The manufacturing of metal parts stands as one of the most pivotal components in a multitude of industries, from automotive to aerospace, and even to the delicate intricacies of medical devices. Behind every efficient engine, robust machinery, and precise surgical tool, lies a complex process of metal parts manufacturing, an intricate world driven by technology, expertise, and meticulous craftsmanship.
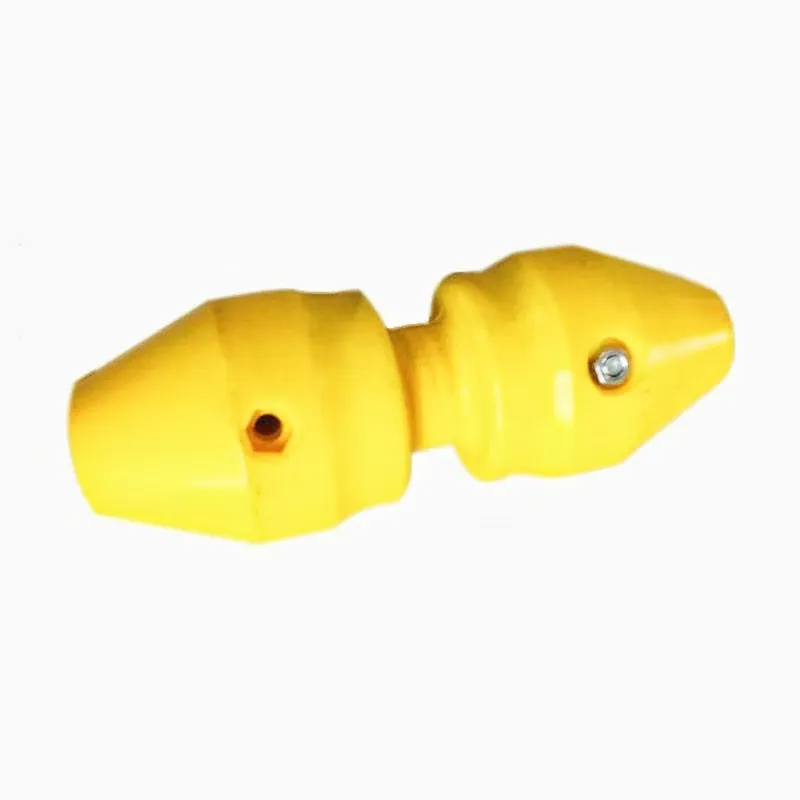
A profound understanding of the metal parts manufacturing process begins with grasping its foundational methods casting, forging, machining, and additive manufacturing. Each of these processes offers unique advantages and challenges, making the choice heavily dependent on the specific applications and desired properties of the final product.
Casting is one of the oldest methods of metal forming, where metal is melted, poured into a mold, and allowed to cool and solidify. This process is particularly beneficial for creating complex shapes that would be difficult or expensive to achieve with other methods. With advancements in technology, precision casting has undergone significant enhancements, allowing for higher dimensional accuracy and smoother surface finishes, which are crucial in high-performance sectors like aerospace.
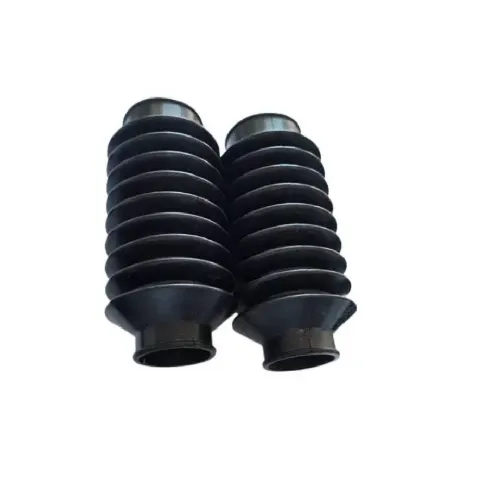
Forging, on the other hand, involves shaping metal using compressive forces. This method improves the mechanical properties of metal parts, such as strength and durability, due to the alignment of the metal's internal grain structure. Forging is predominantly used in the production of components that must withstand high stress and demand, such as bolts, gears, and shafts. The advent of computer-controlled processes has further enhanced the precision and consistency of forged parts, elevating their usability across various sophisticated engineering applications.
Machining is a subtractive process where metal is removed from a workpiece to shape the final product. With the current advancements in CNC (Computer Numerical Control) machining, metal parts can be produced with unmatched precision and efficiency. This is particularly important in the medical device industry, where exact specifications are paramount to ensure safety and functionality.
Additive manufacturing, commonly known as 3D printing, has revolutionized the metal parts manufacturing landscape in recent years. This method builds parts layer by layer, offering unparalleled flexibility in design and the ability to create complex geometries that were once impossible to produce. The customization capabilities of additive manufacturing make it invaluable for prototyping and small batch production, where traditional methods might face significant cost constraints.
metal parts manufacturing
The expertise in metal parts manufacturing lies not only in the understanding of these processes but also in material selection. Various metals and alloys, including steel, aluminum, titanium, and nickel-based superalloys, bring forward different properties - from corrosion resistance to high strength-to-weight ratios. The selection process is critical and depends largely on the application requirements, operating environments, and compatibility with other materials used in assembly.
An authoritative approach in this field requires a deep commitment to quality control and testing, ensuring each part meets strict standards and specifications. Techniques such as non-destructive testing (NDT), metallurgical analysis, and fatigue testing are standard practices employed by manufacturers to verify the integrity and performance of metal parts.
Trustworthiness, an indispensable pillar in metal parts manufacturing, is founded on transparency and adherence to industry standards and certifications. Adopting practices such as ISO 9001 for quality management systems, and AS9100 or IATF 16949 for aerospace and automotive sectors respectively, reassures clients and stakeholders of the manufacturer’s commitment to maintaining high-quality processes.
Moreover, sustainability in manufacturing processes has gained significant traction, urging manufacturers to adopt practices that minimize waste, reduce energy consumption, and promote recycling.
In the metal parts industry, this involves innovative approaches such as remanufacturing and the use of eco-friendly production techniques.
As a seasoned professional in this domain, prioritizing continuous improvement and innovation forms the backbone of success in metal parts manufacturing. Embracing digitalization, like the Internet of Things (IoT) for monitoring production in real-time, can significantly enhance efficiency and reduce downtime, thus strengthening the competitiveness of manufacturing enterprises.
In conclusion, metal parts manufacturing is an ever-evolving field, driven by technological advancements and the necessity for precision and reliability. By integrating knowledge, cutting-edge technology, and a commitment to quality and sustainability, manufacturers not only meet current demands but also shape the future of manufacturing industry standards.