Metal-on-metal seals represent a pinnacle of engineering precision and durability in high-performance industries. These seals are essential in various applications where traditional materials might fail due to extreme conditions. Here, we delve into the unique characteristics, applications, and benefits that place metal-on-metal seals at the forefront of sealing technology.
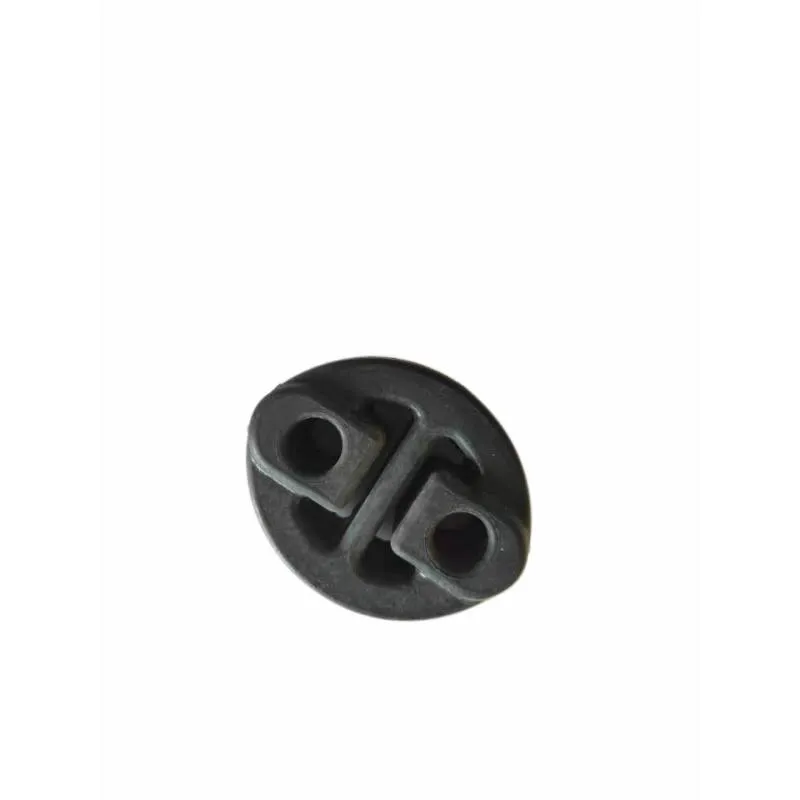
Metal-on-metal seals are constructed using high-grade metals such as stainless steel, Inconel, or titanium. These materials provide exceptional resistance to high temperatures, pressures, and corrosive environments, making them ideal for industries such as aerospace, oil and gas, and power generation. Unlike traditional rubber or polymer seals, metal-on-metal configurations maintain integrity in environments ranging from cryogenic to extreme heat scenarios, offering unparalleled longevity and performance.
One of the key benefits of metal-on-metal seals is their ability to withstand thermal expansion and contraction without losing their sealing capability. This characteristic is critical in applications such as jet engines and gas turbines, where temperature fluctuations are frequent and severe. Engineers value the reliability of these seals, which translates to fewer maintenance requirements and reduced operational downtime.
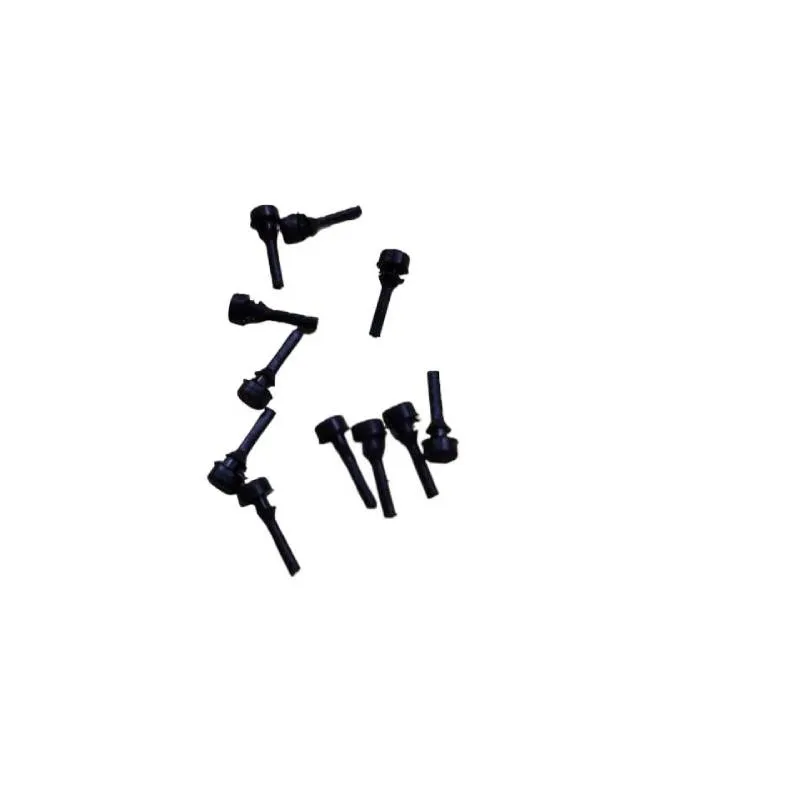
In addition to temperature resilience,
metal-on-metal seals excel in high-pressure situations. In subsea oil extraction, for instance, seals are subjected to immense pressure. Metal-on-metal designs provide the necessary robustness to prevent leaks that could lead to catastrophic failures or environmental disasters. Their precision-engineered surfaces ensure a tight fit and consistent performance, even under variable pressures.
The expertise in manufacturing metal-on-metal seals is reflected in rigorous testing standards that ensure compliance with the strictest industry regulations. Organizations looking to employ these seals can trust in their certified quality, often verified by industry-specific bodies. This level of assurance is crucial for industries where failures can have severe safety implications.
metal on metal seal
Furthermore, the advancements in metal-on-metal sealing technology are evident in the customization options available. Engineers can work closely with manufacturers to tailor seals to specific application needs, selecting the appropriate metal alloys and surface finishes to optimize performance. This customization extends the seal's life, improves efficiency, and enhances overall system reliability.
Product development in the metal-on-metal seal industry continues to evolve with innovations designed to increase environmental compatibility. Eco-friendly coatings that enhance corrosion resistance without toxic byproducts are examples of how the industry addresses environmental concerns while maintaining performance standards.
Metal-on-metal seals are backed by a wealth of real-world data and case studies that demonstrate their effectiveness across various critical applications. Companies can leverage these insights to make informed decisions when implementing sealing solutions. Consulting with industry experts provides access to this extensive knowledge base, ensuring that metal-on-metal seals are utilized to their fullest potential.
In terms of trustworthiness, partnering with reputable manufacturers ensures that seals meet or exceed the operational criteria specified by their intended applications. Reputable suppliers provide thorough documentation and support, fostering confidence in the reliability of metal-on-metal seals.
Engineers and decision-makers looking to invest in metal-on-metal sealing technology benefit from a material that has been refined through decades of research and development. The expertise involved in their construction is matched by the authority of applications success stories across industries. Metal-on-metal seals consistently prove to be the optimal choice for scenarios where performance cannot be compromised, establishing their place as a reliable and effective solution for modern engineering challenges.