Metal bonded sealing washers represent a critical component in various industrial applications, ensuring leak-proof seals in hydraulic and pneumatic systems. As the linchpin of sealing technology, these washers combine the benefits of metal-to-metal contact with the added sealing capability of elastomeric materials bonded within or around them. This unique composition delivers durability, adaptability, and excellent performance even under the most challenging conditions.
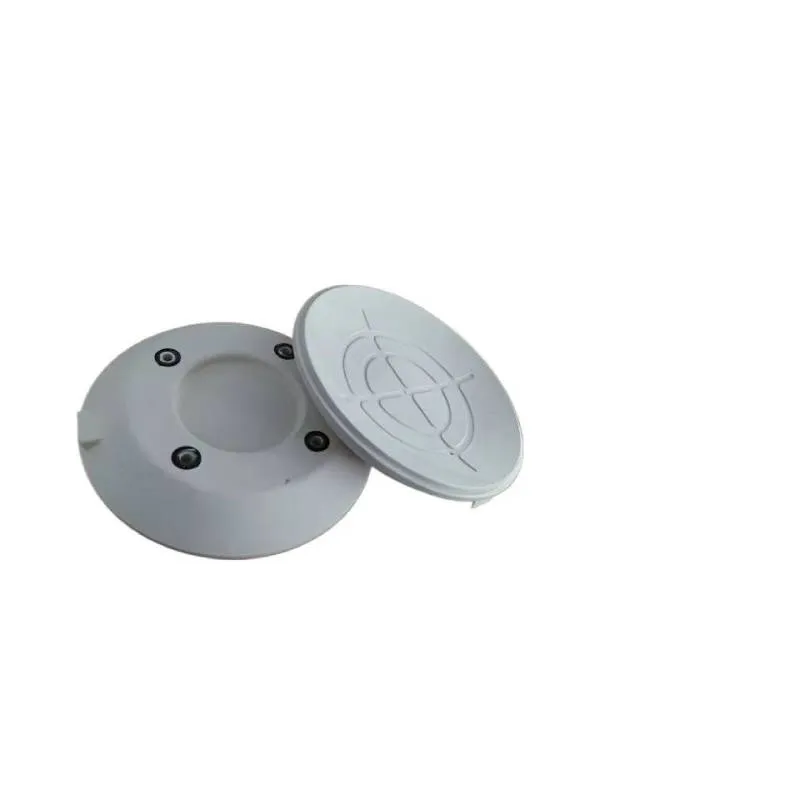
Drawing on extensive field testing and application in diverse industries, metal bonded sealing washers have demonstrated exceptional resilience against high pressure and extreme temperatures. Their design ensures that they can withstand substantial mechanical stress, making them ideal for demanding environments such as automotive, aerospace, and heavy machinery industries. Unlike traditional washers, the metal bonded variant offers a superior seal, effectively preventing leakage of fluids, gases, or contaminants, which can otherwise compromise the integrity of a system.
Expert insight into the development of metal bonded sealing washers reveals a rigorous manufacturing process. Each washer undergoes strict quality control where parameters like bonding strength, material composition, and dimensional accuracy are meticulously verified. Engineers use advanced material science to select the appropriate metals and elastomers that compose these washers. Typically, stainless steel and copper alloys are preferred for their corrosion resistance and strength, while rubber-like materials such as NBR, Viton, or silicone are chosen for their elasticity and temperature tolerance. The interplay of these materials enhances the washer's capacity to deform slightly under load, which effectively cushions the sealing layer and maintains a robust seal even under fluctuating pressures.
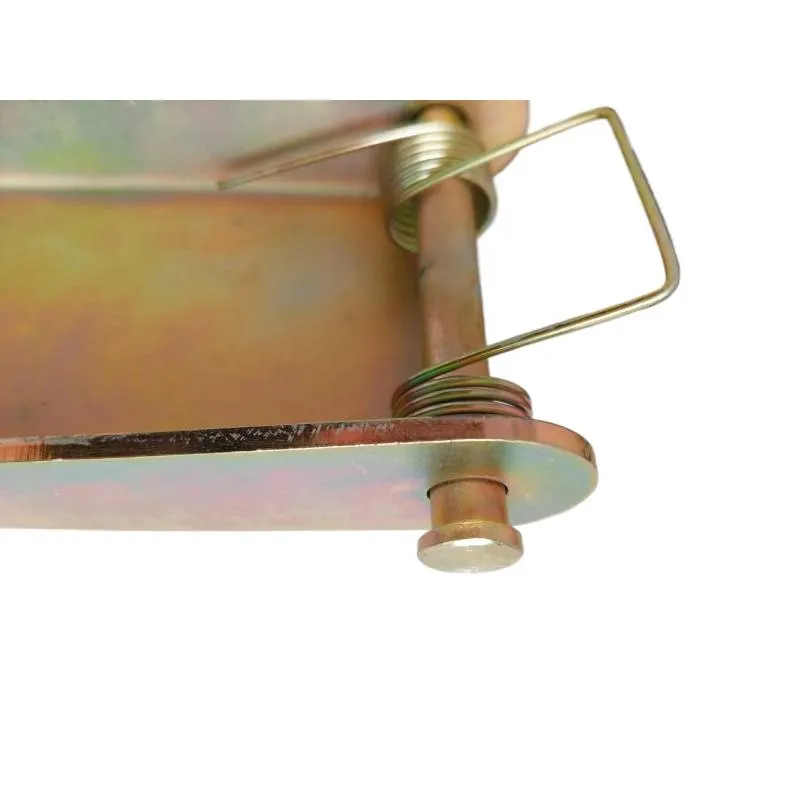
The authority in metal bonded sealing washers is supported by numerous industry standards and certifications. For instance, many washers comply with DIN or ISO standards, ensuring they meet international benchmarks for quality and performance. Manufacturers often provide detailed technical data sheets that outline the operational limits and recommended applications specific to each washer type, enhancing trust and reliability for buyers and engineers who seek stringent operational guarantees.
metal bonded sealing washers
Practical experience further underscores the critical role of these washers in minimizing maintenance costs. By ensuring tight seals, businesses can avert costly downtime associated with leaks and subsequent repairs. Users often report significantly extended service intervals and reduced wear and tear on connected components, which are direct benefits of the washers' integrity. Such feedback validates the trustworthiness and return on investment (ROI) of incorporating metal bonded sealing washers into system designs.
Innovation also plays a pivotal role in the evolving landscape of sealing technology. Recent advancements have seen the inclusion of smart diagnostic features in some washers, enabling real-time monitoring of seal integrity and predictive maintenance alerts. These features exemplify the cutting-edge integration of traditional engineering principles with modern technology to enhance operational efficiency and extend product lifespan.
Finally, sourcing from reputable manufacturers is paramount. Buyers must look for companies with robust supply chains, transparency in manufacturing practices, and proven track records. Retaining open channels of communication with suppliers can further guarantee the delivery of custom solutions tailored to specific industry needs, thus reinforcing both product effectiveness and customer satisfaction.
In conclusion, metal bonded sealing washers stand as a testament to the merging of engineering expertise with practical application. Their intrinsic values of durability, precision, and adaptability make them indispensable in modern industrial settings. By prioritizing quality, adhering to standards, and embracing innovation, these washers not only secure mechanical systems but also play an integral role in advancing the broader goals of efficiency and sustainability in industrial operations.