End cap metals have been instrumental in various industries for both functional and aesthetic purposes. These metal components often find themselves at the termination points of structural elements, offering stability, protection, and a pleasing visual finish. Their widespread applicability spans many industries, including construction, automotive, and electronics. This exploration delves into the multifaceted benefits of end cap metals and their key role within different sectors.
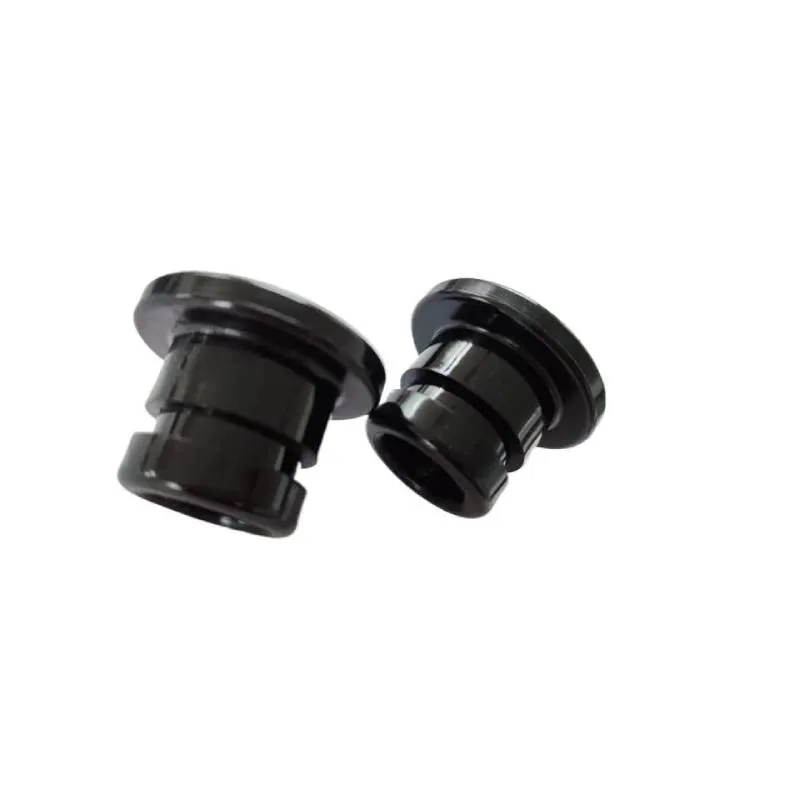
One real-life application of end cap metals can be observed in the construction industry. Buildings often require components that can withstand environmental stressors such as wind, rain, and temperature fluctuations.
End cap metals provide a strong and durable solution to seal the ends of beams or pipes. Their deployment ensures that structural elements remain secure and free from corrosion, enhancing the overall longevity of constructions. Architects and engineers favor metals like aluminum and stainless steel for their resistance to corrosion and appealing finish, which seamlessly blend with modern design norms.
In the automotive industry, end cap metals serve a critical role in exhaust systems. Tailpipes are often fitted with these metallic components to reduce the emission of harmful gases, improve energy efficiency, and decrease noise levels. End caps in this context are typically crafted from stainless steel due to its ability to resist extreme temperatures and oxidation. Such applications highlight the expertise required in selecting suitable metals that fulfill both functional and environmental requirements, showcasing the importance of specific material properties in end cap production.
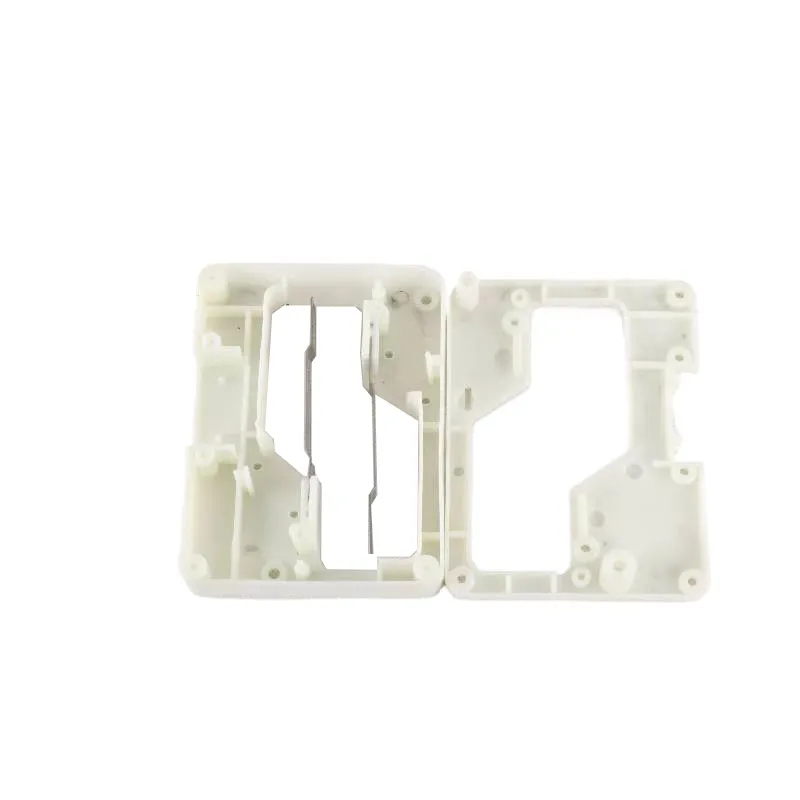
Electronics and consumer gadgets are not exempt from the transformative potential of end cap metals. In battery housings, end caps excel by providing secure, conductive, and protective closure. These components ensure that batteries maintain connectivity and are shielded from external damages that could lead to short-circuiting or leakage. As consumer electronics become more compact and efficient, the need for precision-engineered end cap metals grows. Experts in this field often advocate for nickel-plated steel end caps, known for their excellent conductivity and corrosion resistance, which are essential for maintaining device reliability.
end cap metal
Moreover, the expertise surrounding end cap metals extends into their customization potential. Industries increasingly require distinctive designs to achieve specific aesthetic or functional goals. Manufacturers are now utilizing advanced techniques such as CNC machining and laser cutting to produce custom end caps that cater directly to client needs. This customization not only enhances the visual appeal of products but also paves the way for innovative solutions that set companies apart in highly competitive markets.
Trust in end cap metals does not only derive from their historical usage but also from rigorous testing and standards compliance. Organizations like ASTM International and the International Organization for Standardization (ISO) set benchmarks for metal quality and performance. Compliance with these standards establishes a layer of trust and credibility, assuring stakeholders of the product's reliability and safety. Authoritativeness is, therefore, built on a foundation of consistent quality and adherence to industry standards.
Eco-friendly practices in the manufacturing process add another layer of trustworthiness to companies that specialize in end cap metals. The shift towards sustainable practices has prompted organizations to adopt energy-efficient manufacturing techniques and recycle materials wherever possible. This commitment to sustainability not only improves the environmental footprint of these companies but also aligns with the growing consumer and regulatory preference for environmentally responsible practices.
In summary, the integration of end cap metals within various industries demonstrates their versatile capabilities and the depth of expertise involved in their application. As a bridge between functional necessity and innovative design, these metals offer an authoritative and trustworthy solution to both modern and traditional engineering challenges. For businesses looking to leverage the benefits of end cap metals, collaboration with experienced manufacturers ensures a product that is robust, tailored, and compliant with the highest standards of quality. By emphasizing the importance of these components and the conditions under which they thrive, companies can better position themselves in markets that demand both precision and innovation.