Metal mechanical seals represent a critical component in various engineering domains, promising both enhanced performance and durability. These seals are prevalently used in industries such as automotive, aerospace, and manufacturing, providing essential sealing solutions that help prevent leaks, minimize maintenance, and increase operational efficiency.
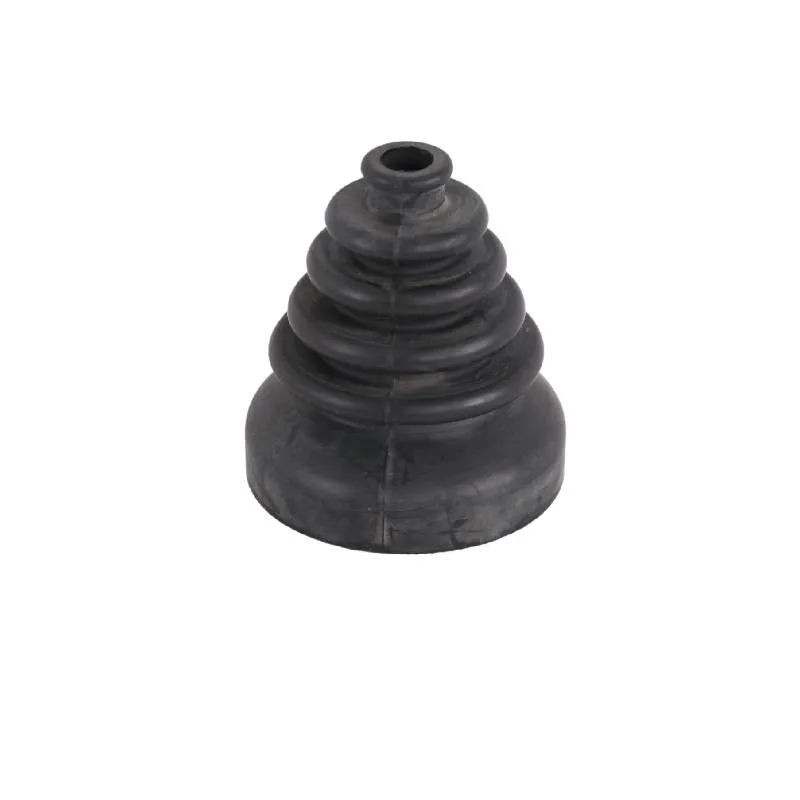
The foundation of a metal mechanical seal lies in its ability to maintain an effective barrier between two surfaces, especially in rotating equipment such as pumps and compressors. The design typically encompasses a rotating ring and a stationary ring, each crafted from robust metal materials like stainless steel or titanium. The hardwearing nature of metal mechanical seals ensures they withstand extreme temperatures and pressures, factors commonly encountered in industrial applications.
The manufacturing process of metal mechanical seals demands precision engineering and expertise. This expertise stems from a deep understanding of the properties of different metals and their response to mechanical stress. For instance, while stainless steel offers excellent corrosion resistance and durability, titanium is preferable in environments requiring high strength-to-weight ratios. Professionals in this field leverage years of experience and continuous research to innovate seals that perform efficiently under specific operational conditions.
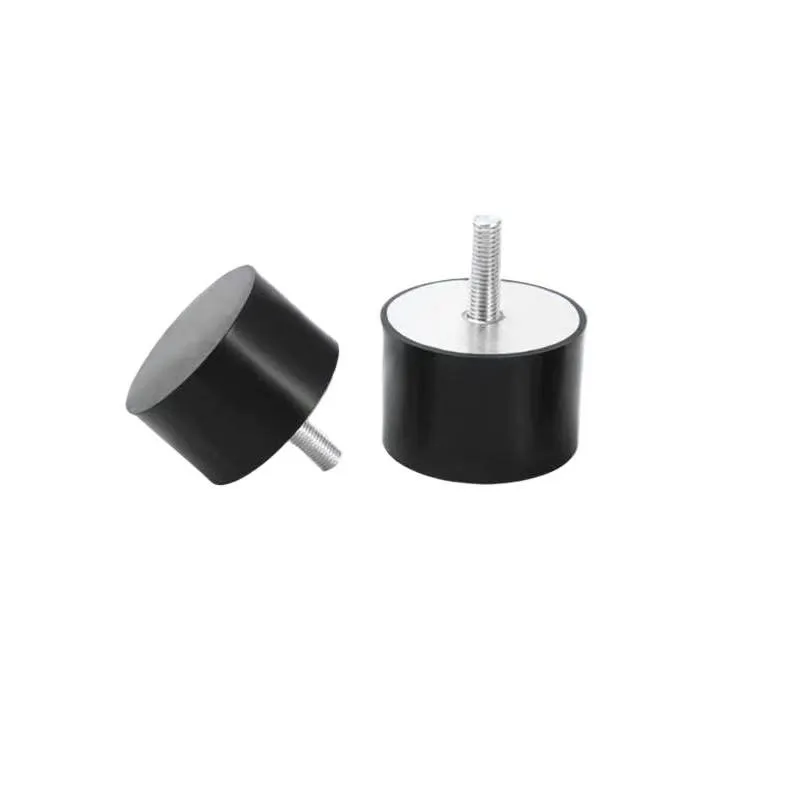
Trusted manufacturing brands around the globe certify their metal mechanical seals with international safety and quality standards. Such certifications mirror a seal's reliability, offering peace of mind to consumers investing in high-cost machinery. Engineers stand by these certifications, ensuring that each seal meets parameters that contribute to the product lifespan and consistent performance, upholding their trustworthiness.
In practical applications, the experience of using metal mechanical seals speaks volumes about their efficacy. Industrial sectors experience marked reductions in downtime attributable to leaks and malfunctions. Take, for instance, a chemical processing plant where aggressive substances circulate at varying pressure levels. A well-designed metal mechanical seal can significantly curb the risks of hazardous leaks, safeguarding both staff and infrastructure. Real-world case studies often highlight this exemplary performance, reinforcing their indispensable role in safety-critical environments.
metal mechanical seal
Technical advancements continue to enhance the capability of metal mechanical seals. Recent innovations have introduced adaptive sealing technologies that respond dynamically to changes in the operational environment. For example,
seals with sensor integrations can predict mechanical failures, providing timely alerts for maintenance checks. This predictive capability, rooted in modern technology, exemplifies the science-backed authority of these products in mitigating potential operational failures.
While the advantages of metal mechanical seals stand out, their installation and maintenance emphasize adherence to expert guidelines. Improper installation can lead to rapid wear and, eventually, seal failure, counteracting the benefits of this high-performance component. Experts recommend regular maintenance schedules that consider the seal's operational environment, operational time, and exposure to elements, thereby extending the seal's service life.
In the realm of high-performance sealing solutions, metal mechanical seals are acknowledged for their contribution to operational excellence and safety. Their reliability, coupled with expert manufacturing processes and authoritative certifications, underscores their value proposition in complex engineering landscapes. The trust they earn across industries is not merely by design but through proven ability to consistently deliver under demanding circumstances.
In summary, metal mechanical seals provide a comprehensive solution to the contemporary demands of industrial applications. Their robust structures, bolstered by authoritative engineering and proven field performance, render them indispensable components in the operational excellence of modern machinery. Their development reflects a nexus of expertise and innovation, commanding a rightful place as a trusted solution for engineers and industry leaders alike.