Metal stamping washers are an integral component in various industries, underpinning everything from automotive to aerospace applications. Their role cannot be understated, as they contribute to the efficiency, safety, and durability of countless mechanical systems. The uniqueness of these components lies in their production method—metal stamping, which offers a level of precision and uniformity that other manufacturing processes struggle to match.
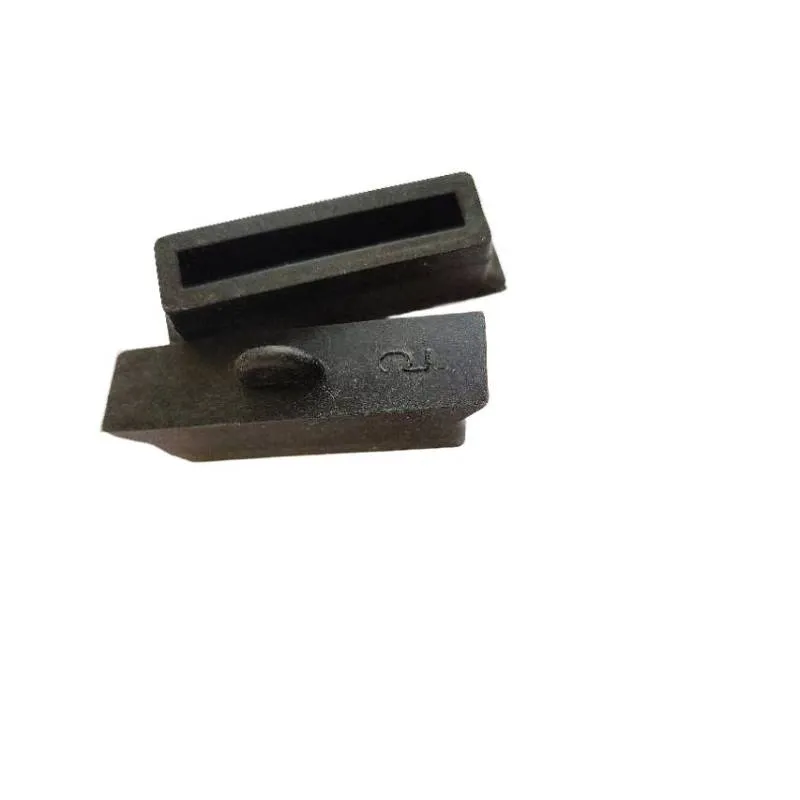
The demand for custom washers is at an all-time high, largely due to the rapid advancements in industrial technology. As industries evolve, so do their requirements for more durable and precise components.
Metal stamping washers meet these needs effectively by offering extreme versatility. They can be tailored to suit specific material properties, thicknesses, and dimensional requirements, making them a go-to solution for various applications.
One of the key strengths of metal stamping is its ability to produce washers in large volumes without sacrificing quality. This process involves cutting and forming metal sheets into predetermined shapes using a die, which enforces consistency across thousands of units. As a result, manufacturers can maintain high standards while managing costs, an aspect highly valued by industries that require bulk components.
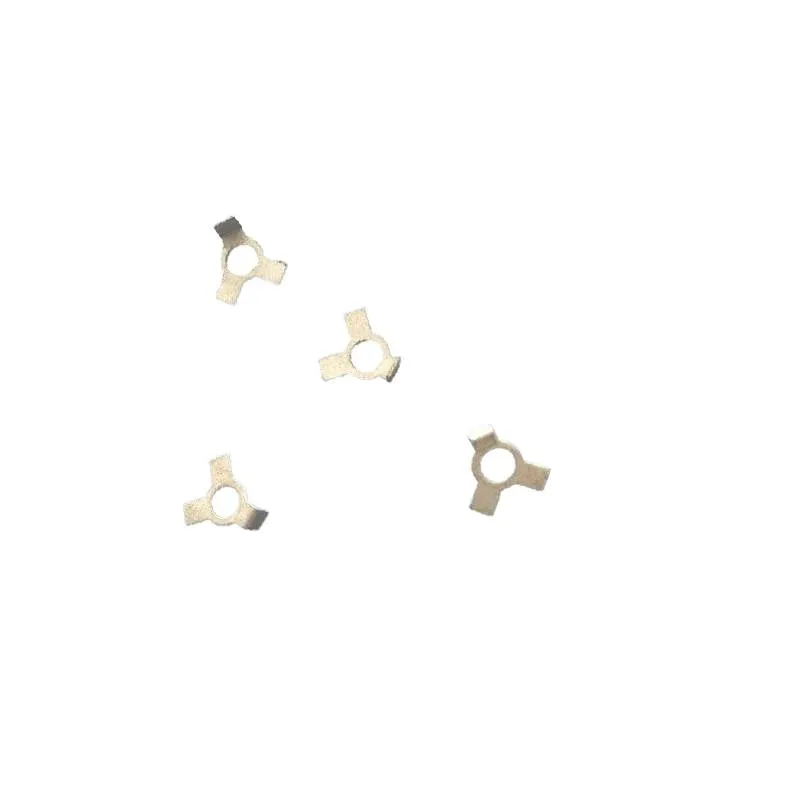
Moreover, the expertise involved in the design and manufacturing of metal stamping washers cannot be overstated. Specialists in this field draw from a deep well of engineering knowledge, ensuring that each washer not only meets, but exceeds specific application requirements. From the selection of materials—be it carbon steel, stainless steel, aluminum, or exotic alloys—to the intricate details of the stamping process itself, every stage is meticulously planned and executed.
A vital aspect of the manufacturing process is material choice, which heavily influences the washer's performance and longevity. For instance, stainless steel washers are renowned for their resistance to corrosion and high thermal stability, making them ideal for harsh environments or applications with significant temperature fluctuations. Alternatively, aluminum washers offer excellent conductivity and are significantly lighter, beneficial for the aerospace industry where weight is a critical factor.
metal stamping washers
In an industry where precision is paramount, the dimensional accuracy of stamped washers is a standout feature. Through computer-aided design (CAD) and computer-aided manufacturing (CAM) technologies, producers achieve precise specifications and tight tolerances. This precision is essential, as even minimal deviations can lead to significant mechanical failures, especially in applications where washers distribute load or reduce vibrations.
The authenticity and reliability of metal stamping washers are further underscored by stringent quality control measures. Manufacturers deploy advanced testing techniques, such as finite element analysis (FEA) and non-destructive testing, to verify the structural integrity and functionality of each washer. These practices not only ensure compliance with industry standards but also foster trust and reliability among end-users.
Trustworthiness in this domain is reinforced by manufacturers’ dedication to eco-friendly practices. Many have adopted sustainable production methods, utilizing recycled materials, reducing waste, and minimizing energy usage. These efforts align with global sustainability goals and demonstrate a commitment to responsible manufacturing, adding a layer of credibility and environmental stewardship to their operations.
The authority of metal stamping washer manufacturers is also evident through their collaborative approaches to innovation. They frequently work alongside clients to develop bespoke solutions, leveraging their extensive knowledge to solve unique challenges. This level of collaboration not only strengthens industry ties but also helps drive technological advancement, ensuring that metal stamping washers remain at the forefront of industrial needs.
In conclusion, metal stamping washers are more than mere components; they are the backbone of numerous mechanical systems. Their production involves a harmonious blend of expertise, precision, and innovative practices, ensuring that they meet the diverse demands of modern industries. Through a commitment to quality, environmental responsibility, and continual innovation, these washers will continue to be a critical element in the machinery of progress.