1. Rubber Bowl Market & Technology Trends
In 2023, the rubber bowl market showed continued growth with the global industrial automation sector. According to Grand View Research, the global industrial rubber products market—including rubber bowls, small rubber caps, and rubber protective caps—was valued at USD 119.9 billion in 2023, forecasted to expand at a CAGR of 4.2% from 2024 to 2030. With rising demand for efficient material handling, dust sealing, chemical resistance, and custom protection in industries such as petrochemical, metallurgy, wastewater treatment, and precision engineering, new technologies and materials for rubber bowl manufacturing are becoming industry drivers.
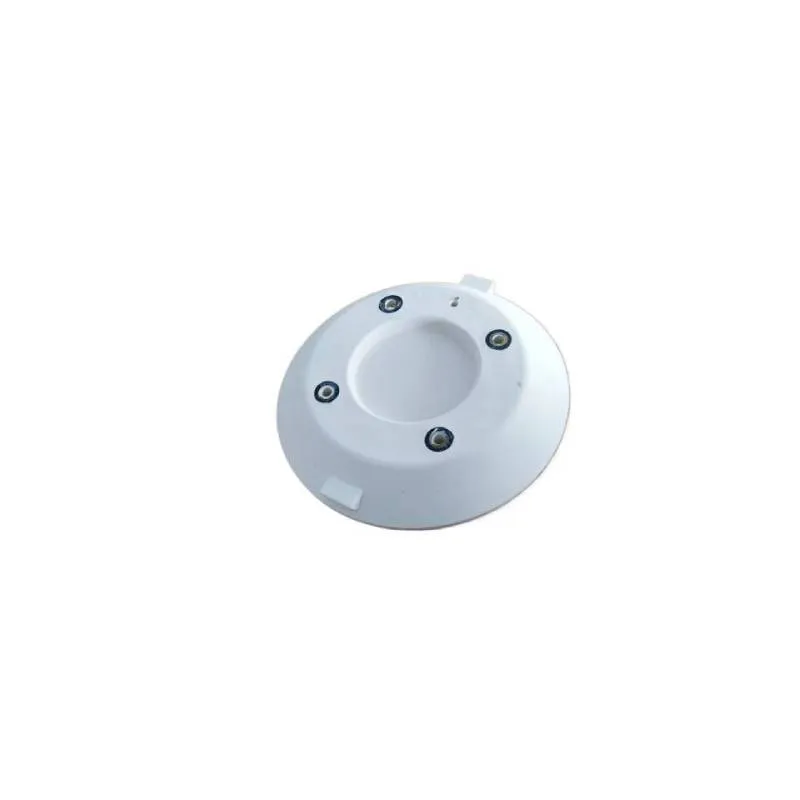
- Increased adoption of high-performance elastomers (such as FKM, HNBR, Silicone) for longer lifespan and chemical resistance
- New standards (ISO 3601, ANSI/SAE J549) regulate production tolerances and service life of rubber sealing and suction products
- Technological upgrades: from manual molding to CNC-aided precision casting, improving consistency and scalability for high-mix, low-volume orders
- Sustainable manufacturing: use of recyclable elastomers and greener curing processes
- Over 8.1 million rubber bowls produced globally in 2023
- 70% are used in automation, robotics end-effectors, and fluid handling equipment
- ISO 9001 and FDA certification requirements are considered standard for major overseas projects
2. Product Overview: Rubber Vacuum Suction Cup, Small Rubber Caps & Rubber Protective Caps
The rubber vacuum suction cup is a specialized type of rubber bowl designed for precision gripping, movement, and automation. Small rubber caps and rubber protective caps serve as dust-proof, chemical-resistant, and impact-shielding solutions across diverse industries.
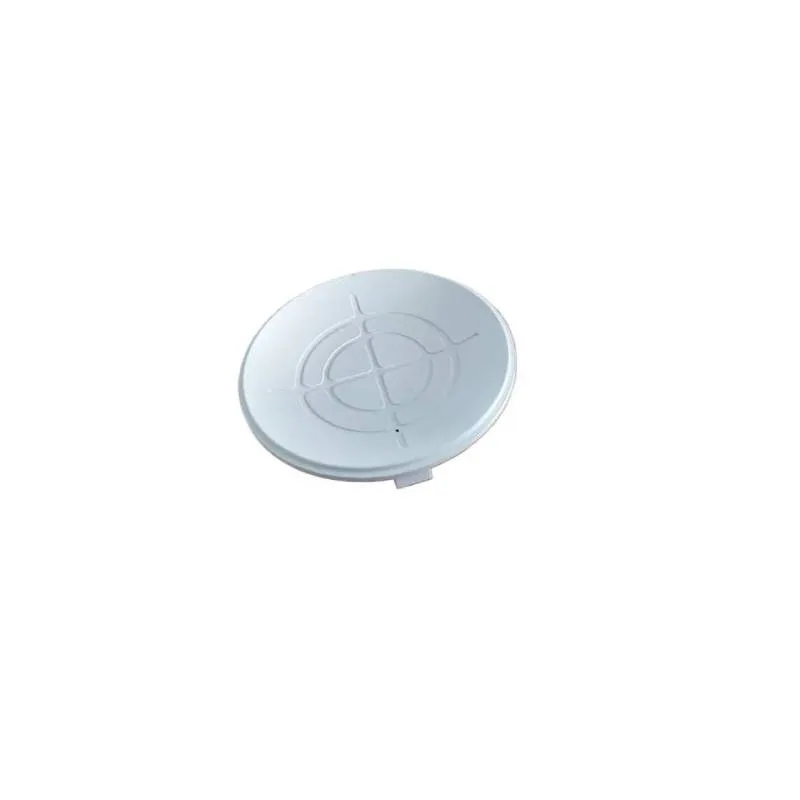
Parameter | Rubber Bowl | Small Rubber Cap | Rubber Protective Cap |
---|---|---|---|
Material | NBR / EPDM / FKM / Silicone | EPDM / Silicone / FKM | NBR / PVC / Custom Polymer |
Hardness (Shore A) | 45-80 | 40-70 | 45-60 |
Temperature Range (°C) | -40 ~ +210 | -50 ~ +200 | -30 ~ +180 |
Applicable Standards | ISO 3601 / DIN 3760 | ANSI/SAE J549, RoHS | FDA, ISO 9001 |
Service Life (cycles) | ≥1 million | ≥0.5 million | ≥0.3 million |
Chemical resistance | High | Moderate | High |
Typical Application | Material handling, automation, fluid systems | Wire terminal sealing, dust protection | Pipe end cover, impact & corrosion protection |
Selecting the right material (e.g., FKM for aggressive chemicals, Silicone for high temperatures) is critical to rubber bowl performance in demanding applications.
3. Manufacturing Process: How Rubber Bowl & Vacuum Suction Cup Are Made
(Process Video Reference: Rubber Suction Cup Manufacture on YouTube)
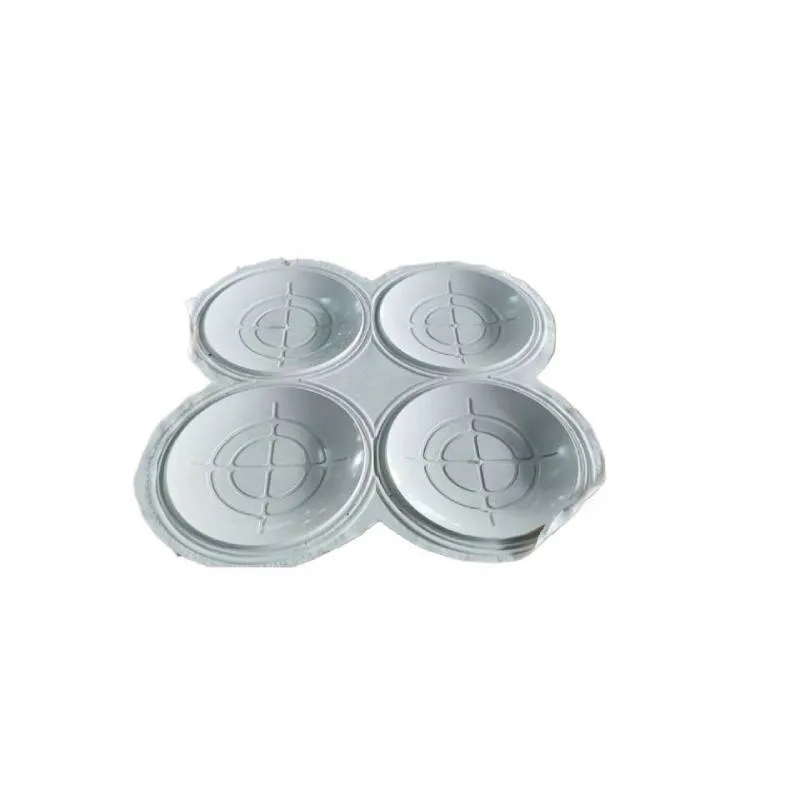
- Casting & Forging: Low-volume custom rubber bowls may use manual casting for initial samples; mass production shifts to steel-tooled compression molding
- CNC Processing: Provides finishing accuracy up to ±0.05mm, ideal for high-precision vacuum cups in electronics assembly
- QA Standards: Each batch is checked per ISO 3601 (dimensional accuracy), FDA 21 CFR 177.2600 (for food-grade rubber)
- Service Lifetime: Products typically achieve over 1 million cycles in robotic pick-and-place testing
4. Technical Specifications & Manufacturer Comparison
Manufacturer | Material Range | ISO/FDA Certifications | Min. ID/OD (mm) | Service Life (cycles) | Customization | Reference Project / Partner |
---|---|---|---|---|---|---|
FYgasket | NBR, EPDM, FKM, Silicone, HNBR | ISO 9001, FDA 21CFR | 2/7 | 1~2 million | Full (Logo/Molding/Compound) | Siemens, Dow Chemical |
SMC | NBR, Polyurethane, Silicone | ISO 9001 | 3/8 | 1 million | Partial | Nissan, FANUC |
Piab | Silicone, Polyurethane | FDA, ISO 9001 | 5/12 | 800,000 | Partial | ABB Robotics |
Parker | NBR, EPDM, FKM | ISO 9001 | 4/10 | 700,000 | Limited | BASF, Magna |
- FYgasket offers broad polymer options, advanced CNC post-processing, and full customer custom branding for rubber bowl solutions
- All leading OEMs adhere to ISO 9001 for QA and traceability; FDA grade is crucial for food/pharm applications
- Longer service life and tighter tolerance achieved via strict process control and material R&D
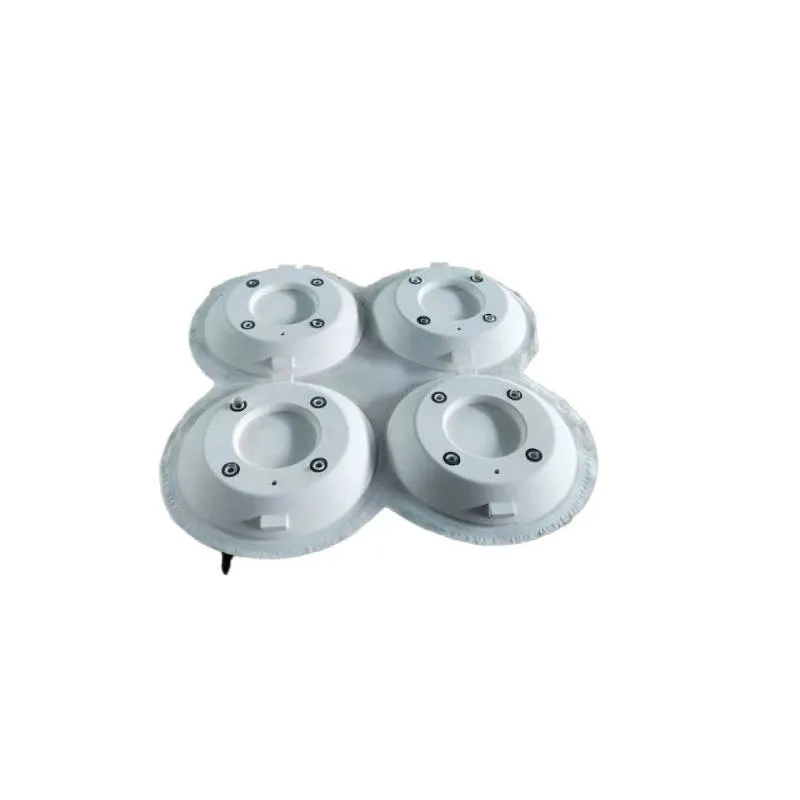
5. Data Visualization: Performance Parameters of Rubber Bowl & Vacuum Suction Cup
6. Application Scenarios & Real-World Case Studies
- Automation End Effectors: Rubber bowl suction cups grip and move delicate panels, glass, and PCBs in robotic pick-and-place systems
- Chemical Pipeline End Caps: Rubber protective caps safeguard pipe ends from corrosive attack and particle ingress during construction or overhaul
- Electronics Assembly: Small rubber caps seal connectors, protecting sensitive circuits from dust and moisture in production lines
- Pharmaceutical & Food: FDA-grade rubber bowls support contamination-free vacuum lifting in cleanrooms
- Water Treatment: Large-diameter rubber bowls operate as check valve backs in high-pressure water hammer prevention systems
- In 2023, FYgasket supplied more than 240,000 rubber vacuum suction cups for robotic drum handling lines in a major Saudi petrochemical expansion. Custom FKM blends were validated in 96-hour salt spray and aggressive solvent tests (per ISO 9227, ISO 1817).
- Recorded field service life exceeded 1.6 million cycles per unit, 35% longer than previous caps. Customers cited reduced downtime and maintenance by 22% in year-on-year OEE audits.
7. Supplier & Customization Solutions
FYgasket, as a verified ISO 9001 & FDA-certified manufacturer, offers one-stop solutions for rubber bowl, small rubber caps, and protection covers.
Customization Workflow:
- Design validation: CAD and FEA simulation support for geometries and assemblies
- Material selection consultation: Based on detailed media and temperature exposure info
- Prototype production: 7-14 days lead time using rapid tooling or 3D printing
- Mass production: Full mold manufacturing and high-throughput molding lines for scalable volumes
Minimum Order: From 100 pcs for standard types; for custom tooling, starts at 500 pcs.
8. FAQ: Key Technical Terms – Answered
-
Q1: What is the difference between NBR, FKM, and Silicone used in rubber bowls?
A: NBR (Nitrile) is excellent for oil and general purpose; FKM (Viton) offers superior chemical and temperature resistance; Silicone suits high/low temp, FDA, but has weaker tear strength. -
Q2: What “Shore A” hardness range is optimal for vacuum suction cups?
A: Most rubber bowl suction cups use Shore A 45-70, balancing flexibility with grip strength, per ISO 7619 standard. -
Q3: How are sizes specified for small rubber caps?
A: ID (inner diameter), OD (outer diameter), and overall height in mm; typically, DIN 46244 or SAE J549 standards guide the measurement and fit tolerances. -
Q4: Are FYgasket’s rubber protective caps food safe?
A: Yes, options available certified per FDA 21CFR177.2600 and free from phthalates. -
Q5: What installation standards apply to rubber vacuum suction cups?
A: Thread/quick coupling ISO/DIN types accepted; ensure mounting meets cup-specific compression/deflection specs for repeatability. -
Q6: Can I order custom color or logo for rubber bowls?
A: Absolutely, FYgasket supports full color customization and permanent logo marking at production batch scale. -
Q7: What QC/Testing is performed before shipment?
A: 100% automated optical inspection, random sample destructive tests for tensile, compression set (ISO 815), and resistance to chemicals per ISO 1817.
9. Delivery, Warranty & After-sales Support
- Lead Time: Standard rubber bowl and suction cups: 3-6 days (
- Quality Guarantee: 13 months warranty against manufacturer defects; free replacement for documented field failures.
- Customer Service: 24/7 technical support (by email/WhatsApp); onsite assistance available for OEMs.
- Certificates: All shipments include ISO 9001:2015, FDA, ROHS and materials traceability report.
10. Authoritative References & Further Reading
- Industrial Rubber Products Market Size Report, 2024-2030 (Grand View Research)
- ASME Journal of Fluids Engineering: Vacuum Seal & Bowl Applications
- Rubber Bowl Selection Forum Thread (eng-tips.com)
- MDPI Polymers: Studies on Advanced Rubber Materials
- ISO 3601:2012 - Fluid Power Systems, O-ring & Seal Tolerances