Understanding Metal Parts Pricing A Comprehensive Guide for Buyers and Suppliers
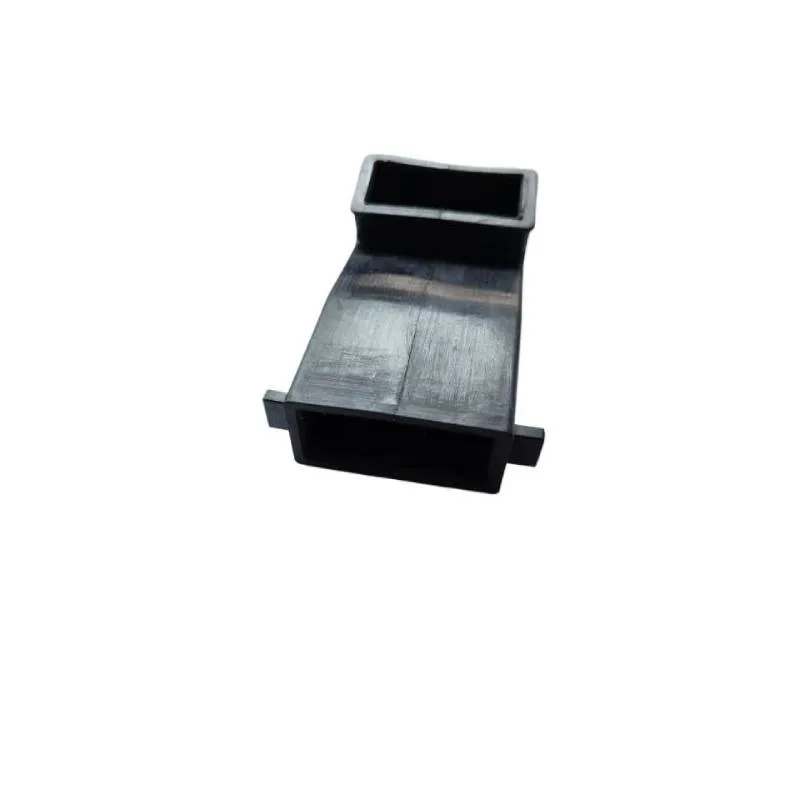
Navigating the world of metal parts pricing can be a complex venture, driven by a wide array of factors that suppliers and buyers must meticulously consider. The intricate balance of material costs, manufacturing processes, and market demand significantly influences pricing structures. Yet, understanding these elements not only aids in better forecasting but also strengthens negotiating positions and strategic decision-making. This guide delves into the key components shaping metal parts pricing, offering insights drawn from both industry expertise and practical experience.
Material Cost The Foundation of Pricing
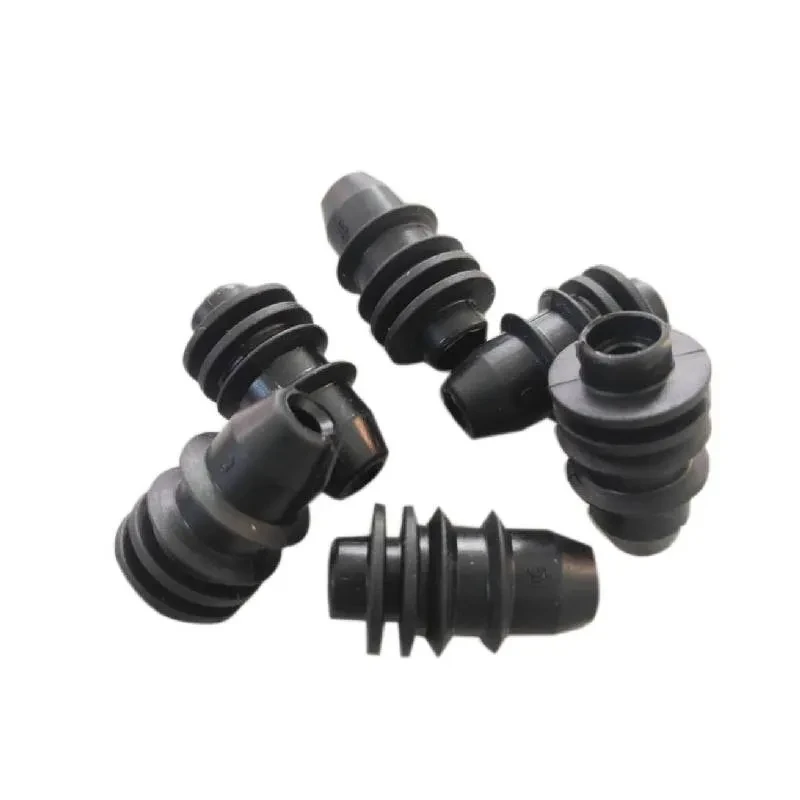
One of the primary determinants of metal parts pricing is the cost of raw materials. Metals such as steel, aluminum, brass, and titanium are traded commodities, subject to global economic conditions, geopolitical factors, and supply chain dynamics. Suppliers must continuously monitor market trends to purchase materials at the most advantageous prices. Buyers, on the other hand, should be aware of these fluctuations to time their purchases strategically.
For example, fluctuations in steel prices can dramatically affect the cost of components used in sectors like automotive and construction. Industries reliant on aluminum face similar challenges, especially with the increasing demand for lightweight materials. Historical data and predictive analytics are invaluable tools for both suppliers and buyers to manage this volatility.
Manufacturing Processes Precision and Cost Efficiency
The complexity and precision required in manufacturing processes also play critical roles in pricing metal parts. Techniques such as casting, forging, machining, and additive manufacturing (3D printing) each come with varying cost structures.
Casting and forging are generally more cost-effective for large volume orders due to lower material waste and faster cycle times. However, for intricate parts requiring high precision, CNC machining might be more appropriate despite its higher operational costs. Understanding the strengths and limitations of each process can help in selecting the most cost-effective method without compromising on quality.
Moreover, advanced manufacturing technologies such as automation and AI have been integrated into production lines to enhance efficiency and reduce costs. Suppliers offering these high-tech solutions often provide competitive pricing due to streamlined operations and reduced labor expenses.
Quality Assurance The Impact on Pricing
Quality assurance processes are paramount in the production of metal parts, directly affecting the final pricing. Rigorous quality checks, compliance with international standards, and certifications such as ISO can increase production costs. However, they also assure buyers of the reliability and durability of products, which is critical in sectors like aerospace and medical devices.
metal parts price
Investing in quality assurance not only enhances the credibility of suppliers but also attracts premium clients willing to pay for superior products. Buyers should evaluate the quality certifications and past performance records of suppliers to ensure they are getting value for money.
Market Demand and Supply Considerations
Like any other industry, the law of supply and demand greatly influences the pricing of metal parts. High market demand for specific metal components can drive prices up, especially if supply chains are disrupted. Recent global events have highlighted the fragility of supply chains, underscoring the importance of diversification and strategic sourcing.
Suppliers must remain agile, capable of adjusting production volumes and sourcing from alternate suppliers as market demands shift. Buyers should foster strong relationships with their suppliers to gain preferential pricing and ensure consistent supply during high-demand periods.
Sustainability in Pricing Strategy
Sustainability is increasingly shaping pricing strategies in the metal parts industry.
As environmental concerns rise, both buyers and suppliers are prioritizing eco-friendly practices. Recycled materials and energy-efficient manufacturing processes may initially raise costs but often lead to long-term savings and less volatility in material supply.
Suppliers integrating sustainable practices into their operations can capitalize on this growing market trend, attracting eco-conscious buyers willing to invest in sustainable products. Buyers, too, should recognize the value in sustainability, often reflected in the total lifecycle cost and reduced regulatory risks.
Conclusion Strategic Insight for Competitive Advantage
Metal parts pricing is influenced by a multitude of factors, ranging from raw material costs to manufacturing processes and market demand. Both suppliers and buyers must adopt a strategic approach to navigate these complexities successfully. By understanding the dynamics at play and leveraging real-world data and industry expertise, stakeholders can secure not only competitive pricing but also ensure high-quality, reliable sourcing of metal components.
Staying informed about market trends, technological advances, and regulatory changes is crucial for maintaining a competitive edge. As the industry evolves, those who can adeptly balance cost efficiency with quality and sustainability considerations will thrive in the ever-dynamic global marketplace.