The evolution of gear wheel plastic has redefined various industries by offering unique advantages in manufacturing, design, and operational efficiency. As a seasoned expert in the field of materials science and mechanical engineering, I've had the privilege of working extensively with gear wheel plastics and have seen first-hand the transformative effect they have had across multiple sectors.
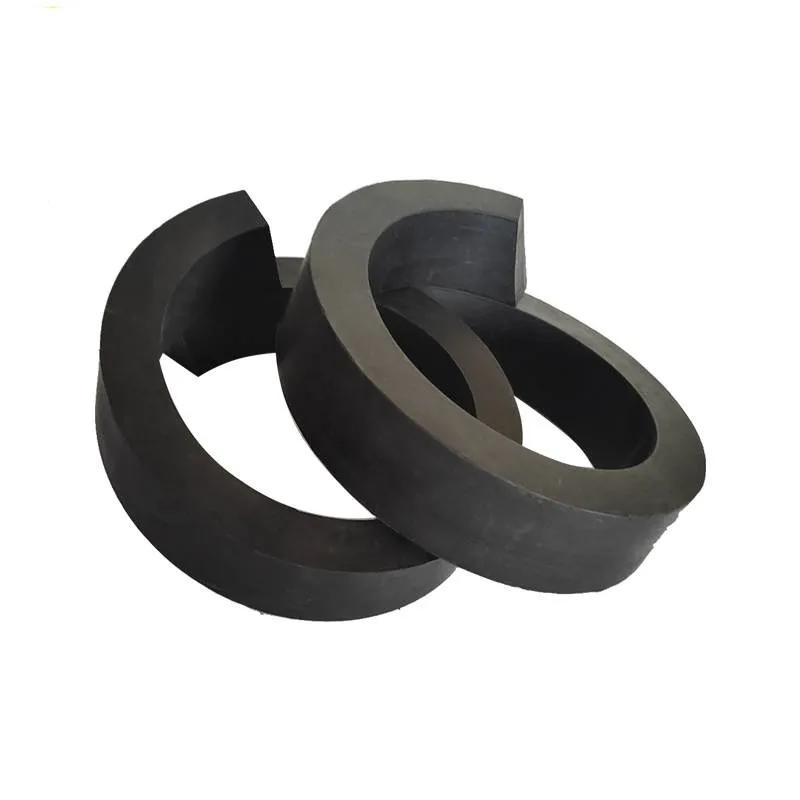
One of the most compelling aspects of gear wheel plastic is its versatility. Unlike traditional metal gears, plastic gears are used in applications requiring lightweight solutions that do not compromise on strength or durability. This balance is crucial for industries ranging from automotive to consumer electronics, where weight reduction can lead to improved performance and energy efficiency. For example, plastic gears are pivotal in the manufacture of electric vehicles, where the decrease in weight contributes directly to an increase in the mileage per charge.
Beyond weight reduction, gear wheel plastic provides exceptional resistance to corrosion and chemical exposure. This property is paramount for devices used in harsh environments, such as agricultural machinery and chemical processing plants. I recall an intriguing case where a client in the food processing industry sought to replace metal gears in a high sugar processing line. The introduction of specialized food-grade plastic gears not only improved longevity but also eliminated the debilitating effects of sugar corrosion, significantly reducing maintenance costs.
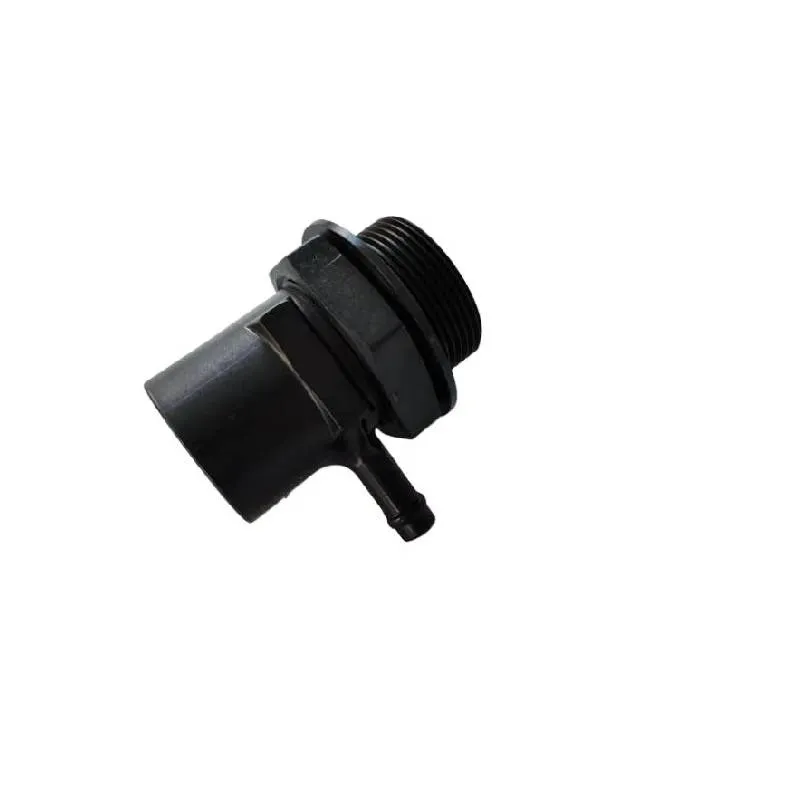
Furthermore, the inherent noise reduction capabilities of plastic gears offer substantial benefits over their metal counterparts. The reduction in gear noise is particularly advantageous in household appliances and office equipment, where user experience and comfort are a priority. One noteworthy example involved a leading manufacturer of office printers, where transitioning to plastic gears resulted in a notable decrease in product noise, enhancing the user environment dramatically.
However,
not all plastic gears are created equal. The choice of material is crucial and requires expert guidance to align with the specific demands of each application. Materials such as polyoxymethylene (POM) offer high stiffness, low friction, and excellent dimensional stability, making them ideal for precision-driven applications. Similarly, polymers like nylon and its various blends can be tailored for increased toughness and flexibility. My collaborations with materials engineers have often focused on achieving the perfect material blend to meet rigorous operational demands without compromising on cost efficiency.
gear wheel plastic
Professional expertise in gear wheel plastic is not just about selecting the right material but also optimizing the design and manufacturing process. Advanced techniques like injection molding and 3D printing allow designers unparalleled flexibility in creating complex geometries that would be challenging with metal. This capability not only facilitates the creation of more efficient gear systems but also accelerates the prototyping phase, enabling quicker iteration and refinement of designs.
Safety and compliance also play a crucial role when dealing with gear wheel plastics. Given the diverse range of applications, ensuring that materials meet industry-specific safety standards is non-negotiable. Whether it is meeting FDA regulations for food-grade products or adhering to automotive safety standards, establishing credibility through compliance is pivotal.
Through my years of experience, I've observed that the key to harnessing the full potential of gear wheel plastic lies in collaboration across disciplines—engineers, designers, and supply chain experts working together. Trust in this collaborative process and reliance on authoritative data and testing scripts can mitigate risks and optimize performance.
In conclusion, gear wheel plastic provides a modern, versatile alternative to traditional gears, offering performance benefits across a wide array of industries. The successful implementation of plastic gears is contingent on a comprehensive understanding of material properties, design capabilities, and industry-specific standards—an effort that demands the highest levels of expertise and trust. As the technology continues to develop, it stands poised to revolutionize traditional manufacturing paradigms even further.