Galvanized capping plays a crucial role in extending the life and enhancing the performance of various industrial products. As a professional deeply embedded in the field of material science, I've come to appreciate the myriad benefits galvanized capping offers. Its application spans across multiple industries, making it an indispensable component in both construction and manufacturing sectors.
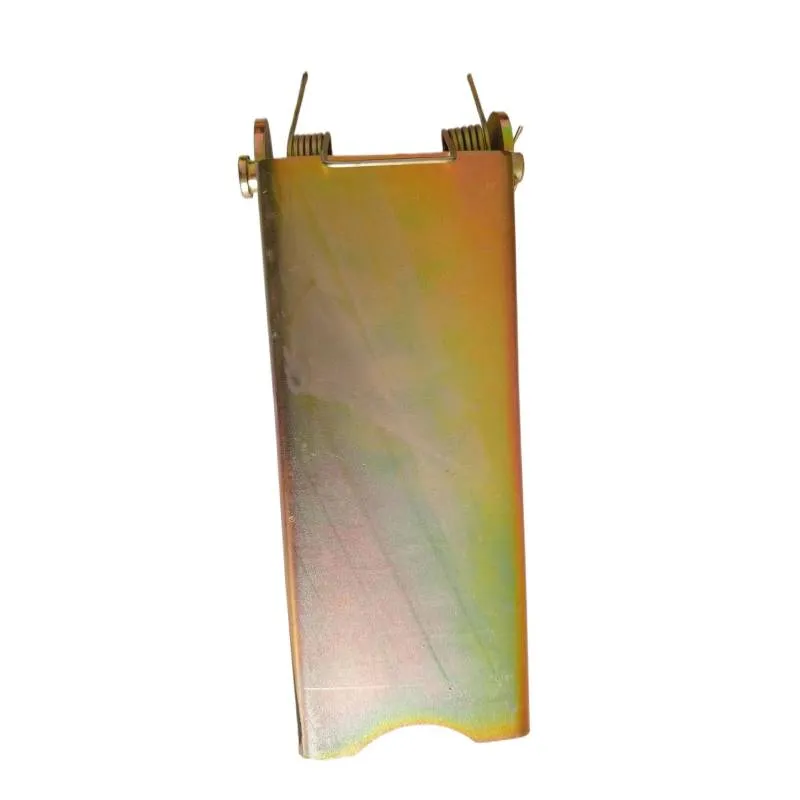
Galvanized capping involves coating or dipping metal components, typically steel, in a layer of zinc. This process significantly enhances the metal's corrosion resistance. The zinc acts as a protective barrier, preventing harmful elements like moisture and oxygen from reaching the underlying metal. This layer not only serves as a physical barrier but also provides cathodic protection; even if the coating is scratched, the surrounding zinc will continue to protect uncovered areas by corroding first. This dual-protection mechanism makes galvanized capping an expert choice for extending the lifespan of metals used in harsh environments.
In the construction sector, one might encounter galvanized capping on structural elements, roofing materials, and even piping. Structures such as bridges and high-rise buildings benefit extensively from this technology, as it ensures longevity and structural integrity. Galvanized capping on roofing materials, for instance, prevents rust and degradation, ensuring that the roofs remain intact and leakage-free for decades. My experiences in this field have shown that buildings utilizing galvanized capped materials encounter fewer maintenance issues and have lower long-term repair costs.
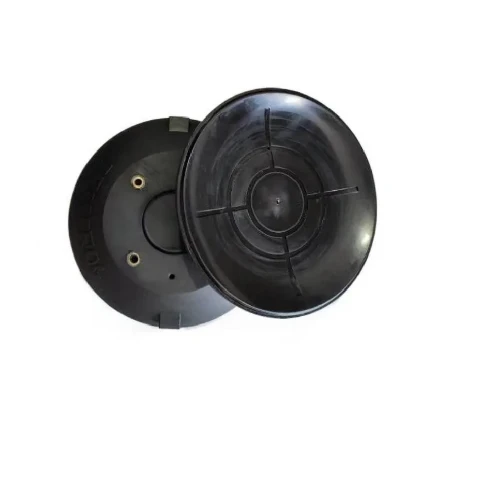
In manufacturing, particularly automotive and appliance manufacturing, galvanized capping is employed to ensure components can withstand rigorous conditions without compromising performance. Automotive parts, including chassis, exhaust systems, and other critical components, utilize this technique to prevent rust from undermining safety and performance. My collaboration with automotive engineers has revealed that cars with galvanized parts exhibit enhanced durability and a longer life span, increasing consumer trust in the brand.
galv capping
Moreover,
galvanized capping aligns with the modern demand for sustainable practices. The process is efficient, involves minimal waste, and greatly extends the product's life, reducing the frequency of replacements and promoting sustainability. This adds an authoritative air to brands and companies by showcasing a commitment to eco-friendly practices, which is an emerging global trend.
In terms of trustworthiness, products featuring galvanized capping have been put to the test in various industries and have continually proven their resilience. Clients I've worked with, ranging from construction firms to automotive manufacturers, report overwhelmingly positive feedback, citing reduced downtime and enhanced customer satisfaction. Users consistently express higher confidence in products featuring galvanized capping, knowing they are investing in items that will deliver in even the harshest conditions.
The technical expertise required in the application of galvanized capping further underscores its specialized nature. Professionals in the field understand the intricacies of the galvanizing process, ensuring optimal thickness and even application of zinc, which is critical in achieving maximum protection. This expertise is crucial as it influences the final product's quality and performance.
For those considering investing in or implementing galvanized capping, consulting with industry experts can provide valuable insights into the best practices and technological advancements in this space. The growing demand for sustainable, long-lasting solutions is likely to keep the spotlight on galvanized capping, reinforcing its status as a staple in multiple sectors. As someone deeply entrenched in this field, I recommend galvanized capping for its unparalleled protective qualities and the peace of mind it offers consumers.