Metal face seals, often referred to as mechanical face seals or heavy-duty seals, are critical components in various industrial and automotive applications. These robust seals are indispensable in environments where equipment must withstand extreme conditions, such as abrasive, corrosive, or high-pressure scenarios. Below is an exploration of metal face seals, focusing on their real-world applications, expert insights on best practices for their use, and how their quality and reliability establish trustworthiness in industries worldwide.
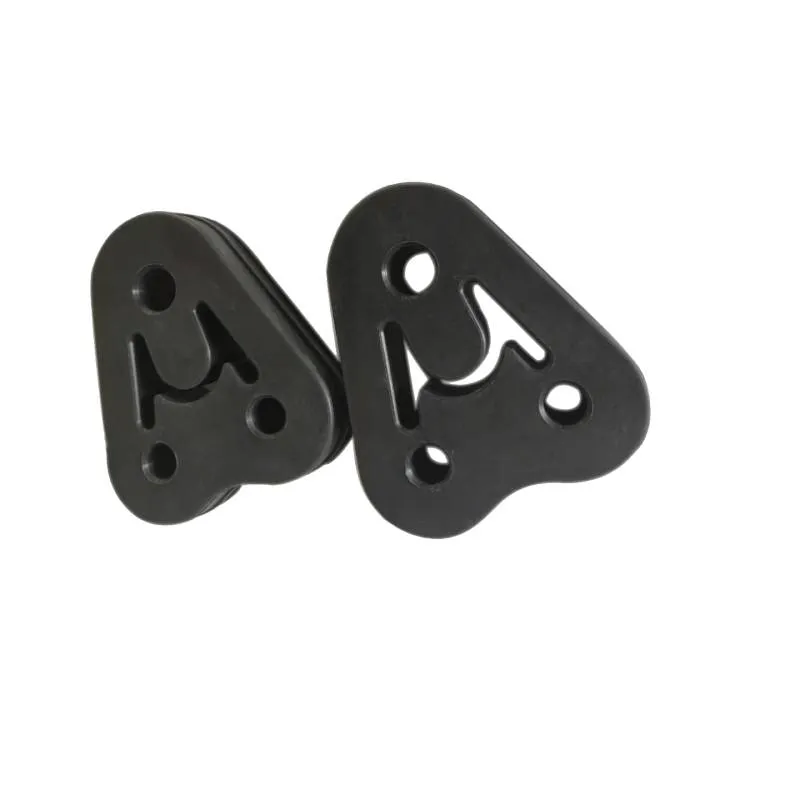
Metal face seals are predominantly used in equipment that is subjected to harsh operational conditions. Mining and construction machinery, agricultural equipment, as well as heavy-duty vehicles like bulldozers and excavators, rely heavily on these seals. Their primary function is to protect critical components such as bearings, gears, and shafts from contamination by dust, dirt, and moisture, which could otherwise lead to premature wear and equipment failure.
The design of metal face seals is a testament to engineering precision. Typically comprising two identical metal rings and two resilient toric elastomer load rings, these seals work by creating a tight, lubricated barrier in rotary applications and machinery components. The metallic rings are precision-lapped with an extremely smooth surface finish. This design ensures a dynamic sealing interface with minimal wear, a factor that contributes to their durability in adverse conditions. The load rings, usually made from superior-grade elastomers, maintain contact pressure between the metal rings under varying thermal and mechanical stresses.
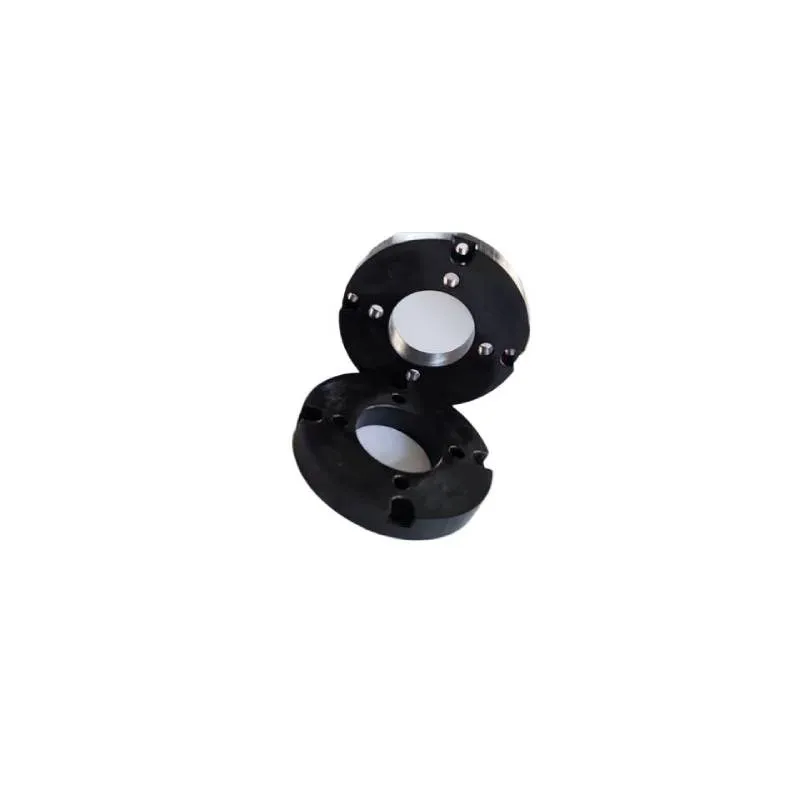
Expertise in selecting the right metal face seal involves understanding the specific operational environment and mechanical demands. It is crucial to consider factors such as temperature ranges, rotational speeds, and exposure to specific chemicals or abrasives. Some metal face seals are manufactured with custom alloys to enhance their resistance to corrosive agents, thereby extending their lifespan in chemically aggressive environments. An expert understanding of metallurgical properties and elastomer compatibilities is essential when choosing seals, as even small deviations can compromise the integrity and performance of the seal in critical operations.
metal face seals
One example of their application can be drawn from the mining sector, where metal face seals are subjected to continuous exposure to rock fragments, mud, and slurry. Experience has shown that regular inspections and scheduled maintenance significantly enhance the lifespan of seals in such rigorous settings. Preventive maintenance strategies, including proper lubrication and routine checks for wear and tear, are vital. These practices, born from decades of industrial expertise, highlight the importance of not only selecting the right seal but maintaining it adequately to ensure optimal performance.
The authoritativeness of metal face seal manufacturers plays a pivotal role in this niche market. Industry leaders often invest heavily in R&D to innovate designs that push the boundaries of longevity and reliability. Certifications, compliance with international standards, and collaboration with OEMs (Original Equipment Manufacturers) further verify their commitment to quality. Trustworthiness is built through decades of proven field performance, a factor that procurement managers and engineers consider indispensable when selecting components for high-stake environments.
In conclusion, metal face seals are an engineering marvel that combine design precision, material science, and reliability. Experience in their application demonstrates their indispensable role in protecting heavy machinery components from operational hazards. Expertise in their selection and maintenance ensures efficiency and longevity, while authoritative manufacturers reinforce trust through continuous innovation and commitment to quality standards. Through the synthesis of experience, expertise, authoritativeness, and trustworthiness, metal face seals continue to be a cornerstone component in industries that demand the highest levels of reliability and performance.