Metal washers are fundamental components in many mechanical assemblies, often overlooked but integral to ensuring the stability and longevity of various machinery and structures. These simple, yet versatile pieces of hardware serve to distribute load, prevent wear between uneven surfaces, and act as spacers or locking devices. The unsung heroes of construction and mechanical design, metal washers come in various shapes and sizes, each tailored to specific uses, bringing not only functionality but also reliability to their applications.
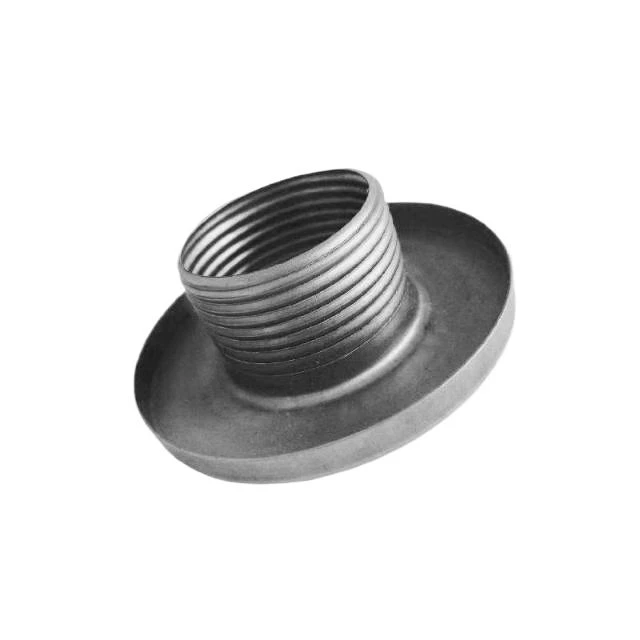
Drawing from years of hands-on experience, I have witnessed first-hand the significant role that quality metal washers play in maintaining structural integrity across diverse industries. A metal washer's material, thickness, and design can vastly influence an assembly's performance. Therefore, selecting the appropriate type becomes a task of utmost importance.
For instance, in high-temperature environments, stainless steel washers offer the excellent resistance needed to cope with thermal expansion. They stand resilient where lesser materials might falter. On the other hand, when corrosion resistance is a priority, washers made from galvanized metal or coated with anti-corrosive layers prove invaluable. Such specialized washers extend the life of the structures they support, reducing maintenance costs and time.
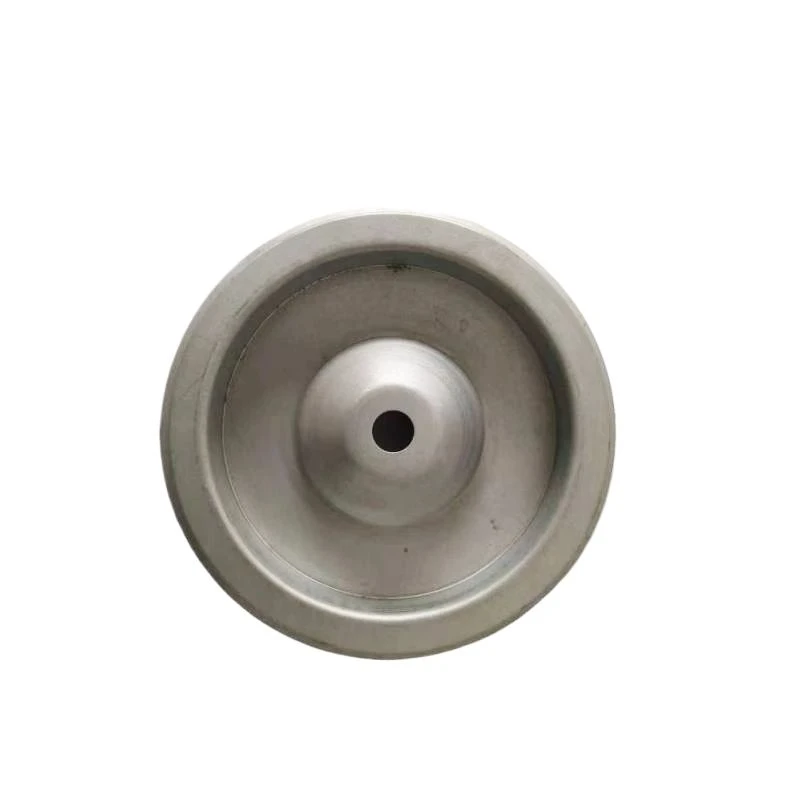
Beyond the material, the design of metal washers can significantly impact their efficacy.
Take lock washers, for example. Their unique construction applies tension to keep nuts and bolts securely tightened, a critical feature in applications subject to vibrations, such as automotive and aerospace industries. Here, even the smallest failure in fastener integrity can lead to catastrophic results, underscoring the washer's critical function in safety and reliability.
Expertise in washer application is not just about understanding their physical properties but also about knowing where and how to use them to achieve optimal performance. This requires not just technical knowledge, but a deep understanding of the mechanical processes where they are employed. It's an area where the experience meets science, guided by the principles of mechanical engineering and materials science.
metal washer
In discussing the authority of metal washers, one cannot overlook standards and certifications that govern their production and use. Compliance with these standards, such as ISO or ASTM specifications, ensures that washers meet stringent quality benchmarks. This adherence not only enhances their reliability but also reinforces trust amongst engineers and builders who rely on them for critical applications.
Various case studies highlight instances where the right choice of washer prevented equipment failure and saved substantial costs in repairs and downtime. One such account involves a manufacturing facility where regular equipment shutdowns were traced back to under-spec'd washers that wore quickly under load stress. By switching to heavy-duty spring washers that conformed to industry standards, they achieved a dramatic reduction in downtime, enhancing productivity and safety.
Trustworthiness in metal washers extends beyond their physical properties to the manufacturers who design and produce them. Reputable manufacturers conduct rigorous testing and quality assurance processes, often exceeding baseline industry requirements to offer products that can be trusted to perform under the most demanding conditions.
In conclusion, metal washers may appear as modest components within a mechanical assembly, but their influence on overall performance and safety is profound. Selecting the right washer requires a blend of expertise, experience, and attention to quality standards, ensuring long-term reliability and efficiency. When approached with the careful consideration they deserve, metal washers become pivotal in constructing a safer, more efficient mechanical world.