficiency, and mini press brakes provide a perfect solution. Unlike their larger counterparts, these machines are designed to take up minimal space while delivering exceptional functionality. The compact size of mini press brakes does not compromise their versatility, as they can handle a variety of materials, including steel, aluminum, brass, and copper. This adaptability makes them an invaluable asset for those who require frequent changes in production tasks or materials.
One of the standout features of mini press brakes is their precision. Equipped with sophisticated control systems, these machines ensure accurate and consistent bending, which is crucial for high-quality metalworking projects. Digital readouts and programmable logic controls (PLCs) are common features that enhance precision and repeatability, resulting in reduced waste and improved production efficiency. This technological sophistication not only increases productivity but also minimizes the likelihood of human errors, thereby enhancing the overall quality of the output.
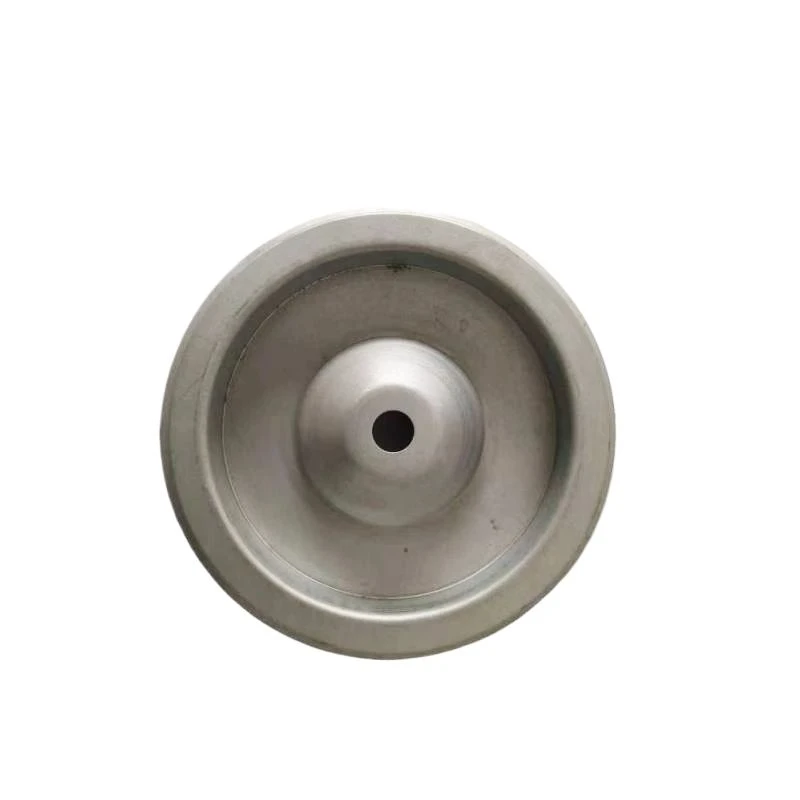
Safety is paramount in any workshop setting, and mini press brakes come equipped with various safety features to protect operators. These include safety guards, emergency stop buttons, and programmable safety controls that prevent accidents and ensure compliance with industry regulations. By incorporating advanced safety measures, mini press brakes foster a safer working environment, which is essential for maintaining high productivity levels.
The affordability of mini press brakes makes them accessible to a wider audience. Their cost-effectiveness does not mean they skimp on quality; these machines are built to withstand rigorous use while maintaining their performance over time. For small businesses and independent fabricators, investing in a mini press brake can significantly enhance their capabilities and open up new possibilities for complex metalworking projects without exceeding budget constraints.
mini press brake
From an operational standpoint, mini press brakes offer ease of use that appeals to users of all skill levels. With user-friendly interfaces and intuitive controls, operators can quickly learn how to execute various bends and forms, reducing the time spent on training and setup. This ease of use integrates smoothly into existing workflows, allowing fabricators to focus on creating quality products without unnecessary downtime.
The versatility of mini press brakes extends to their ability to perform complex operations, such as hemming, flanging, and box forming. These capabilities are essential for fabricators looking to create custom metal parts tailored to specific requirements. The flexibility of mini press brakes allows users to respond swiftly to changing market demands, giving them a competitive edge in the fast-paced world of metal fabrication.
Energy efficiency is another benefit that makes mini press brakes a compelling choice for environmentally conscious operations. By utilizing less power than traditional machines, they contribute to reduced operational costs and a lower environmental impact. This aspect is increasingly important in today's market, where sustainable practices are not only encouraged but often required by customers and industry standards.
Lastly, the evolution of mini press brakes continues to incorporate advanced technology, including automation and smart manufacturing solutions.
As the industry moves towards Industry 4.0, these machines are being designed to integrate seamlessly with other automated systems, providing real-time data monitoring and analysis. This integration enhances decision-making capabilities, allowing fabricators to optimize performance and elevate their production processes.
In conclusion, mini press brakes are an indispensable tool in modern metalworking. Combining precision, safety, affordability, and versatility, they provide an optimal solution for a wide range of fabrication needs. Whether for a small shop or a larger manufacturing environment, these machines empower users to achieve their bending goals with confidence and efficiency. As technology continues to advance, mini press brakes will undoubtedly keep pace, continually offering cutting-edge solutions that meet the evolving demands of the metal fabrication industry.