Large diameter steel pipe end caps hold significant importance in various industrial applications where pipeline systems demand reliable sealing solutions. These components, often overlooked in discussions about piping infrastructure, stand as a testament to the blend of engineering ingenuity and material science. Recognizing the critical need for durable and reliable sealing, manufacturers have innovated in the design and manufacture of these end caps to meet diverse industrial requirements.
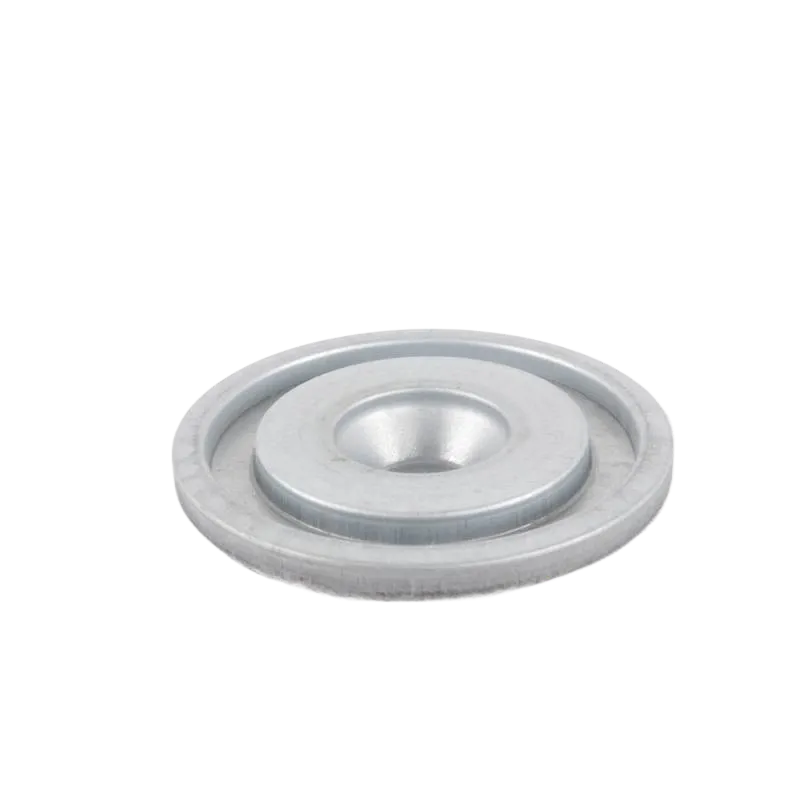
The journey of selecting the appropriate large diameter steel pipe end caps begins with understanding the specific needs of the pipeline system in which they will be used. Not all end caps are created equal; the material, size, and design must match the pipeline's operational demands. The most commonly used materials for these end caps are carbon steel, stainless steel, and alloy steel. Each material offers distinct advantages carbon steel for its cost-effectiveness and durability, stainless steel for its corrosion resistance, and alloy steel for its enhanced mechanical properties under extreme conditions.
One of the most compelling aspects of large diameter steel pipe end caps is their adaptability to different applications. Industries ranging from oil and gas to water treatment, and even construction rely on these end caps to provide a secure seal that protects the integrity of the pipeline and prevents leaks. Such leaks, particularly in critical infrastructure scenarios, can lead to catastrophic failures. Therefore, using a robust end cap is not merely an option but a necessity to uphold safety standards and operational efficiency.
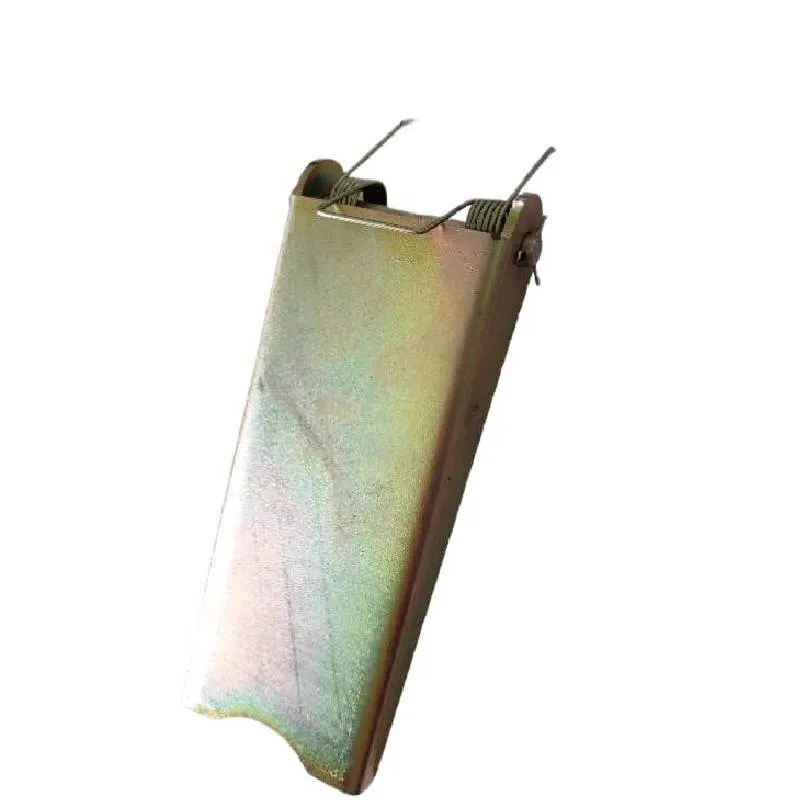
Expertise in manufacturing these components is crucial. The process involves precise engineering to ensure the end caps fit perfectly to the pipe ends. This precision prevents the risk of misalignment, which can compromise the seal's integrity. Advanced fabrication techniques, such as welding and forging, are employed to produce end caps that not only fit securely but also endure the stress and pressure typical of large diameter pipelines.
Experience in the field further highlights the importance of maintenance and regular inspections. Employing end caps made with high-quality materials and superior craftsmanship minimizes the frequency of necessary interventions, thereby reducing long-term operational costs. For instance, an industry veteran might share that end caps made from superior alloys exhibit remarkable endurance in aggressive environments, outlasting their basic steel counterparts by a significant margin.
large diameter steel pipe end caps
To assert authority in the space of large diameter steel pipe end caps, manufacturers often adhere to stringent international standards. Compliance with ASME (American Society of Mechanical Engineers) specifications, for instance, ensures that the products meet global benchmarks for safety and performance. This authority is further solidified by obtaining certifications that endorse quality and reliability, thereby instilling trust among engineers and procurement professionals.
Trustworthiness is also built through transparent customer engagement, from the consultancy phase down to post-purchase support. Reputable manufacturers offer detailed documentation, including technical datasheets and installation guides, which empower end-users to make informed decisions. Moreover, offering extended warranties and responsive after-sales service reinforces trust, assuring clients of the end caps' reliability over their operational lifespan.
A true mark of innovation in the field is the capacity to customize end caps to fit specific pipeline configurations, taking into account unique pressure requirements, temperature ranges, and environmental conditions. This specialization not only maximizes the functionality and safety of pipeline systems but also demonstrates a deep understanding of the various challenges faced by different industries.
The narrative around large diameter steel pipe end caps is evolving as industries demand higher efficiency and reliability from their piping solutions. As experts continue to explore novel materials and manufacturing techniques, these components are becoming more than mere accessories. They are integral parts of a sophisticated system that sustains critical infrastructure, supporting both everyday operations and groundbreaking industrial endeavors. By focusing on experience, expertise, authority, and trust, the industry can further enhance the standing of these vital components in the global market.