High pressure O-rings are essential components in various industrial applications, where sealing performance under extreme conditions is paramount. These small yet mighty devices play a crucial role in ensuring the reliability and safety of equipment ranging from hydraulic machinery to aerospace technologies. When selecting the right high pressure O-ring, understanding their materials, design considerations, and application contexts is key to optimizing their performance.
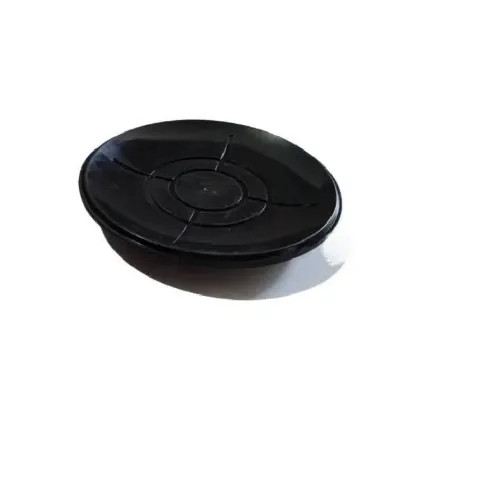
High pressure environments demand O-rings that can withstand significant stress without compromising their integrity. Materials such as nitrile rubber (NBR), fluorocarbon (FKM), and ethylene propylene diene monomer (EPDM) are commonly used due to their durability, resistance to extreme temperatures, and chemical inertness. Each material offers distinct advantages for instance, NBR is favored for its oil resistance, while FKM is ideal for high-temperature environments due to its excellent heat stability.
Design considerations for high pressure O-rings are equally vital. The cross-section of the O-ring must be precisely engineered to distribute pressure evenly, minimizing the risk of extrusion or blowout. The durometer, or hardness, of the material must also match the application's pressure requirements; softer materials might provide better sealing capabilities, but harder materials offer increased wear resistance.
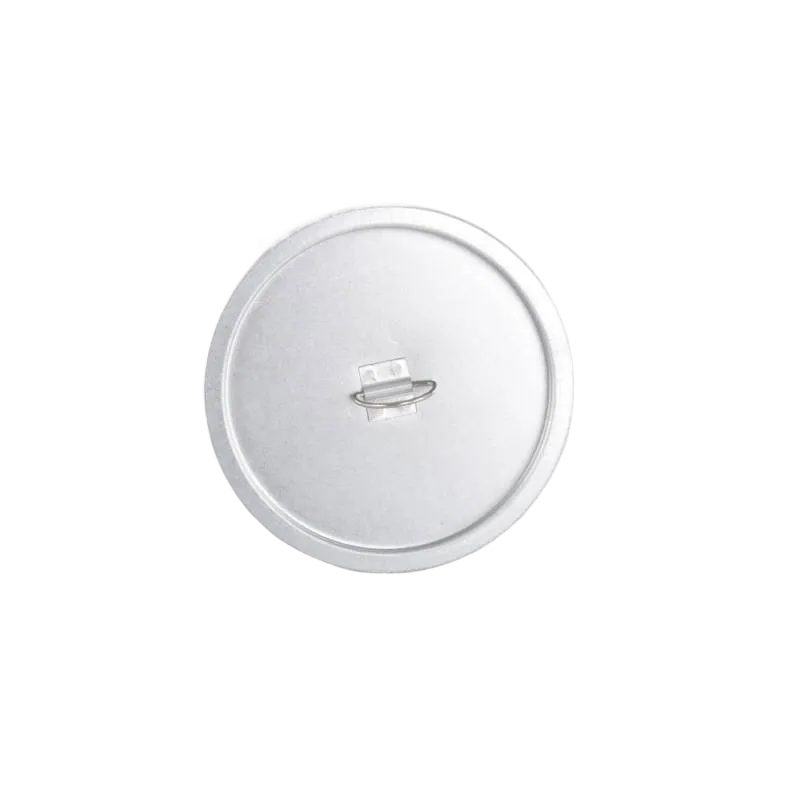
In practical applications, proper installation of high pressure O-rings ensures their effectiveness. The gland design should accommodate the O-ring’s expansion under pressure, and surface finishes of both the O-ring and mating surfaces must be smooth to prevent abrasion. This attention to detail during installation helps maintain the integrity of the seal, preventing leaks that could lead to costly equipment failures or safety hazards.
high pressure o ring
Real-world experiences underscore the importance of choosing the right high pressure O-ring. For example, in hydraulic systems, inadequately specified O-rings can lead to premature failure, causing system downtime and financial losses. Engineers often report success with FKM O-rings in these systems, citing their resilience and ability to maintain a seal under fluctuating temperatures and pressures.
Authoritative testing and compliance with industry standards further bolster the trustworthiness of high pressure O-ring selections. Standards such as those set by the International Organization for Standardization (ISO) and American Society for Testing and Materials (ASTM) provide benchmarks for material quality and performance. Purchasing O-rings from reputable manufacturers who adhere to these standards ensures that the products meet the necessary specifications for safety and reliability.
In conclusion, high pressure O-rings are critical to the safe and efficient operation of complex machinery and systems. By carefully considering material selection, design specifications, and installation practices, engineers can enhance the operational longevity and reliability of these essential components. With firsthand experience and adherence to industry standards, the authority of recommendations and products is reinforced, ensuring consistent performance under the most demanding conditions.