Industrial tube fittings are a crucial component in a myriad of industries, from petrochemicals to food processing. Their role in ensuring the seamless connection and efficient flow of gases and liquids cannot be overstated. However, selecting the right tube fittings involves an understanding of various factors that go beyond mere specifications.
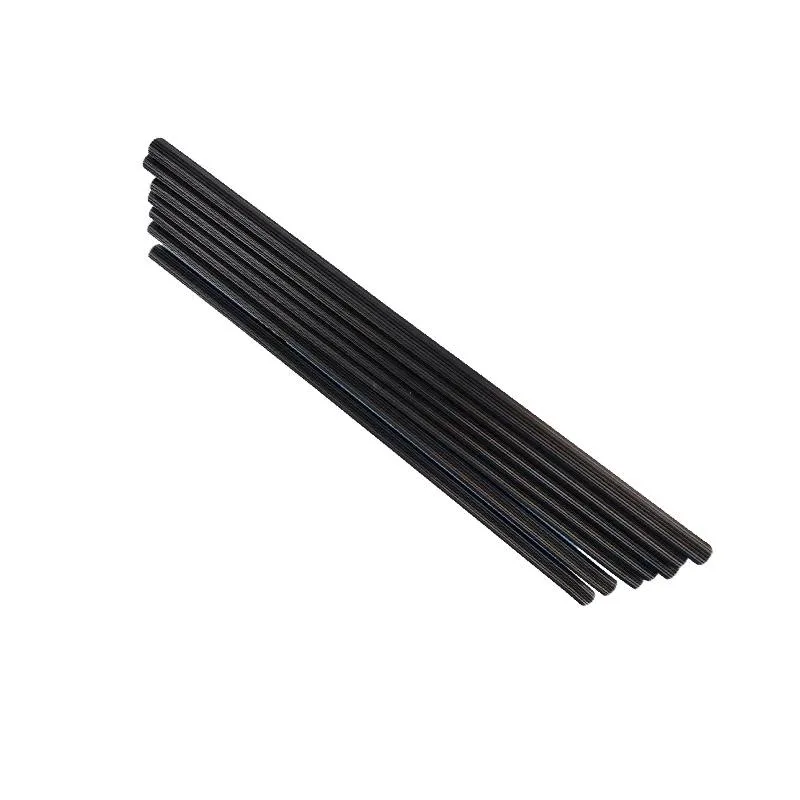
Firstly, a comprehensive knowledge of the materials used in the construction of industrial tube fittings is fundamental. Stainless steel, brass, and plastic composite are popular choices, each selected based on the compatibility with the substances being transported, temperature tolerance, and environmental exposure. Stainless steel fittings, for instance, are favored in industries where corrosion resistance and high-temperature durability are paramount. In contrast, plastic composites offer lightweight solutions with excellent chemical resistance, making them ideal for certain food processing applications.
When evaluating industrial tube fittings, understanding the types of connectors is vital. Compression fittings are widely used due to their ease of installation and reliability under high pressure. Push-to-connect fittings offer speed and convenience, ideal for cost-sensitive operations requiring rapid assembly or frequent disconnection. A seasoned professional understands that selecting the correct connector type can significantly impact operational efficiency and safety.
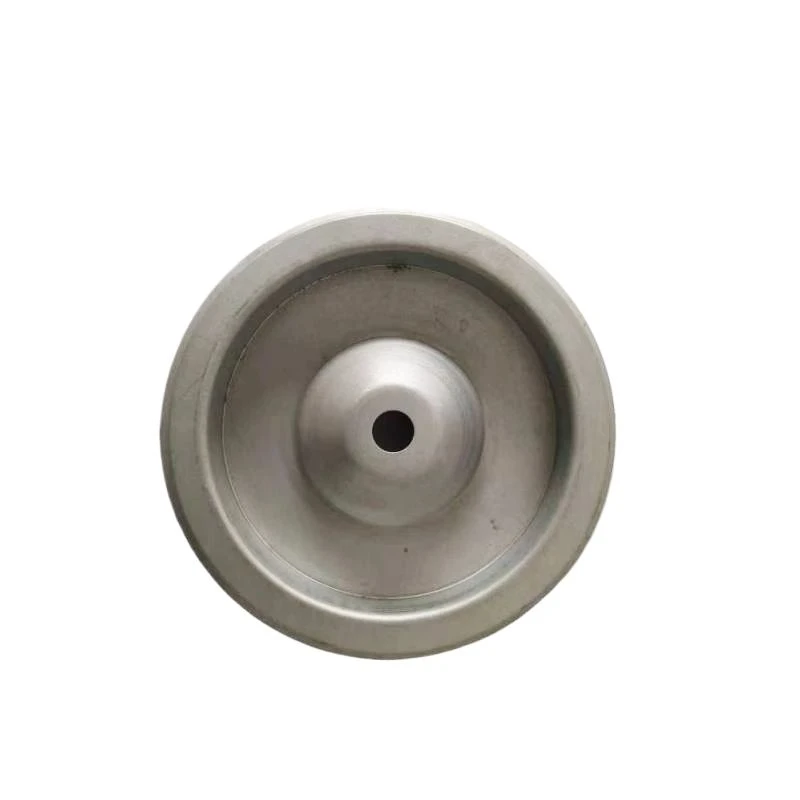
Expertise in industrial tube fittings also involves being well-versed in standards and certifications, such as those from the American National Standards Institute (ANSI) or the International Organization for Standardization (ISO). These standards ensure that the fittings are manufactured to meet rigorous quality and safety requirements. A fitting that complies with these standards offers peace of mind in maintaining system integrity under stress and wear, which is essential for maintaining trust in critical operations.
industrial tube fittings
Moreover, the role of technology and innovation cannot be ignored. The latest advancements in 3D printing and materials science have given rise to fittings that offer better performance and less environmental impact. For example, the advent of AI-driven quality control systems in the manufacturing of tube fittings ensures unprecedented precision and consistency, allowing for predictive maintenance and reduced downtime.
Incorporating the insights of seasoned engineers and technicians can further boost the reliability of the tube fitting system. Real-world experience is invaluable; it helps anticipate potential issues that may not be evident in the design phase, such as the effects of pressure variance and thermal expansion on fitting integrity. Professionals with extensive field experience can provide invaluable advice for fitting selection and installation, guiding decisions that could prevent future failures and costly downtime.
The trustworthiness of an industrial tube fitting supplier is of equal importance. A reputable supplier offers not only high-quality products but also technical support and comprehensive warranties. When evaluating a supplier, it's critical to consider their track record in the industry, their commitment to innovation, and their post-sales support services. Engaging with a supplier that values long-term relationships over short-term sales is key to ensuring reliability and continuity in operations.
In conclusion, selecting industrial tube fittings requires a harmonious blend of technical knowledge, practical experience, and an unyielding commitment to quality. By understanding the materials, stress tolerance, applicable standards, and the credibility of your supplier, you can make informed decisions that protect your operations and ensure peak performance. An experienced professional, armed with deep industry insights, will view tube fitting selection not just as a purchase, but as a strategic decision that directly influences operational excellence and business success.