In the realm of precision engineering, drilled aluminum washers have emerged as an indispensable component, renowned for their ability to enhance both functionality and durability in various applications. With an extensive background in materials science, I have witnessed firsthand how these modest yet critical components can contribute to optimized mechanical performance and reliability. This article delves into the significance, application, and advantages of drilled aluminum washers, highlighting the extensive expertise and authority that underpin their usage in today's advanced technological landscapes.
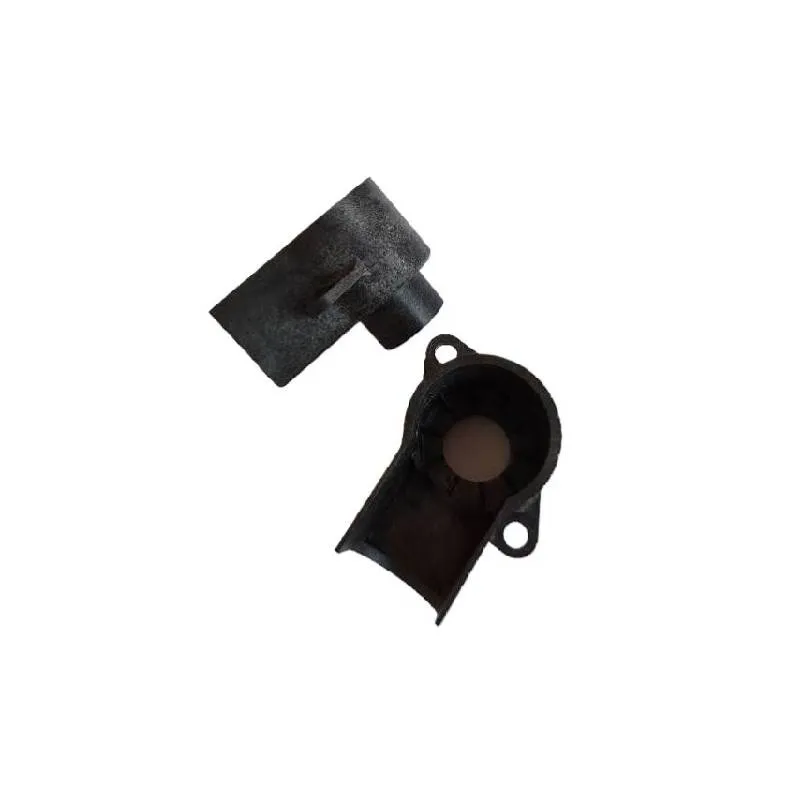
Drilled aluminum washers are engineered components designed to distribute load and reduce friction within mechanical assemblies. Unlike standard washers, drilled variants include holes or perforations, meticulously crafted to meet specific engineering criteria. This unique feature allows for various advantages such as enhanced weight reduction, improved distribution of lubricants, and efficient heat dissipation, all of which are crucial in high-performance and high-precision environments.
One of the primary applications of drilled aluminum washers is in aerospace engineering. The lightweight properties of aluminum, combined with the structural benefits derived from the drilled design, make these washers ideal for aircraft assembly. They help maintain structural integrity while minimizing additional weight. Moreover, the drilled design allows for effective fluid flow in hydraulic systems, a factor of utmost importance in environments where precision and safety are paramount.
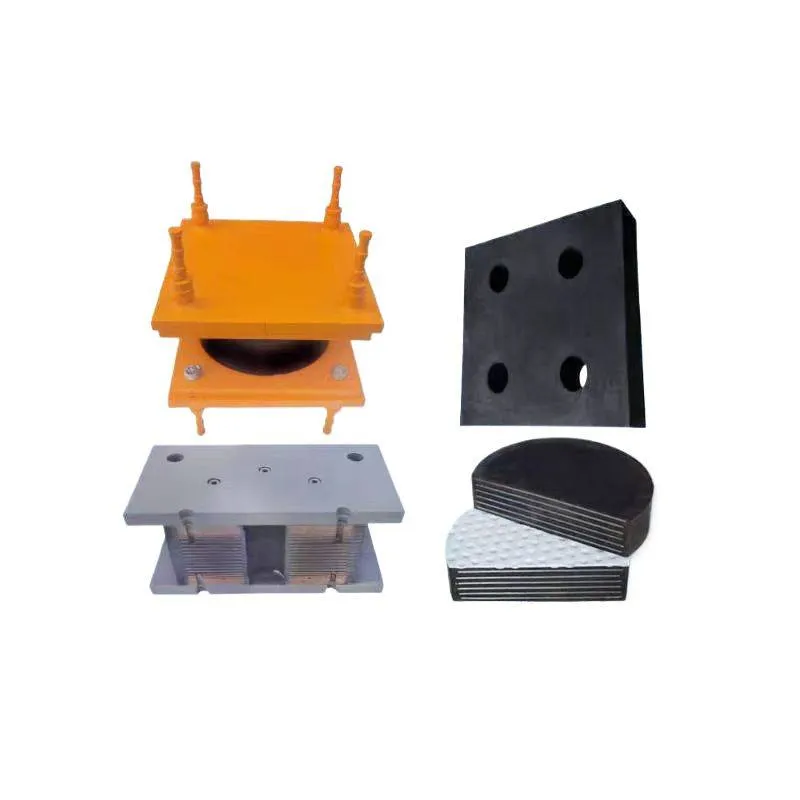
Furthermore, in the automotive industry, drilled aluminum washers find extensive use in engine assemblies and braking systems. Their ability to withstand thermal and mechanical stress while contributing to weight efficiency makes them preferred components in performance vehicles. The drilled configuration ensures optimal distribution of thermal energy, reducing the risk of overheating and improving overall system reliability.
The expertise involved in manufacturing drilled aluminum washers is rooted in precision engineering. Each washer is engineered using advanced CNC machinery to ensure exact conformity to specified dimensions. This precision is critical; even a minute deviation can lead to mechanical failure, underscoring the importance of rigorous quality control practices. The production process leverages advanced metallurgy, ensuring that each washer possesses the requisite mechanical properties to perform under high stress and extreme environmental conditions.
drilled aluminum washers
From a materials science perspective,
the choice of aluminum as the base material for these washers is deliberate. Aluminum offers an exceptional strength-to-weight ratio, corrosion resistance, and the capacity for high thermal conductivity. Such characteristics are essential for applications that demand not only strength but also durability and resilience against environmental factors.
As an industry authority, trust in the quality and reliability of drilled aluminum washers stems from adherence to stringent standards and specifications set by both industry and governing bodies. These standards ensure that every washer is fit for purpose, capable of performing reliably in critical applications where failure is not an option. Established manufacturers conduct comprehensive testing on their products, including stress tests, thermal cycling, and fatigue analysis, all contributing to a high level of trust in these components.
In terms of sustainability, the utilization of aluminum aligns with increasing global efforts to implement environmentally friendly materials in manufacturing. Aluminum is inherently recyclable, and its lightweight nature contributes to reduced energy consumption in applications like transportation and aerospace, where fuel efficiency is a persistent concern. This eco-friendly aspect is an additional layer of assurance that aligns with modern environmental standards.
Choosing drilled aluminum washers for your engineering needs signifies a commitment to quality, performance, and innovation. Their unique combination of structural ingenuity and material excellence makes them an indispensable component in sophisticated mechanical systems. Leveraging these components not only improves immediate operational outcomes but extends the longevity and reliability of entire systems, contributing to sustainable engineering practice.
Through the lens of my professional journey in material engineering and component design, embracing drilled aluminum washers epitomizes a fusion of expertly crafted engineering solutions with the reliability that only established industry expertise can offer. This fusion is the hallmark of excellence that translates to real-world performance, fostering trust and authority in engineering applications globally.