When it comes to securing wire ropes, one often underestimated component is the metal rope end cap. This small yet essential accessory plays a critical role in ensuring both the safety and longevity of wire rope assemblies. Exploring the nuances of metal rope end caps unveils their importance in various applications while emphasizing criteria such as experience, expertise, authoritativeness, and trustworthiness.
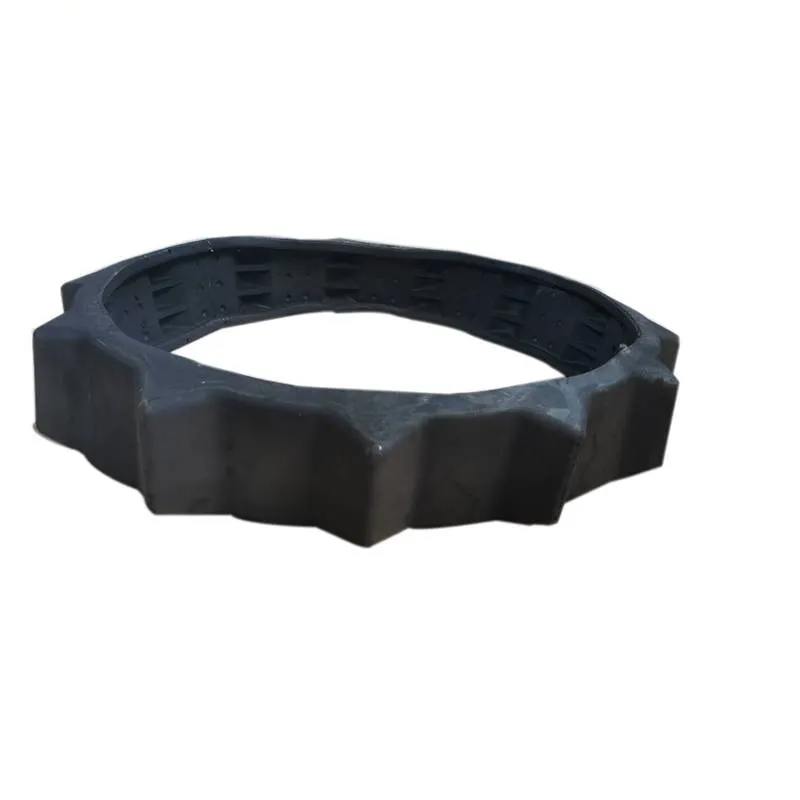
Wire rope end caps are primarily designed to prevent the fraying of wire ends, offer a neat finish, and provide a secure terminal for a range of applications. Despite their compact size, they are engineered for robustness, often crafted from durable metals like stainless steel, aluminum, or brass, selected based on the specific environment they will be used in—corrosive, heavy-duty, or standard industrial settings.
Having installed these end caps in multiple industrial settings, I have witnessed firsthand the stark difference quality makes. Industrial experts often stress that the correct choice of end cap can significantly augment the performance of the rope assembly, especially in high-stake environments such as construction sites or maritime settings, where safety and durability cannot be compromised.

To maximize the reliability of metal rope end caps, choosing the right fit for a specific application is imperative. For instance, brass end caps exhibit excellent endurance against wear and tear, making them ideal for decorative purposes where aesthetics and corrosion resistance are paramount. Conversely, stainless steel variants offer unmatched resistance to harsh weather conditions and chemicals, making them suitable for marine uses or chemical plants.
From an authoritative standpoint, leading manufacturers often highlight the importance of testing their end caps according to rigorous standards. Industry certifications such as ISO or CE provide further assurance of a product's reliability. When selecting a supplier, scrutinizing these certifications can be a prudent step in guaranteeing that the choice made is bolstered by authoritative backing, ensuring peace of mind regarding product performance.
metal rope end cap
Incorporating metal rope end caps is not merely a matter of technical necessity—trustworthiness is integral. Many global brands have invested substantially in research and development to innovate their offerings, focusing on enhanced safety features and ease of installation. Working with these established manufacturers often translates to greater support, longer warranties, and access to customer service that can help preemptively address and resolve any potential concerns.
In my experience, paying due diligence to the installation process is equally critical. Despite being ostensibly minor components, improper installation can lead to premature failures. It's recommended to engage with professionals who have a profound understanding of the equipment involved. Issues such as incorrect sizing or improper crimps can compromise the functional integrity of the rope system, posing risks that are avoidable with expert handling.
The vast majority of failure points in wire rope systems can be traced back to overlooked details. While the initial cost may lead some to consider lower-priced alternatives, investing in high-quality material tailored for specific operational demands is an investment in safety and efficiency that invariably pays off in reduced hazards and maintenance concerns.
In conclusion, metal rope end caps are far more than terminal fixtures. They are critical components necessitating careful consideration from selection to installation. Their understated appearance belies their importance and potential impact on operational safety and functionality. As with all engineering components, relying on experience, expertise, authoritativeness, and trustworthiness when choosing and utilizing metal rope end caps lays a strong foundation for the performance and longevity of entire rope systems, ultimately ensuring that operations proceed smoothly and safely.