Navigating the world of electrical installation, professionals often encounter terminologies and components crucial for project success. Among these, the metal conduit end cap is an essential part that cannot be overlooked. Understanding its unique qualities and applications ensures the integrity and safety of any wiring system.
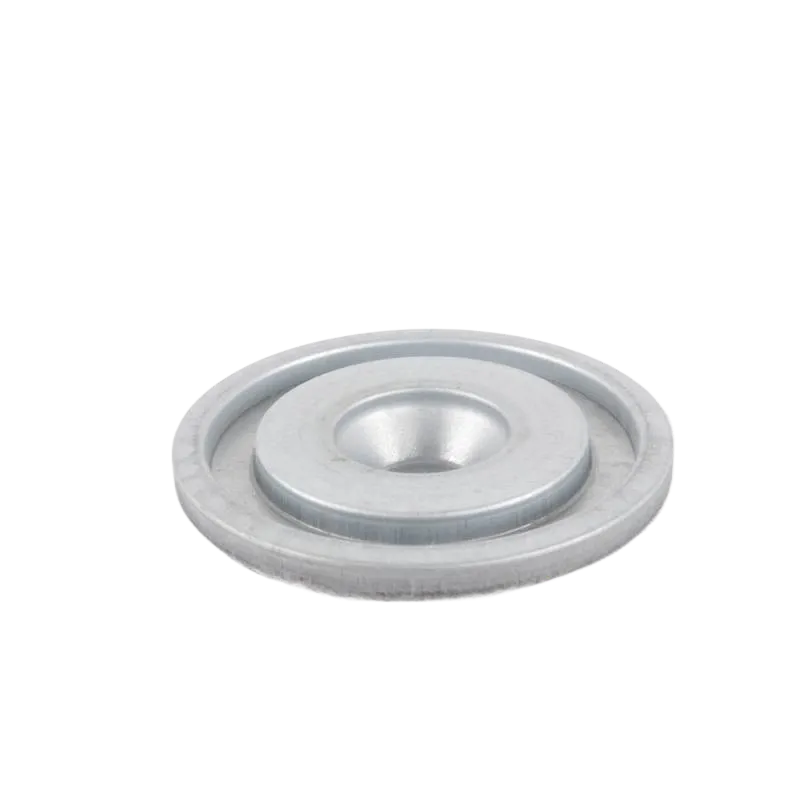
Metal conduit end caps serve a pivotal role in electrical installations. These components, typically made from robust materials such as aluminum, stainless steel, or zinc-plated steel, are designed to fit over the open ends of conduits, providing a tidy closure. Their primary function is to protect the interior of the conduit from dirt, moisture, and physical impacts that may compromise the electrical wiring within. By sealing off these open ends, end caps prevent damage to the wires that might otherwise lead to future electrical failures or hazards.
Expert usage of metal conduit end caps can greatly enhance the durability and safety of an installation. When selecting an end cap, it is crucial to consider the type of conduit being used—whether it's a rigid metal conduit (RMC), intermediate metal conduit (IMC), or electrical metallic tubing (EMT). Each type of conduit may require specific end caps to ensure proper sealing and protection. For instance, RMC requires a thicker and more durable end cap due to its use in heavy-duty applications often exposed to harsh environmental conditions.
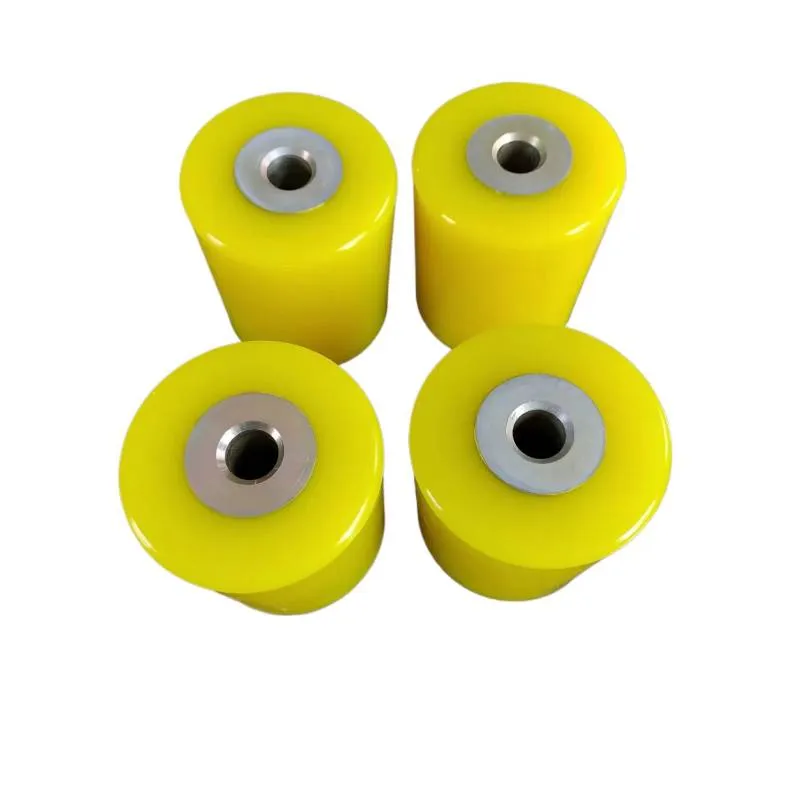
Moreover, the environment in which the conduit is installed dictates the choice of end cap material. Stainless steel end caps, known for their corrosion resistance, are ideal for coastal or industrial settings where exposure to saltwater or chemicals is a concern. On the other hand, aluminum end caps are lightweight and suitable for installations where weight considerations are crucial, without compromising corrosion resistance.
metal conduit end cap
The expertise involved in selecting and installing metal conduit end caps extends to their sizing and fitting. Choosing an end cap that fits too loosely can result in exposure to environmental contaminants, while a cap that is too tight may damage the conduit or be difficult to install properly. Therefore, precise measurements of the conduit diameter are vital. Many professionals recommend using a vernier caliper for accurate measurement, ensuring the end cap fits snugly without gaps.
Authoritativeness in the installation of metal conduit end caps is further demonstrated by adhering to industry standards and regulations, such as the National Electrical Code (NEC). This respected set of guidelines outlines the requirements for electrical components, ensuring installations are safe and compliant. Regular inspections and testing also validate that all conduit end caps remain securely in place and perform their protective role effectively over time.
Trustworthiness as an installer or supplier often comes with product knowledge and an ongoing commitment to quality. Clients rely on experts who not only understand the technical specifications but also maintain up-to-date knowledge on evolving standards and technologies. By collaborating with reputable manufacturers known for rigorous quality control, professionals ensure that the end caps used in their projects meet high-performance criteria and are tested for durability and reliability.
In conclusion, metal conduit end caps might seem like a minor part of an electrical project, yet they are an essential component that upholds the safety and longevity of the entire system. Through informed selection and expert installation, these end caps prevent potential electrical hazards and ensure installation integrity. Awareness of the materials, environment, and regulatory standards associated with metal conduit end caps not only illustrates expertise but bolsters the comprehensive trustworthiness of an electrical professional or firm in delivering reliable service.