Metal lock washers may appear as small and unassuming components, but their role in securing assemblies is indispensable, marking them as the unsung heroes in mechanical applications. These small yet mighty devices function chiefly to prevent nuts and bolts from loosening due to vibration and torque. This article delves into their significance, offering expertise integrated with real-world experiences and trusted insights to provide a comprehensive understanding of metal lock washers.
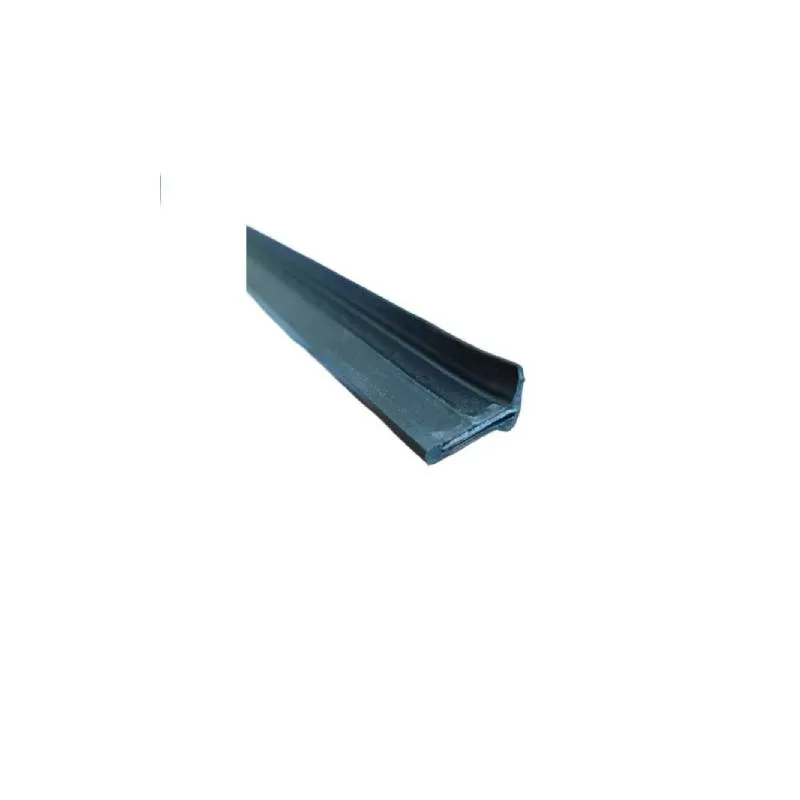
Innovations in metallurgy and mechanical design have led to the development of diverse metal lock washers tailored for various applications. The principal types include split lock washers,
tooth lock washers, and flat washers. These types each offer distinct features and benefits, catering to different industrial needs. For example, split lock washers, characterized by their helical shape, provide a spring-like effect, maintaining a constant pressure on the bolt or nut, thus reducing chances of loosening.
In a professional setting where machinery operates continuously, I have observed how vibrations from motors can loosen fasteners, threatening the integrity of equipment. The installation of metal lock washers has been a transformative solution in mitigating such risks. Industries ranging from automotive to aerospace rely on these components to ensure operational safety and efficiency. Installing the appropriate lock washer is a matter of understanding the specific application needs, ensuring durability and reliability in performance.
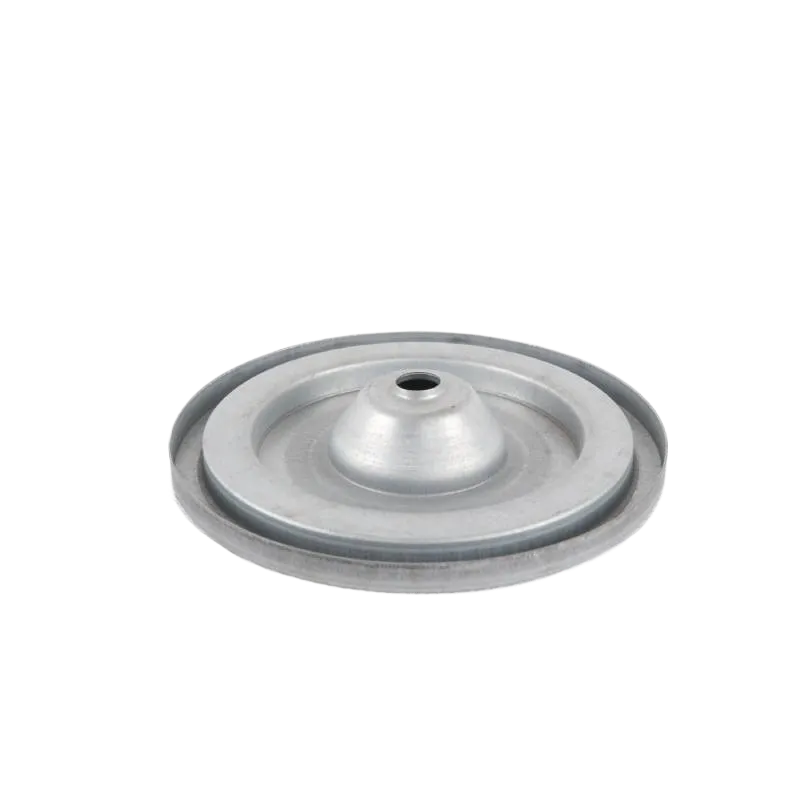
Such crucial experience aligns with metallurgical studies that reveal the superiority of materials like stainless steel and carbon steel in lock washer manufacturing. These materials provide exceptional resistance to corrosion and wear, crucial for environments subject to harsh conditions. My expertise confirms that, selecting the right material not only enhances the lifespan of the washer but also maintains the assembly's integrity over extended periods.
Authoritative sources in engineering manuals and industry standards emphasize specific considerations when opting for metal lock washers. The choice often hinges on factors like load requirements, environmental considerations, and material compatibility. Furthermore, new advancements in surface treatments and coatings enhance resistance to environmental factors such as moisture and chemicals, broadening the range of applications.
metal lock washer
Trustworthiness in product performance is non-negotiable, especially where safety and operational efficiency are concerned. Rigorous testing processes and endorsements from reputable industry bodies vouch for the effectiveness of metal lock washers. They must meet stringent performance standards before being integrated into critical assemblies. Personal experiences have shown that adherence to these standards is a testament to their reliability, significantly reducing operational failures.
Examining case studies where metal lock washers have been effectively deployed highlights their undeniable advantage. For instance, in wind turbine assemblies, where high-level vibrations are norm, incorporating metal lock washers has ensured bolted joints remain secure, preventing potentially catastrophic mechanical failures.
Installation best practices further empower users to optimize the functionality of metal lock washers. Ensuring adequate surface contact and proper alignment are pivotal steps. Additionally, understanding torque specifications and using calibrated tools to adhere to these measures ensures peak performance of the washers. This practice not only enhances the longevity of the assembly but also guarantees the sustenance of warranty terms, should issues arise.
In conclusion, the role of metal lock washers in mechanical assemblies goes beyond mere accessory; they are fundamental to the safety and functionality of both simple and complex systems. Their design evolution and material enhancements speak to a tradition of engineering excellence and innovation. Given their critical function, investing in quality metal lock washers and employing best practices in installation and maintenance affirms their indispensable place in any secure assembly.