High-Density Polyethylene (HDPE) pipe elbow fittings are indispensable in various industries for their flexibility, durability, and resistance to environmental stressors. In the realm of fluid and gas transport, HDPE pipe elbows serve a pivotal role, particularly when it comes to facilitating changes in flow direction with minimal friction loss and ensuring system integrity. The seamless installation, long-term sustainability, and adaptability of HDPE pipe elbows make them a favored choice among engineers and contractors.
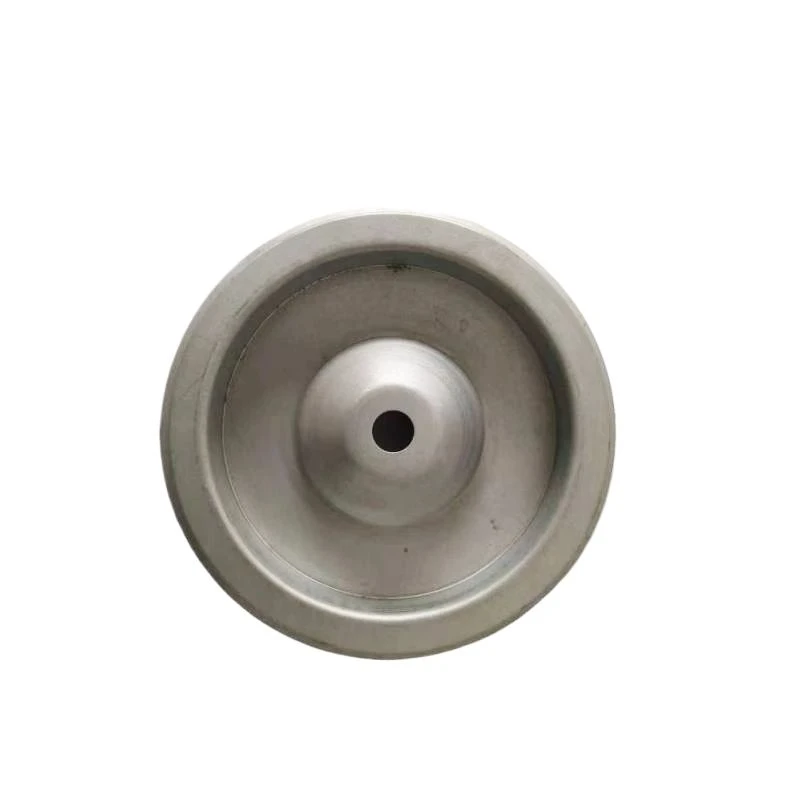
Firstly, the remarkable flexibility of HDPE pipe elbows arises from their inherent material qualities. HDPE has a high bendability factor, allowing it to be molded into various angles to accommodate specific layout requirements. This feature is especially advantageous in complex piping systems where space is a constraint, and angular adjustments are necessary to navigate obstacles. The material’s flexibility means it can absorb shocks and deflections without cracking, thus maintaining the system’s functionality over time.
Secondly,
HDPE pipe elbows boast significant corrosion resistance. In industries such as chemical processing and wastewater management, pipes often encounter harsh chemicals that can degrade traditional materials like metal. HDPE, however, is immune to a wide array of chemical reactions, ensuring the longevity of the piping system. This resilience against chemical attacks not only reinforces the structural integrity of the pipeline but also reduces maintenance costs and frequency, providing a cost-effective solution for industrial fluid handling challenges.
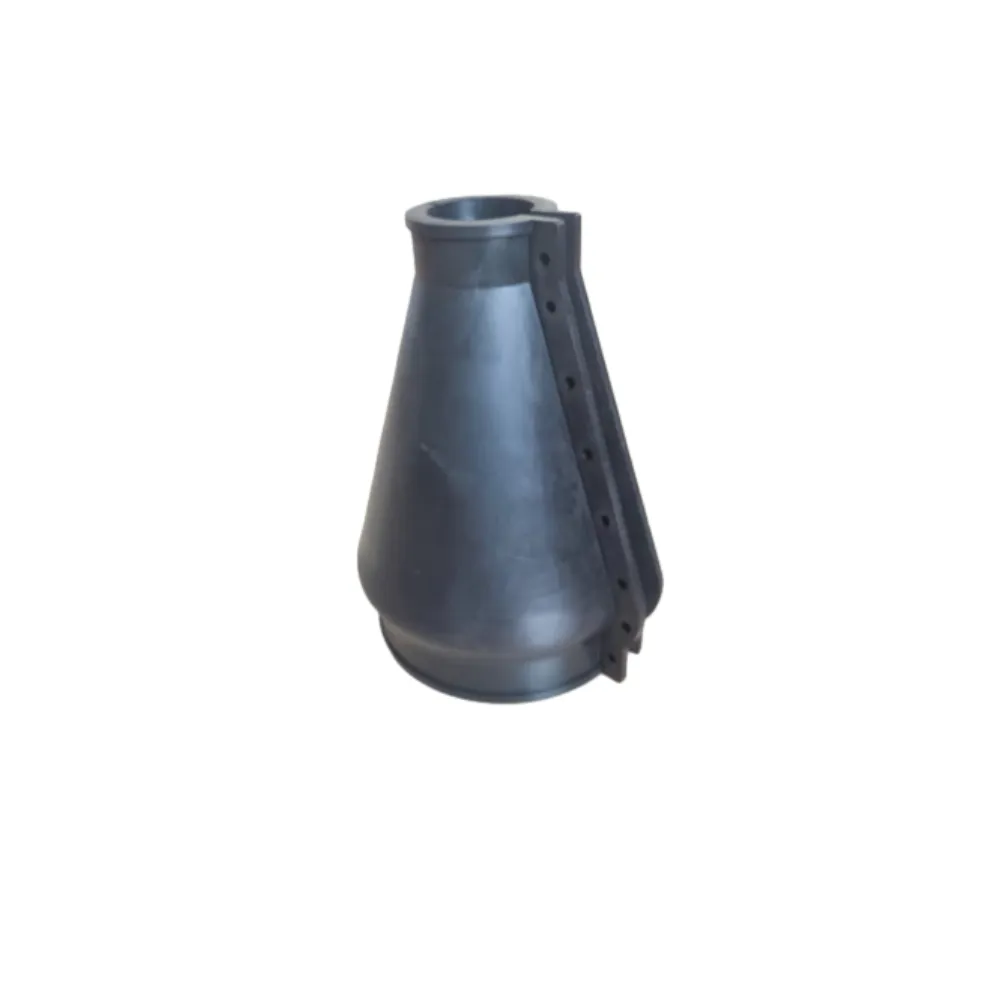
Moreover, the lightweight nature of HDPE pipe elbows simplifies transportation and installation. Unlike heavy metal fittings, HDPE components can be easily maneuvered, reducing the labor intensity and risk of injury during setup. This advantage is complemented by the use of heat fusion techniques in joining HDPE fittings, which creates leak-proof connections that are essential in preventing loss of resources and minimizing environmental hazards. The fusion joints become as strong as the pipe itself, resulting in a homogeneous system free from potential weak points or leakage.
hdpe pipe elbow
In terms of environmental impact, HDPE pipe elbows are exemplary due to their recyclability and low carbon footprint. The production process of HDPE is less energy-intensive compared to conventional pipe materials, and once their life cycle concludes, these elbows can be recycled into new HDPE products. This aligns with global sustainability goals by promoting the use of recyclable materials that do not deplete natural resources.
Industry experts endorse HDPE pipe elbows for their authoritative reliability in diverse applications. Their proven track record in both complex infrastructure projects and everyday plumbing solutions testifies to their versatility and dependability. Professionals with decades of experience highlight the adaptability of HDPE elbows in tackling diverse engineering challenges, endorsing their use based on peer-reviewed studies and practical implementation.
Drawing on trusted sources and firsthand account evaluations, HDPE pipe elbows represent a significant advancement in pipeline technology. Their adaptability, strength, and environmentally friendly attributes not only meet the current troubleshooting requirements but also anticipate the future needs of expanding industries. For stakeholders investing in robust, efficient, and sustainable infrastructure, HDPE pipe elbows emerge as a prudent choice backed by years of field evidence and technical endorsement.